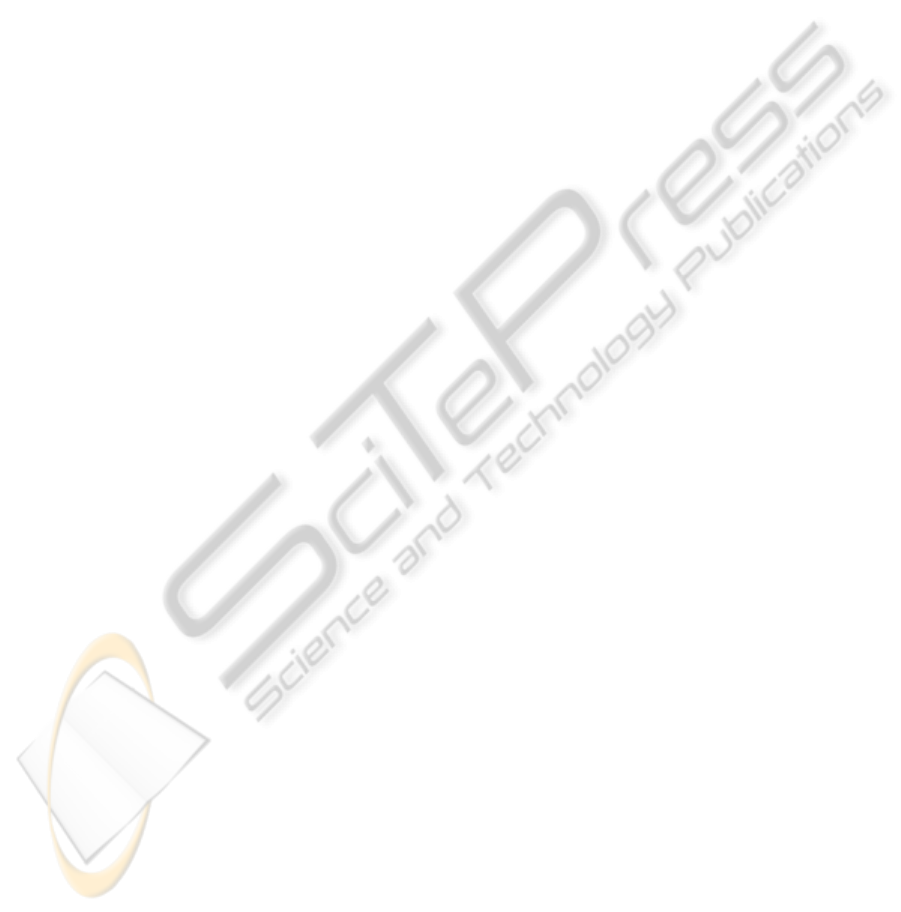
technology for ultrahigh performance and
customization. NI CompactRIO incorporates a real-
time processor and reconfigurable FPGA for reliable
stand-alone embedded or distributed applications,
and hot-swappable industrial I/O modules with built-
in signal conditioning for direct connection to
sensors and actuators’ (National Instruments, 2009).
The setup of the system applicable for
MANOLA consists of an embedded real-time
processor with 800 MHz, 512 MB DDR2 RAM, and
4 GB storage. The processor is connected to a 4-slot
Virtex-5 LX50 reconfigurable chassis that will be
installed on the MANOLA trolley. Furthermore two
8-slot deterministic chassis will be installed on the
manipulator itself for embedding all sensors and
actuators of MANOLA. Both chassis on the
manipulator will be linked with the main chassis on
the trolley in daisy chain mode via Ethernet cable,
and the main chassis on the trolley is linked via
WLAN with a laptop that serves as the MANOLA
Control Panel. Beyond all these components there
are WLAN cameras installed on each, the trolley and
the manipulator, for process monitoring by the
operator.
5.2 Sensors
Various sensors are part of the MANOLA control
system. They are used for different purposes like
positioning, vacuum and pressure monitoring,
position monitoring of pistons as well as scanning
and evaluating the object which has to be treated.
All sensors provide necessary input to the
manipulator for a proper operation.
First, there are four distance laser sensors used as
a simplified positioning system for MANOLA. The
four sensors are fixed to a traverse that carries the
laser processing head and runs over the main frame
of the manipulator. By moving the distance laser
sensors over the entire frame, many different reading
points can be generated and used to map the
borderlines given by adjacent parts of the building.
Second, a laser scanner is used for scanning and
evaluating the surface area of the object to be
treated. The laser scanner is part of the processing
head which also includes the optics of the laser unit
for the ablation process, and it enables the machine
to detect disruptive objects like offsets on the
surface, nails, screws, pipes, etc. All these different
kinds of objects may interfere with the operation of
the laser. Thus it is very important to detect them in
order to protect the laser processing head.
Third, there are two ultrasonic sensors attached
to the processing head. The ultrasonic sensors are
used for the detection of obstacles that may appear
in front of the processing head during treatment of
the surface area. In any case of interference the
process will be paused immediately in order to
protect the processing head. Then the processing
head will be moved up by an electric drive and the
suspect area will be scanned with the laser scanner if
applicable. Depending on the size of the obstacle the
manipulator will be moved forward or around the
localised object. The integrated decision making
process is based on the input of the various sensors
of the processing head.
Fourth, pressure and vacuum monitoring is an
essential part of the control system. Due to the fact
that the manipulator is operated with vacuum
technology it is security-relevant and prevents
MANOLA from falling off the wall. The vacuum for
the suction plates is produced by sending pressurized
air through vacuum generators that operate
according to the Venturi Principle. Because the
connection of the suction plates to the object
depends on the pressure as well as on the vacuum,
both, pressure and vacuum, need to be monitored.
Fifth, several small size sensors are required for
monitoring the exact positions of the pistons of all
pneumatic cylinders. Every time when a piston is
moved the control system asks for a feedback, if the
piston reached its destination. If this case is true,
further operations can proceed. In a false case,
further operations have to be put on hold due to the
occurrence of an error. Only after assessing and
removing the error by the operator further operation
may proceed.
5.3 Actuators
Besides the sensors MANOLA includes different
actuators. The actuators are used for the operation of
the supporting frame, the traverse and the processing
head. The actuators of MANOLA are a rack drive, a
rotary module, a servo drive as well as a couple of
pneumatic control valves.
The rack drive joins two important tasks. It
moves the traverse and processing head for ablation
processing as well as the supporting frame which
includes the main frame and sub frame for pacing.
By linking the rack drive to the component that has
to be moved only one drive is needed. Thus the
overall weight of the manipulator is kept on a low
level.
In order to turn the manipulator by 45, 90 or any
degrees to change the direction of processing a
rotary module is built-in to the center of the sub
frame. When the manipulator is rotated the suction
ICINCO 2010 - 7th International Conference on Informatics in Control, Automation and Robotics
380