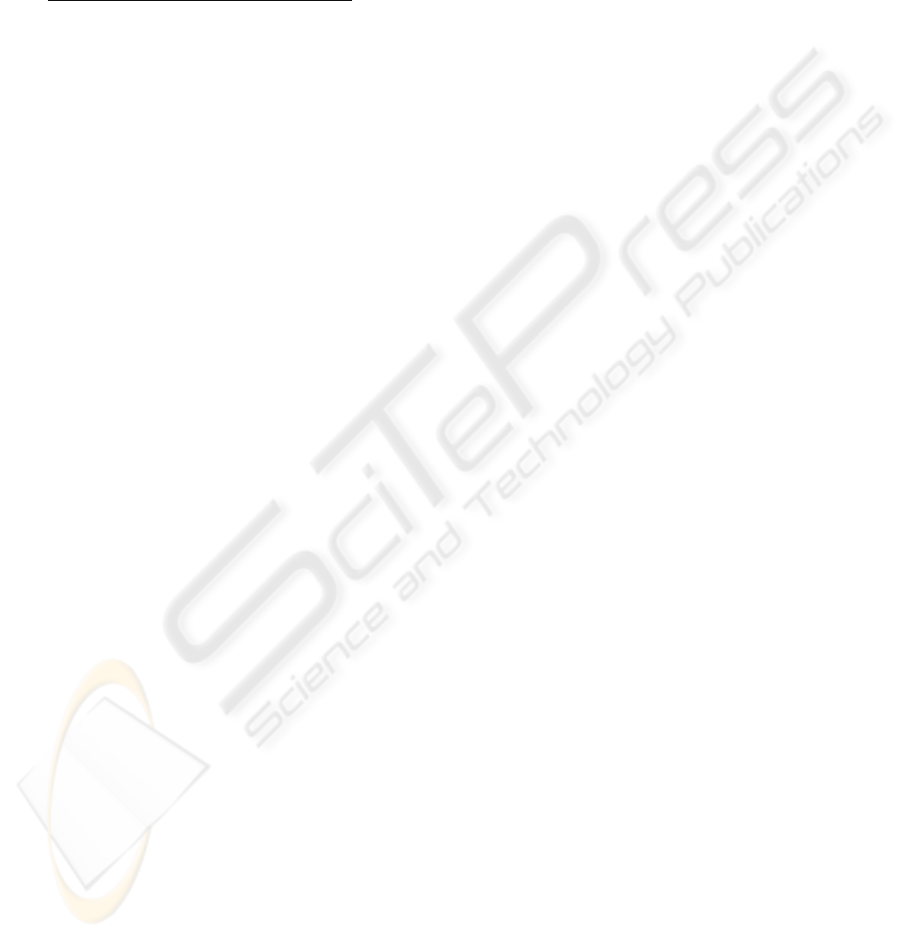
the elastic moduli will generate substantial shear
strain at the gold-SU8 interface, which may lead to
de-lamination of the film from the substrate.
If the film thickness is significant, (2) and (3)
can still be used for predicting deflections by
replacing the substrate modulus (E
s
) with the
effective substrate modulus (E
eff
) given as (Yi, 2002)
24 24 2 2
2(223)
fs fs
eff
fs
E a E b E E ab a b ab
E
Ea Eb
++ ++
=
+
(4)
where a = t
f
/t and b = t
s
/t, and t is total thickness of
the cantilever. To elucidate (4), consider the
geometric and material properties of the gold coated
cantilever analysed in this study. Though E
s
is 130
GPa, the E
eff
is about 127 GPa.
4 CONCLUSIONS
Microcantilever biosensors provide a universal,
rapid, and highly sensitive mean to many
applications. The measurement accuracy of the
sensor depends on its ability to isolate and eliminate
the noise from the signal. Since bimetallic effects are
a major source of noise in the signal, we investigated
the effect of temperature on the deflection
characteristics of the cantilever. The results
indicated that thermal deflections can be determined
accurately using analytical and simulation models.
By studying the combined effect of thermal- and
adsorbate-induced surface stresses on the cantilever
deflection, we found that the two stresses act linearly
and additively. We found that even for small
temperature variation, the thermal deflections can
easily exceed the adsorbate-induced deflections, and
hence produce noise in the deflection signal.
However, by deducting the thermal deflection from
the total deflection amount, the exact adsorbate-
induced deflection or stress can be determined.
Further, the large mismatch in the thermoelastic
properties makes SU8 microcantilever biosensors
more susceptible to bimetallic effects.
ACKNOWLEDGEMENTS
This study was supported by Inha University.
REFERENCES
Barnes J. R., Stephenson R. J., Woodburn C. N., 1994. A
femtojoule calorimeter using micromechanical
sensors, Rev. Sci. Instrum., vol. 65, pp. 3793-3798.
Hennemeyer M., Burghardt S., Stark R.W., 2008.
Cantilever micro-rheometer for the characterization of
sugar solutions, Sensors, vol. 8, pp. 10-22.
Qazi M., Koley G., 2008. NO
2
detection using micro-
cantilever based potentiometry, Sensors, vol. 8, pp.
7144-7156.
McKendry R., Zhang J., Arntz Y., Strunz T., Hegner M.,
Lang H. P., Baller M. K., Certa U., Meyer E.,
Guntherodt H. J., Gerber C., 2002. Multiple label-free
biodetection and quantitative DNA-binding assays on
a nanomechanical cantilever array, Proc. Natl. Acad.
Sci., vol. 99, pp. 9783-9788.
Mertens J., Rogero C., Calleja M., Ramos D., Martin-
Gago J. A., Briones C., Tamayo J., 2008. Label-free
detection of DNA hybridization based on hydration
induced tension in nucleic acid films, Nature
Nanotechnol., vol. 3, pp. 301-307.
Fritz J., Baller M. K., Lang H. P., Rothuizen H., Vettiger
P., Meyer E., Guntherodt H. J., Gerber C., Gimzewski
J. K., 2000. Translating biomolecular recognition into
nanomechanics, Science, vol. 288, pp. 316-318.
Stoney G. G., 1909. The tension of metallic films
deposited by electrolysis, Proc. Roy. Soc. Lond. A, vol.
82, pp. 172-175.
Hsueh C. H., 2002. Modeling of elastic deformation of
multilayers due to residual stresses and external
bending, J. Appl. Phys., vol. 91(12), pp. 9652-9656.
Finot E., Passian A., Thundat T., 2008. Measurement of
mechanical properties of cantilever shaped materials,
Sensors, vol. 8, pp. 3497-3541.
Ansari M. Z., Cho C., Kim J., Bang B., 2009. Comparison
between deflection and vibration characteristics of
rectangular and trapezoidal profile microcantilevers,
Sensors, vol. 9, pp. 2706-2718.
Ramos D., Mertens J., Calleja M., Tamayo J., 2007. Study
of the origin of bending induced by bimetallic effect
on microcantilever, Sensors, vol. 7, pp. 1757-1765.
Yi J. W., Shih W. Y., Shih W. H., 2002. Effect of length,
width, and mode on the mass detection sensitivity of
piezoelectric unimorph cantilevers, J. Appl. Phys., vol.
91, pp. 1680-1686.
A STUDY ON BIMETALLIC EFFECTS IN MICROCANTILEVER BIOSENSORS
31