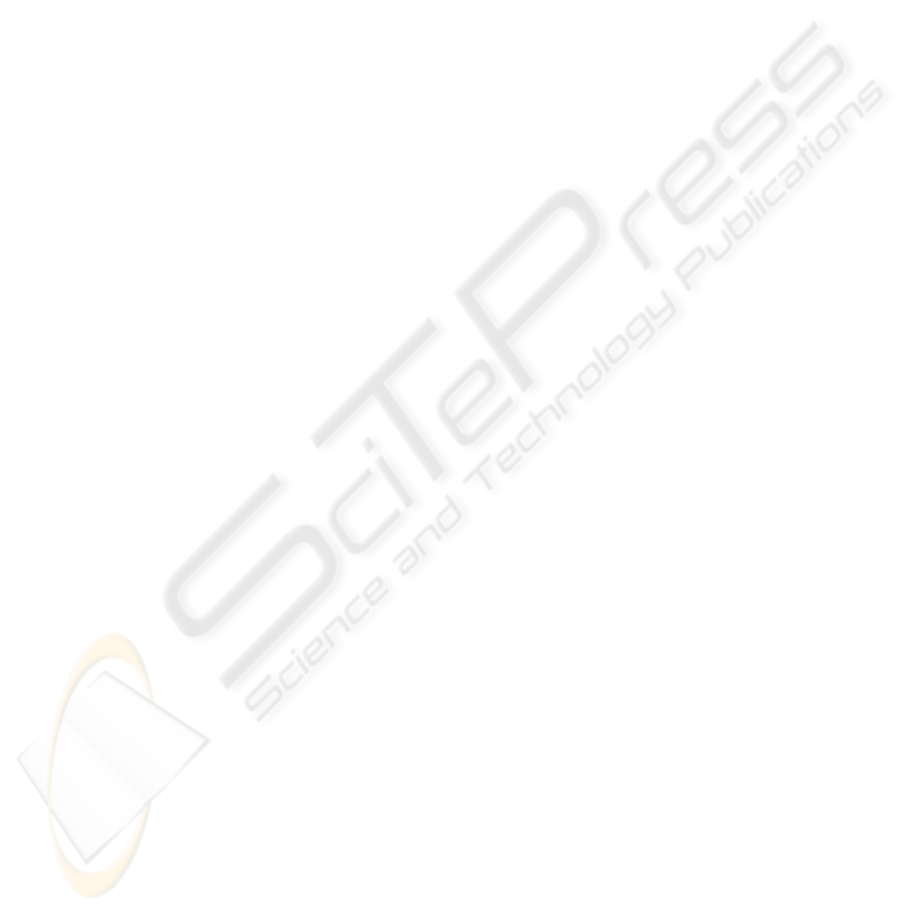
ssed with the client. Their feedback serves as a basis
to validate the above findings and to check the
possibilities for the measures to be suggested. The
potentials and problems as well as excerpts from
KMDL models were presented during the result
workshop. Subsequently, the client discussed the
measures described above and jointly prioritized
them by considering their estimated benefit and
costs.
3 CONCLUSIONS
AND OUTLOOK
Objective 1: How does KMDL help to identify and
to highlight knowledge activities or processes?
KMDL enables process analysts to gain an in-
depth understanding of a process and the underlying,
often previously unidentified knowledge activities.
By means of interviews as well as feedbacks and
approvals on various levels, the actual situation can
be reflected and intensely examined.
The interviewed employees can bring up the
problems concerning the knowledge transfer,
generation, sharing and the like according to their
field of expertise. The client is able to look into their
business processes beyond the typical flow oriented
point of view. The process and the activities are
reviewed by multiple actors from different
perspectives, which encourages unbiased views. As
a result knowledge activities are documented and
made visible.
Objective 2: How is KMDL an appropriate
method to analyze and improve knowledge intensive
business processes?
Prior to the application of the method the client’s
understanding of the problem was only vague.
During the project, this understanding was
broadened and concrete causes of the problem were
identified by obtaining transparently reflected
processes and activities within the processes. They
also benefit from the analysis and the recommended
measures.
Apart from that, clients of KMDL projects do not
need a comprehensive method knowledge Any
inquiries about the method or the analysis could
easily be transferred during the two workshops.
By focusing on concrete instances of the process
a better caption of the actual activities was obtained.
However, two instances are hardly enough evidence
for empirical analysis. It remains an issue of
interpretation to evaluate the models, which is why
the analysts are required to have sufficient
experiences in the field.
Objective 3: How can KMDL be improved?
Which benefits do the expanded functions in version
2.1 offer?
As described, in this case the procedural model
has been simplified, due to very limited resources.
However, the separation of the process and activities
views has proven to be a significant improvement.
The process model acts as source for an overview
and reference for a detailed analysis of knowledge
activities. Transfers and applications can also be
traced within various activities.
In capturing the general characteristic of the
communication, the evaluation of small numbers of
process instances produces only exemplary results.
Formal and quantitative methods are more
appropriate to capture communication. These
communication acts can indicate additional
knowledge exchange.
Only recently KMDL was extended with an
additional view for communication (Müller, 2008),
which captures actors, communication acts as well
as communication instruments. The view
differentiates types of communication by anytime /
anyplace matrix. New angles such as a planned
(e.g. scheduled during a meeting) and random (e.g.
met in the hall) communication act are used to
validate the activity view and to incorporate random
acts of (informal) knowledge exchange into the
analysis.
REFERENCES
Abecker, A., Hinkelmann, K., Maus, H. & Müller, H.-J.,
2002. Integrationspotenziale für Geschäftsprozesse
und Wissensmanagement. In: Geschäftsprozessorientiertes
Wissensmanagement, pp. 1-22. Springer. Berlin.
Allweyer, T., 1998. Knowledge Process Redesign -
Modellierung und Gestaltung der Wissensverarbeitung
im Unternehmen. IDS Prof. Scheer GmbH.
Fröming, J., Gronau, N. & Schmid, S., 2006. International
Journal of Knowlegde Management (IJKM),vol2, pp.
32-51.
Gronau, N. & Weber, E., 2004. Defining an Infrastructure
for knowledge intensive Business Processes. In:
Proceedings of IKNOW 2004, pp. 424-431. Graz,
Austria,
Heisig, P., 2003. Business Process Oriented Knowledge
Management. In: Knowledge Management - Concepts
and Best Practices, pp. 15-44. Springer. Berlin.
Kim, S.-K., Lim, S.-H. & Mitchell, R. B., 2006.
International Journal of Knowlegde Management
(IJKM), vol 2, pp. 17-31.
Müller, C., 2008. Graphentheoretische Analyse der
Evolution von Wiki-basierten Netzwerken für
selbstorganisiertes Wissensmanagement, Gito. Berlin.
KMDL FOR INNOVATION AND PRODUCTION RAMP-UP PROCESS EVALUATION - A Case Study
283