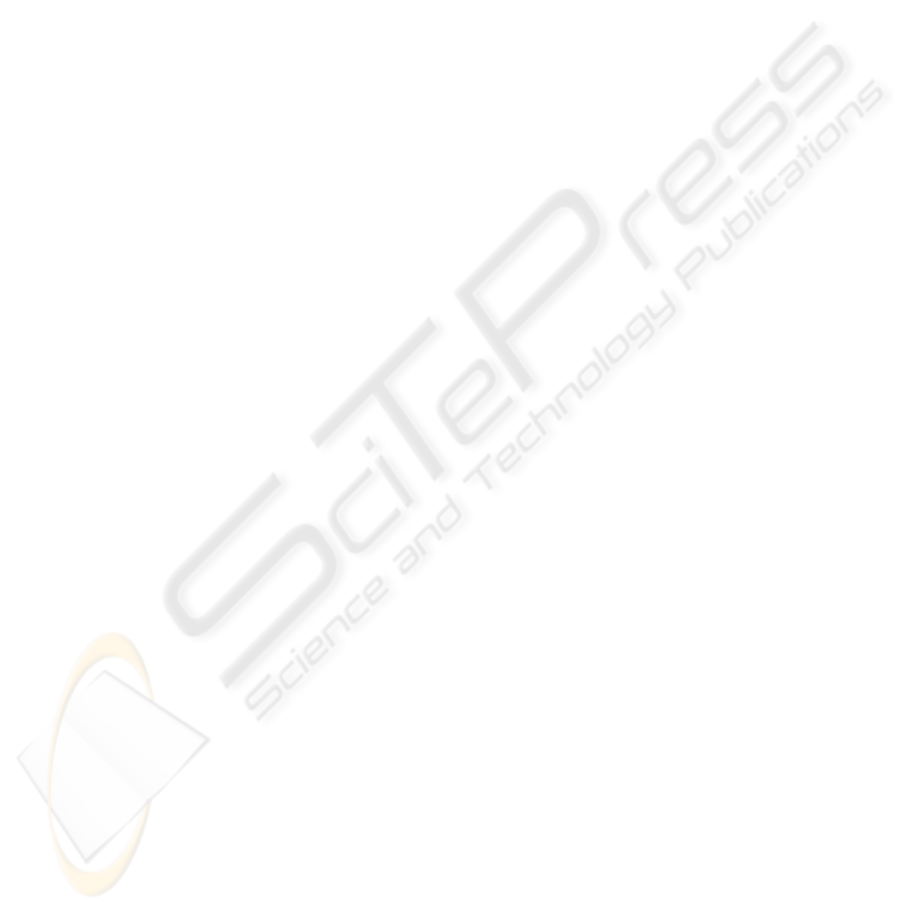
7 CONCLUSIONS
In this paper, an original prototype of VGSTV has
been presented. The dynamic model have been intro-
duced. From this model, a stability criterion based on
the ZMP technique has been computed. This model
have been validated on the real robot in the context of
a staircase clearance.
Future works will focus on the autonomy of the
robot. In a short term work, a real time stability as-
sistance will be provided to the operator based on the
model (CoG or ZMP) presented in this paper. The
presented results are also a preliminary survey for
a long term work that will be oriented on the au-
tonomous obstacle clearance. Actual work (based on
the model and results presented here) is focused on
the automatic control of the robot.
REFERENCES
Carlson, J. and Murphy, R. R. (2003). Reliability analysis of
mobile robots. International Conferenee on Robotics
and Automation.
Carlson, J. and Murphy, R. R. (2005). How ugvs physi-
cally fail in the field. IEEE Transactions on robotics,
21(3):423–437.
Casper, J. and Murphy, R. R. (2003). Human-robot interac-
tions during the robot-assisted urban search and res-
cue response at the world trade center. IEEE Trans-
actions on systems, man, and cybernetics, 33(3):367–
384.
Clement, G. and Villedieu, E. (1987). Variable geometry
track vehicle. Us patent.
Craig, J. J. (1989). Introduction to Robotics Mechanics and
control. Silma, 2 edition.
Frost, T., Norman, C., Pratt, S., and Yamauchi, B. (2002).
Derived performance metrics and measurements com-
pared to field experience for the packbot. Proceedings
of the 2002 PerMIS Workshop.
Guarnieri, M., Debenest, P., Inoh, T., Fukushima, E., and
Hirose, S. (2004). Development of helios vii : an
arm-equipped tracked vehicle for search and rescue
operations. IEEE/RSJ Int. Conference on Intelligent
Robots.
Iwamoto, T. and Yamamoto, H. (1983). Variable configura-
tion track laying vehicle (us patent).
Kajita, S., Kanehiro, F., Kaneko, K., Fujiwara, K., Harada,
K., Yokoi, K., and Hirukawa, H. (2003). Biped walk-
ing pattern generation by using preview control of
zero moment point. Proceedings of the 2002 IEEE
Internationnal Conference on Robotics ans Automa-
tion.
Khalil, W. and Dombre, E. (2004). Modeling, Identification
and Control of Robots. Kogan Page Science, 2 edition.
Kim, J., Chung, W. K., Youm, Y., and Lee, B. H. (2002).
Real time zmp compensation method using null mo-
tion for mobile manipulators. Proceedings of the 2002
IEEE Internationnal Conference on Robotics ans Au-
tomation.
Kinugasa, T., Otani, Y., Haji, T., Yoshida, K., Osuka, K.,
and Amano, H. (2008). A proposal of flexible mono-
tread mobile track. Internationnal Conference on In-
telligent Robots and Systems.
Kyun, L. S., Il, P. D., Keun, K. Y., Byung-Soo, K.,
and Sang-Won, J. (2005). Variable geometry single-
tracked mechanism for a rescue robot. IEEE Inter-
national Workshop on Safety, Security and Rescue
Robotics, pages 111–115.
Misawa, R. (1997). Stair-climbing crawler transporter. Us
patent.
Paillat, J. L., Lucidarme, P., and Hardouin, L. (2008). Vari-
able geometry tracked vehicle, description, model and
behavior. Conference Mecatronics.
Vincent, I. and Trentini, M. (2007). Shape-shifting tracked
robotic vehicle for complex terrain navigation: Char-
acteristics and architecture. Technical memorandum,
Defence R and D Canada.
Vukobratovic, M. and Borovac, B. (2004). Zero-momment
point - thirty five years of its life. Internationnal jour-
nal of humanoid Robotics, 1(1):157–173.
ICINCO 2009 - 6th International Conference on Informatics in Control, Automation and Robotics
28