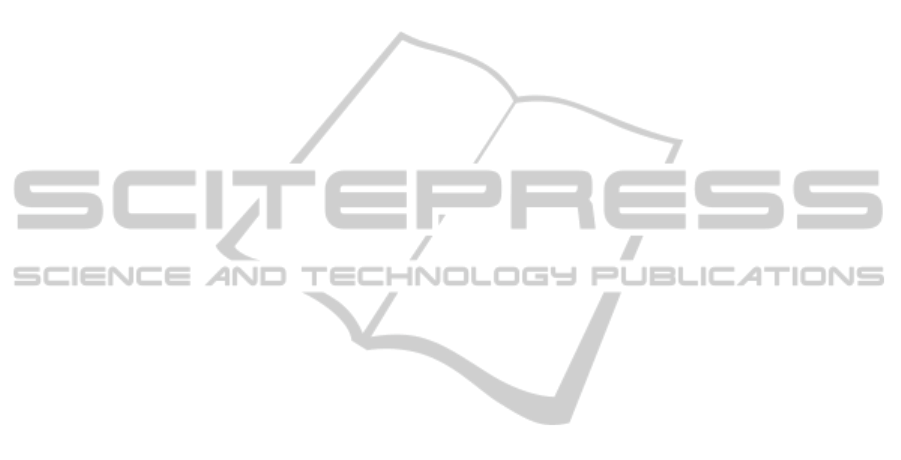
5 WHAT THE NEW SYSTEM
WILL PROVIDE FOR THIS
PROBLEM (CONFIGURATOR)
For the past few months a researcher have been work-
ing on a Configurator, and there was a lot of chal-
lenges in customising it, some of these are related to
the barriers mentioned below, which was caused of
lack of employees knowledge in IT basic tools, and
some others was due to the lack of encouragement
of using the ERP system. Employees no longer have
faith, and don’t believe in the change it would make.
One of the mistakes when doing the Configurator,
was its complexity as it was two pages, with more
than 100 boxes to fill and pick, and that was confus-
ing to employees not knowingmuch about computers,
they refused to use it, as it was complicated and not
user friendly. So with interviews and tests including
employees in the steps, we have eliminated boxes and
made it simpler.
In the Configurator, which is an aid to design and
produce doors, one for an FD30 door, a standard door
for 30 minutes fire rating, was changed about 4 times.
The first one didn’t have all requirements for the door,
and the second was too complicated for employees,
with showing and hiding fields facilities, and then af-
ter sitting with the estimator and discussing things
thoroughly we have found that these are the only re-
quirements for the FD30 door unless there was spe-
cial cases which we will not go through at this stage
of the implementation. After showing this to every-
one in JCK it was discussed that going through this
might take longer time than required and the best idea
if we can set defaults for making this door. Once you
open it, you have all defaults for an FD30 door and
then you just check and do any changes if required,
this will minimise the number of errors and reduce
the time required for making any quote.
Defaults were all set, and the final Configurator
for this door was ready to be used.
In this Configurator there were some requirements
to choose from first, things like Mobility, Secure by
design, Chain of Custody, fire rating and location.
Then the structural opening, which will be allocat-
ing the height and width, and finishing with the glass
and hardware attached to the door. All of these boxes
are attached to the database, where all parts used in
JCK are listed, and connected to purchasing orders to
be able to pull prices and to calculate the door price
when doing the quote.
And here we have faced another problem which
was with validating the knowledge in the Configu-
rator. Employees were saving prices differently into
their excel sheets, using what they have which wasn’t
up to date and prices were very different from.
And here we started gathering receipts, talking to
the employee doing all the purchasing, and trying to
verify prices, and do all the mathematical equations
to get the right door price, and while going through
this process, another problem was found which was
with the different names of the parts used in the door
making. Employees know different ways of naming
the products and were refusing to change to the new
names which were required by the ERP system, and
which are used when purchasing. Some were saying
how hard it is to use this format of names, for that
we had to find a way to write them differently were
everybody can work on the system.
All part names were printed out from the ERP sys-
tem, and there was around 3000 parts available there,
and have decided on one person who would take the
time to do this job, remove un used parts which were
added two years ago, rename the parts with the help
of the researcher and go through the prices, and try-
ing to verify them with the purchasing order. Some
were named with the manufacturer first, others with
the kind of hardware, some was depending on the
height and width of the door. Rules had to be set for
the name and how to deal with them in the Configu-
rator.
Working on this along with the ERP system
Provider Company and the researcher, verification of
prices have been done and the testing process is in
progress.
Hypothesis (1):
Configurator may work, solving all the validation
problems in JCK Joinery and will eliminate all kind
of errors that was happening earlier!
Hypothesis (2):
Configuratormay work faster than the excel sheets
used in the quotes orders.
Hypothesis (3):
When Configurator works properly this will affect
the quality of work positively and make the business
flow easier.
6 PROBLEMS AND BARRIERS
According to previousresearchon JCK, problems that
led to the need of an ERP system, barriers to installing
and using it have been listed as follows:
Problems:
• Loss of information, documents are not filed and a
lot of paper work flows through the organisation,
which makes it easy to mislay or lose.
• Sales enquiries are not tracked, so finding a job
needs to be done manually, which takes time.
KMIS 2010 - International Conference on Knowledge Management and Information Sharing
356