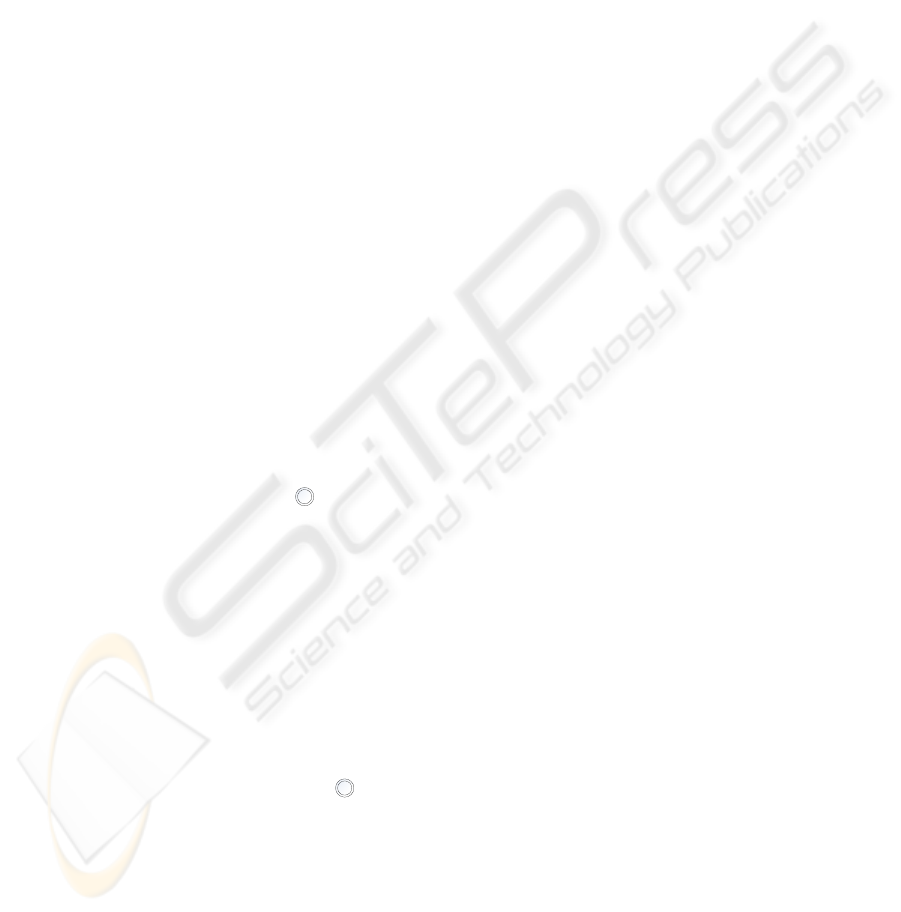
organization is accomplished to produce the
economic output that generates the profitable return
on the capital employed (Watson, 1994).
Business process modelling generates a model to
describe a certain business process in an enterprise
using different techniques. The model is a
representation of a business process and reflects its
reality by capturing all the necessary information on
process behaviour. The modelled process is then
analysed and improved instead of the real business
process. In this paper, we present process modelling
using a technique called the Activity Table.
The activity table is organized as follows: the
first column represents the business process and the
second column shows the work processes of the
business process discussed. The activities of the
listed work processes are shown in the rows of the
third column. The resources are introduced in the
remaining columns of the second row grouped by
the departments to which they belong.
To make the activity table reflect the real world,
we link the activities horizontally and vertically.
Horizontal linkage means that each activity must be
connected with those entities in the columns which
are involved in it. Vertical linkage is used to define
the order in which the activities are performed. Each
activity is connected with one or more predecessor
activities, except the first one, and is also linked to
one or more successor activities, except the last
activity.
To model a process, the activity table uses
symbols such as:
□, ◇, →, ↓, ○, and .
Symbol □ in square(i,j) means that resource(j)
performs activity(i), where j ranges from 1 to the
number of resources and i ranges from 1 to the
number of activities. Symbol ◇ in square(i,j) means
that activity(i) is a decision activity. Symbols → and
↓ are used to connect the activity horizontally and
vertically. An arrow → drawn from square(i,j) to
square(i,k) shows the horizontal linkage of
activity(i). An arrow ↓drawn from square(i,j) to
squre(k,j) indicates that activity(i) is linked
vertically to its successor activity(k). Symbol
○
indicates a start of the process and symbol
means
an end of the process.
Surgery: The business process “Surgery” was
modelled by developing Table 1, which represents
the activity table.
3 SIMULATION
A simulation is the imitation of the operation of a
real-world process or system over time. Simulation
involves the generation of an artificial history of a
system, and the observation of that artificial history
to draw inferences concerning the operating
characteristics of the real system (Banks et al.,
2001).
The functioning of the process discussed is
observed in order for it to be understood completely.
Understanding the behaviour of a process over time
enables as to model it and create a simulation
scenario based on a set of data and assumptions
about the operation of its activities.
When the process model is created, we have to
check and validate it to find out if it reflects the real
process. Then the model is analysed carefully using
different "what-if" questions to test several options
and possibilities concerning the functioning of the
process. Such versions of process behaviour are then
simulated to find out their impact on process
performance and to compare them in order to choose
the best solution.
Business processes are modelled with the aim of
analysing their current states within the organization,
as well as improving them through the execution of
potential ‘‘what-if” simulation scenarios (Aguilar-
Saven et al., 2002). The use of scenario-based what-
if analyses enables the design team to test various
alternatives and choose the best one (Laguna et al.,
2005).
Process modelling, creating scenarios of its
behaviour, and running its simulation enable the
analyst to obtain knowledge and new ideas that
could be very important in process improvement.
This is usually achieved by changing the simulation
input data and analysing the simulation outputs. This
technique leads us to find out which data or
parameters are essential for process improvement.
Discrete-event system simulation is the
modelling of systems in which the state variable
changes only at a discrete set of points in time.
Discrete-event models are appropriate for those
systems for which changes in system state occur
only at discrete points in time (Banks et al., 2001)
and business processes are such systems.
Below we list some of the major concepts of a
discrete-event model of a system, as they are defined
in "Discrete-Event System Simulation" by Banks,
Carson, Nelson and Nicol:
- System: A collection of entities (e.g., people and
machines) that interact together over time to
accomplish one or more goals;
- model: An abstract representation of a system
that describe a system, usually containing
structural, logical, or mathematical relationships
HEALTHCARE PROCESS IMPROVEMENT USING SIMULATION
423