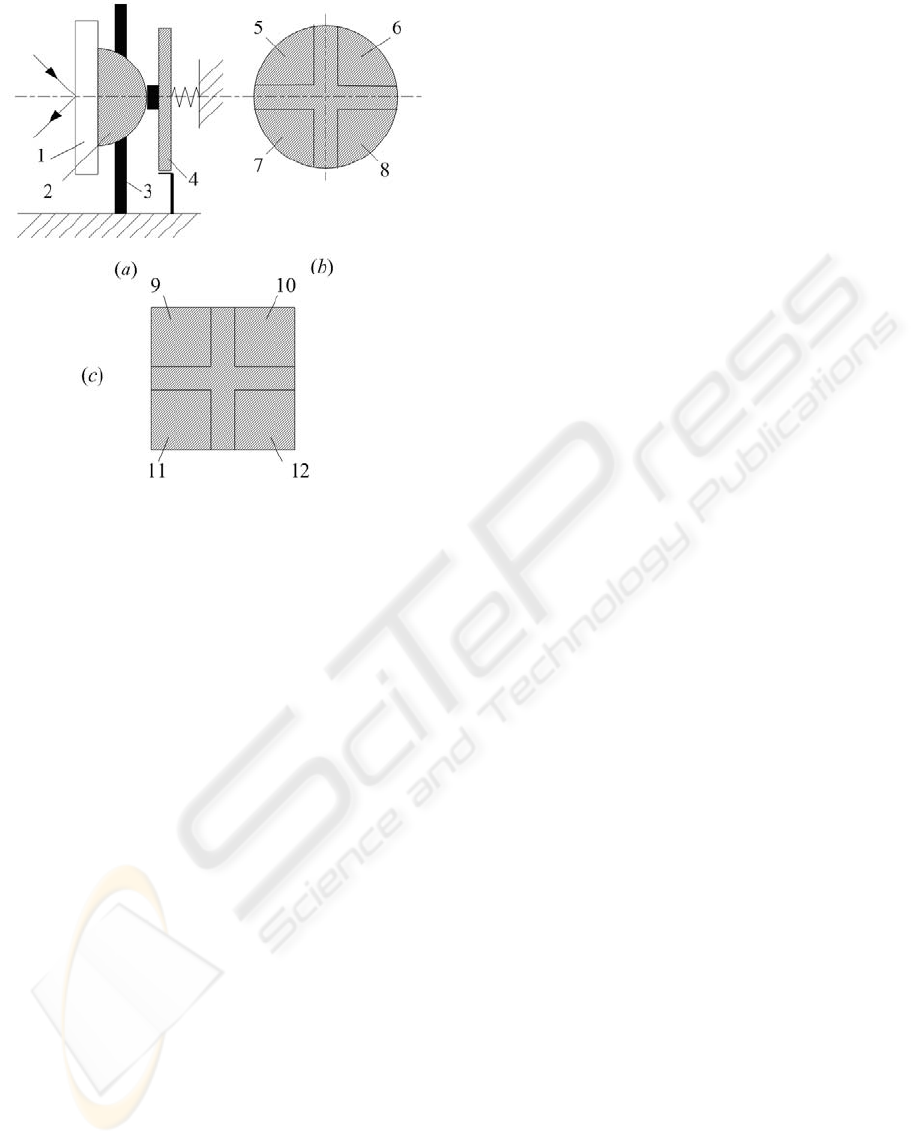
Figure 10: Two-degree-of-freedom optical beam
reflector/scanner. 1 – mirror; 2 – segment of spherical
piezotransducer; 3 – fixing element (scheme is not
specified); 4 – plate type piezotransducer; 5…12 –
sectioned electrodes.
4 CONCLUSIONS
New type of multi-degree-of-freedom piezoelectric
actuators, based on active kinematic pairs, is
presented in this paper. Schematics of piezoelectric
motors, using two active elements in the contact
zone and comprising the number of degrees-of-
freedom up to 5 are presented. Several applications
for laser beam deflection and positioning devices in
the plane are described. The concept of active
bearing is introduced.
The contact zones of these actuators are formed
by oscillating pairs of piezoelectric transducers.
Control of the phase difference between the
transducers enable transformation of oblique impacts
into continuous motion. Such types of actuators are
characterised by high resolution, low time constant,
and are applicable in different areas of precision
mechatronics.
ACKNOWLEDGEMENTS
Research has been financed by Lithuanian State
Science and Studies Foundation (High-Tech
Development program’s research project
PjezoAdapt).
REFERENCES
Ragulskis, K., et al., 1988, Vibromotors for Precision
Microrobots, Hemisphere Publishing Corp., New
York, 310 p.
Bansevicius, R. et al., 2002a, The Mechatronics
Handbook, CRC Press, Boca Raton.
Bansevicius, R., 2002b, Latest trends in the development
of piezoelectric multi-degree-of-freedom actuators/
sensors. Responsive systems for active vibration
control, NATO Science Series, Vol. 85, Kluwer
Academic Publishers, Dordrecht, p.207-238.
Bansevicius, R., et al., B., 2000a, Design and control of
precise robots with active and passive kinematic pairs,
Mechatronics 2000: Proceedings of the 7-th
Mechatronics Forum, Atlanta, Georgia, U.S.A.,
Pergamon, p.10-16.
Ko, H-P., et al., 2006, A novelty in ultrasonic linear motor
using the radial mode of a bimorph, Sensors and
Actuators A 125, p.477–481.
Chu, C-L. and Fan, S-H., 2006, A novel long-travel
piezoelectric-driven linear nanopositioning stage,
Precision Engineering 30, p.85–95.
Bansevicius, R., et al., 2000b, Active error compensation
for precise machines, IMEKO 2000: XVI IMEKO
World Congress Proceedings, Vienna, Vol. 8, p.21-26.
Bansevicius, R. and Ahmed, S., 2000a, Piezoelectric
Active Supports, U.K. Patent 2313982, Patented by
Smart Technology Ltd., U.K..
Bansevicius, R. and Ahmed, S., 2000b, Piezoelectric
Actuators, U.K. Patent 2332090, Patented by Smart
Technology Ltd., U.K..
Bansevicius, R. and Ahmed, S., 2001, Bearings and
Support, USA Patent 62625114B1, Patented by Smart
Technology Ltd., U.K..
Zienkiewicz, O.C. and Taylor, R.L. 1991, Finite Element
Method – Solid and Fluid Mechanics: Dynamics and
Nonlinearity, Vol. 2, McGraw-Hill: New York.
ICINCO 2009 - 6th International Conference on Informatics in Control, Automation and Robotics
164