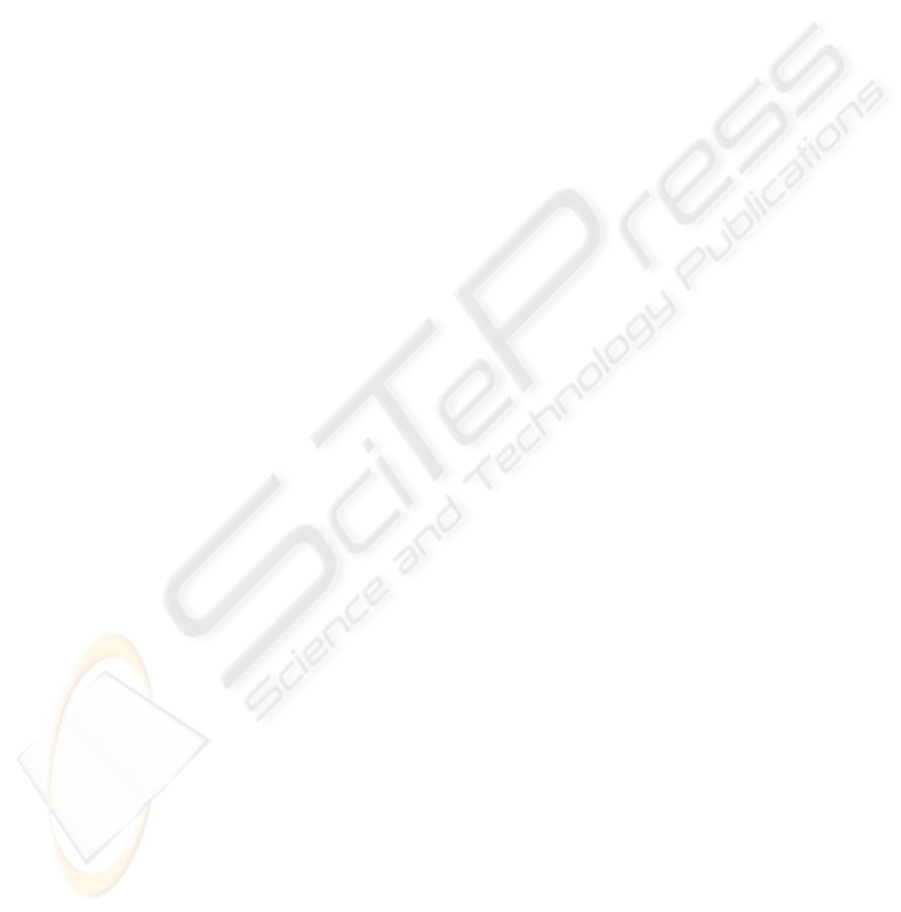
THEORETICAL CALCULATION OF THERMAL CONTACT
RESISTANCE OF BALL BEARING UNDER DIFFERENT LOADS
Chao Jin, Bo Wu
State Key Laboratory for Digital Manufacturing Equipment and Technology
Huazhong University of Science and Technology, Wuhan, Hubei 430074, China
Youmin Hu
School of Mechanical Science and Engineering, Huazhong University of Science and Technology
Keywords: Hertzian theory, JHM method, Load distribution, Thermal contact resistance.
Abstract: The thermal contact resistance between the balls and the inner and outer rings of an angular contact ball
bearing is investigated. It is assumed that the bearing sustains thrust, radial, or combined loads under a
steady-state temperature condition. The shapes and sizes of the contact areas are calculated using the
Hertzian theory. The distribution of internal loading in the bearing is determined by the JHM method. The
comparison between the experimental data and the calculated values confirms the validity of the prediction
method for the thermal contact resistances between the elements of a bearing.
1 INTRODUCTION
In a high-speed feeding system, bearings are
considered to be the main heat sources, and the
thermal properties of the bearings need to be
carefully studied. For a bearing, the thermal
resistances for conduction through the bearing
elements themselves and for radiation can be
calculated using the dimensions, the thermal
conductivities, the thermal-optical properties, and
the temperatures of the elements. However, it ca be
said that the thermal contact resistances between the
balls and the rings, which are most closely related to
the temperature differences across the bearings, are
difficult to predict because few useful calculation
method have been proposed yet.
Since the thermal resistance results from the fact
that most of the heat is constrained to flow through
small contact areas, a reasonable step in determining
the contact resistance between the balls and the inner
and outer rings of the bearing would be to use a
similar approach to that adopted to solve the thermal
constriction problem for ideal smooth surfaces. The
thermal constriction resistances for circular, circular
annular, rectangular, and other geometrical-shaped
contact areas are normally solved analytically or
numerically as Dirichlet problems. The prediction of
the thermal contact resistance necessitates the
determination of the contact area. This is possible
with the Hertzian theory when the contact surfaces
are approximated as being smooth. In addition to the
study by Clausing and Chao, the thermal contact
resistance problem has been discussed in many
papers. Most papers determine the contact areas
using the Hertzian theory. However, a survey of the
literature shows that only the studies by Yovanovich
have dealt with the problem of the contact resistance
between bearing elements. He studied the contact
resistance under axial loads and concluded that the
contact resistance depends on the size and shape of
contact area as determined by the Hertzian theory
and the thermal conductivity of the material. He did
not, however, give thermal designers a tractable
expression that considered the change in contact
angle induced by elastic deformation at the contact
points. Also, he did not consider other types of
loadings such as radial and combined axial/radial
loads.
This article develops an approach that accurately
predicts the thermal contact resistance between the
balls and the inner and outer rings of an angular
contact ball bearing. The contact forces required to
calculate the contact area are explicitly formulated
for axial, radial, and combined loadings. The
prediction method for the thermal contact resistance
is verified by comparing the calculated values with
181
Jin C., Wu B. and Hu Y. (2009).
THEORETICAL CALCULATION OF THERMAL CONTACT RESISTANCE OF BALL BEARING UNDER DIFFERENT LOADS.
In Proceedings of the 6th International Conference on Informatics in Control, Automation and Robotics - Intelligent Control Systems and Optimization,
pages 181-188
DOI: 10.5220/0002192401810188
Copyright
c
SciTePress