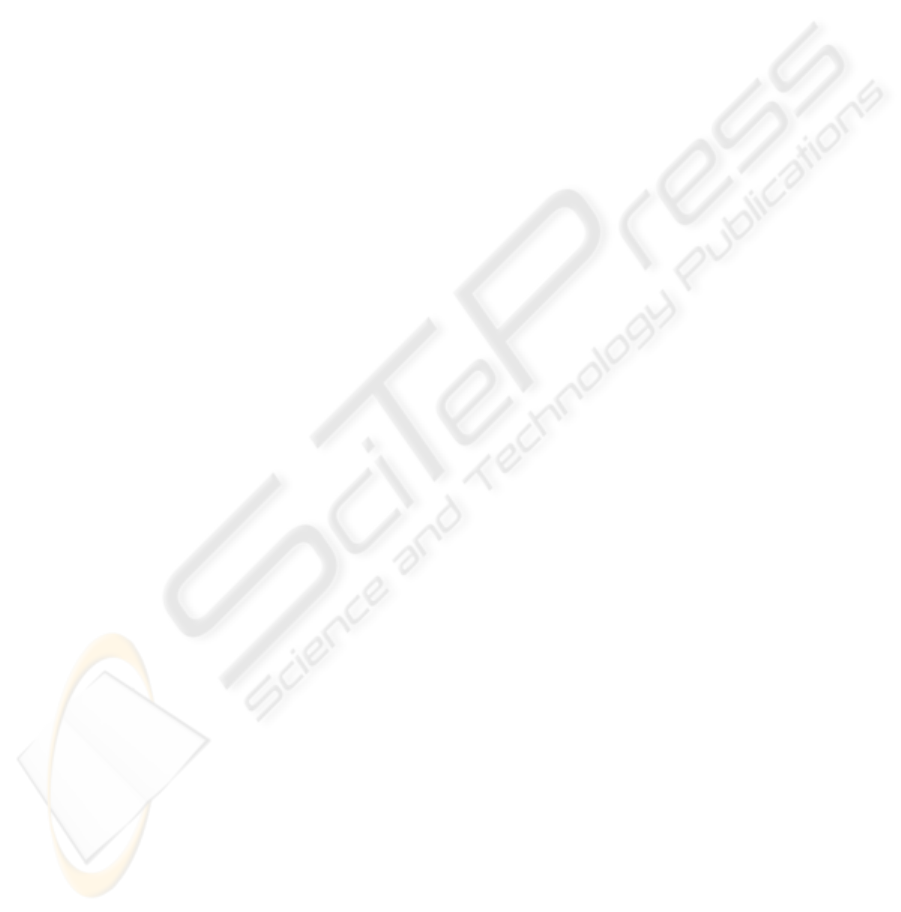
to walk when lifting, these moments should be
supported. However, it is also desirable that the
wearer be able to abduct the leg. Passive joints that
only allow abduction of the legs would solve this.
5 DISCUSSION
Even with the proposed solutions the variety of
motions that can be performed with HAL is still less
than without, and limitations remain. Gravity
compensation is limited to generic postures, some
useful DoFs, such as inner rotation of the arm, are
not augmented, and the full RoMs are not achieved.
Even so, in most working situations there are
several postures available to the worker by which
the task’s goals can be achieved, and the wearer may
adapt his motion to utilize postures for which HAL
provides the most support. Since this is available in
postures humans use extensively it is very likely that,
although it should be confirmed by further research,
at any time at least one good posture can be attained.
Therefore, HAL would be valuable in a human
environment and the proposed practical design
approach thus achieved its goals. In addition, it is
expected that further practical, human characteristics
may be exploited to simplify design.
We believe that a similar practical focus may be
applied to other fields where humans and machines
meet cooperatively, such as rehabilitation, to yield
new improvements. A practical approach could
unveil solutions that enable patients to perform
particularly those motions needed for daily activities.
ACKNOWLEDGEMENTS
This work was supported in part by the Global COE
Program on “Cybernics: fusion of human, machine,
and information systems”.
REFERENCES
Aida, T., Nozaki, H. & Kobayashi, H., 2009.
“Development of Muscle Suit and Application to
Factory Laborers” Proc. IEEE Int. Conf. on
Mechatronics and Automation, China, pp.1-5.
