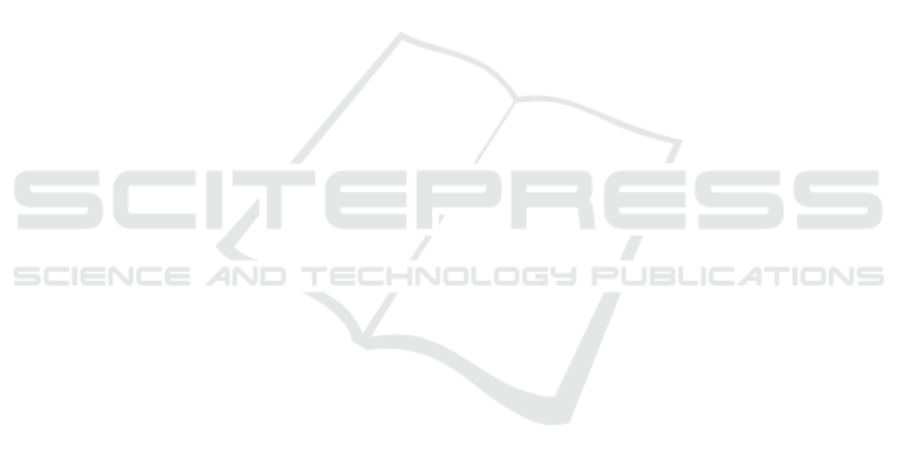
ELECTRICAL RELIABILITY OF Cu/Sn MICRO-BUMP IN
WAFER LEVEL PACKAGING FOR BioMEMS DEVICES
Myeong-Hyeok Jeong, Jae-Won Kim, Byung-Hyun Kwak, Young-Bae Park
School of Materials Science & Engineering, Andong National University, Andong, 760-749, Korea
Byoung-Joon Kim, Young-Chang Joo
Department of Materials Science & Engineering, Seoul National University, Seoul, 151-744, Korea
Keywords: Cu/Sn micro-bump, Electromigration, Wafer Level Packaging, BioMEMS Devices.
Abstract: The electrical reliability of Cu/Sn micro-bump in wafer level packaging for advanced BioMEMS devices
applications were systematically investigated during current stressing condition. After bump bonding,
Cu
3
Sn
and
Cu
6
Sn
5
intermetallic phases were observed, and Cu
3
Sn formed and grew at Cu pillar/Cu
6
Sn
5
interface with increasing annealing and current stressing time. The kinetics of intermetallic compound
growth changed when all Sn in Cu/Sn micro-bump was exhausted. The complete consumption time of Sn
phase in electromigration condition was faster than that in annealing condition. Under current stressing
condition, intermetallic compound growth was significantly enhanced by current stressing where the growth
rate follows a linear relationship with stressing time.
1 INTRODUCTION
Through-Si-via technology using flip-chip solder
bump has recently been investigated in high
performance wafer level packaging for advanced
BioMEMS device packaging (Chiang, Lee, Lee, and
Chen, 2006). This technology assists in the
achievement of high performance and
miniaturization because the chip and the substrate
are directly connected to solder bumps. As the
integration of devices increased, the size of solder
bump in wafer level packaging became smaller with
fine pitch. And increase of current density due to
miniaturization of solder bump size with fine pitch
causes serious reliability issues of wafer level
packaging for advanced BioMEMS applications.
The solder bumps become spherical to minimize the
surface energy during reflow process (Rao, Tay,
Kripseph, Lim, and Yoon, 2004). Bump bridging is
caused by the shape of solder in miniaturized
electronics. It is limited to applications with a fine
pitch below 100 um. Therefore, a new shape for the
bump structure is necessary to address this limitation.
Cu/Sn micro-bumps are known to be one of the most
promising candidates for the fine pitch
interconnection materials in wafer level packaging
because they do not cause bump bridging between
adjacent bumps and uniform current distribution
(Son, Jung, Park, and Paik, 2008). Electrical
reliability issues can also be solved with this
structure because Cu pillars have superior electric
conductivity. At the interface between Cu and solder,
Cu6Sn5 and Cu3Sn are formed by the reaction of Cu
and Sn, and Kirkendall void is grown (Tu, Mayer,
Feldman, 1992). Additionally, the high
concentration of Sn in Pb-free solder induces more
excessive growth of intermetallic compounds
(IMCs) than eutectic SnPb solder (Lee, Zhang,
Wong, Tan, and Hadikusuma, 2006). IMCs growth
and Kirkendall void formation are important
reliability issues of wafer level packaging for
advanced BioMEMS devices because IMCs is brittle
and has higher resistivity than solder or Cu, which
results from the difference in the intrinsic
diffusivities of Cu and Sn, in solder joints severely
deteriorate the mechanical strength of the joints. The
mechanical reliability of solder joints is sensitive to
the solder reaction and the microstructure of the
solder. Therefore, to ensure the bonding reliability of
wafer level packaging for advanced BioMEMS
devices, a deep understanding of the IMC growth
between Cu and solder is necessary. Many
researchers have studied IMCs formation and the
growth between Cu and solder in solder bumps and
thin film structures (Chao, Chae, Zhang, Lu, Im, and
Ho, 2007); but the IMCs growth behaviours in
311
Jeong M., Kim J., Kwak B., Park Y., Kim B. and Joo Y..
ELECTRICAL RELIABILITY OF Cu/Sn MICRO-BUMP IN WAFER LEVEL PACKAGING FOR BioMEMS DEVICES.
DOI: 10.5220/0003122603110314
In Proceedings of the International Conference on Biomedical Electronics and Devices (BIODEVICES-2011), pages 311-314
ISBN: 978-989-8425-37-9
Copyright
c
2011 SCITEPRESS (Science and Technology Publications, Lda.)