BBC News, 2008. "US army develops robotic suits", April
16 2008, retrieved August 31, 2009, <news.bbc.co.uk
/2/hi/7351314.stm>.
Colombo, G., Joerg, M., Schreier, R. & Dietz, V., 2000.
“Treadmill training of paraplegic patients using a
robotic orthosis,” J. Rehabil. Res. Develop., vol. 37,
no. 6, pp. 693–700.
Dollar, A.M., & Herr, H., 2008. “Lower Extremity
Exoskeletons and Active Orthoses: Challenges and
State of the Art,” Transactions on Robotics, vol. 24(1).
Folgheraiter, M., Bongardt, B., Schmidt, S., De Gea, J.,
Albiez, J. & Kirchner, F., 2009. “Design of an Arm
Exoskeleton Using a Hybrid Model- and Motion-
Capture-Based Technique,” Interfacing the Human
and the Robot Workshop, ICRA.
Hidler, J.M. & Wall, A.E., 2005. “Alterations in muscle
activation patterns during robotic-assisted walking,”
Clin. Biomech., vol. 20, pp. 184–193.
Liszka, M.S., 2006. “Mechanical Design of a Robotic Arm
Exoskeleton for Shoulder Rehabilitation,” M.S. thesis,
Univ. of Maryland.
Mulas, M., Folgheraiter, M. & Gini, G., 2005. “An EMG-
controlled Exoskeleton for Hand Rehabilitation” Int.
Conf. on Rehabilitation Robotics, Chicago, IL, USA.
Nevala-Puranen, N., 1995. “Reduction of farmers' postural
load during occupationally oriented medical reha-
bilitation,” Applied Ergonomics, 26(6), pp. 411-415.
Perry, J.C. & Rosen, J., 2006. “Design of a 7 Degree-of-
Freedom Upper-Limb Powered Exoskeleton,” IEEE
Conf. on Biomedical Robotics and Biomechatronics.
Rosen, J., Perry, J.C., Manning, N., Burns, S. &
Hannaford, B., 2005. “The human arm kinematics and
dynamics during daily activities – toward a 7 DOF
upper limb powered exoskeleton,” Proc. 12th Intl.
Conf. on Advanced Robotics, ICAR '05, pp. 532-539.
Sasaki, D., Noritsugu, T., Takaiwa, M., & Yamamoto, H.,
2004. “Wearable power assist device for hand
grasping using pneumatic artificial rubber muscle,”
13th IEEE Int. Workshop on Robot and Human
Interactive Communication, ROMAN, pp. 655-660.
Schibye, B., Faber Hansen, A., Hye-Knudsen, C.T.,
Essendrop, M., Bocher, M. & Skotte, J., 2003,
“Biomechanical analysis of the effect of changing
patient-handling technique,” App Ergonom, 34, pp.
115-123.
Schiele, A., & Van der Helm, F.C., 2006. “Kinematic
design to improve ergonomics in human machine
interaction”, IEEE Trans Neural Syst Rehabil Eng,
14(4), 456-69.
Suzuki, K., Kawamura, Y., Hayashi, T., Sakurai, T.,
Hasegawa, Y. & Sankai, Y., 2005, "Intention-Based
Walking Support for Paraplegia Patient," Int. Conf. on
Systems, Man and Cybernetics, Hawaii, pp.2707-2713.
Toyama, S., 2009. “Wearable Agri Robot,” Toyama Lab,
retrieved August 31, 2009, <www.tuat.ac.jp/
~toyama/research_assistancesuitE.html>.
Tsagarakis, N. & Caldwell, D., 2003. “Development and
control of a soft-actuated exoskeleton for use in
physiotherapy and training,” Autonomous Robots, vol.
15, pp. 21–33.
Vieira, E.R. & Kumar, S., 2004 “Working postures: a
literature review,” J Occup Rehabil, 14(2), pp. 143-59.
Yamamoto, K., Hyodo, K., Ishi, M. & Matsuo, T., 2002.
“Development of power assisting suit for assisting
nurse labor,” JSME Int. J., Series C: Mechanical
Systems, Machine Elements and Manufacturing, v 45,
n 3, pp. 703-711.
BIODEVICES 2010 - International Conference on Biomedical Electronics and Devices
138