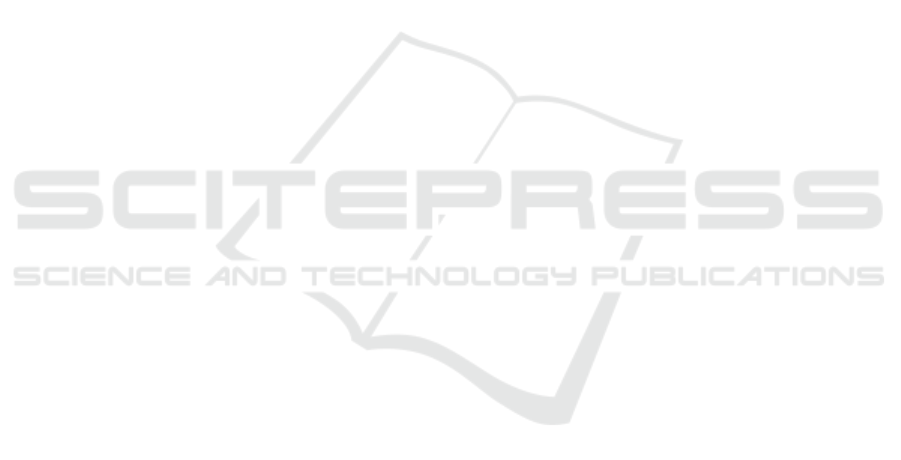
EVALUATING STRAIN SENSOR PERFORMANCE FOR MOTION
ANALYSIS
Giancarlo Orengo, Giovanni Saggio, Stefano Bocchetti and Franco Giannini
Università “Tor Vergata”, Dipartimento Ingegneria Elettronica, via Politecnico 1, 00133, Roma, Italy
Keywords: Piezoresistivity, Bend sensor, Motion analysis, Posture recognition.
Abstract: Investigation on the more suitable technologies to register human body movements in 3D space with great
spatial accuracy is a very challenging task, because a wide range of applications are concerned, from
registration of post-stroke rehabilitation or sports performance, to monitoring of movement of disabled or
elderly people, etc. In this paper the possibilities offered by piezoresistive bend sensors applied as wearable
devices, integrated on body garments, have been explored. Piezoresistive sensors can be usefully adopted to
recover human joint bend angles for body movement tracking. Due to their pliability, sensitivity and
cheapness, they could be a valid alternative to movement analysis systems based on optoelectronic devices
or inertial electronic sensors. This paper suggests a new approach to model their electrical behavior during
bending and extension movements, in order to predict their real-time performance during different kinds of
applications.
1 INTRODUCTION
Technology progress in the last decades has
provided the opportunity to observe human behavior
in 3D space with great spatial accuracy, thanks to
image-based methods or virtual reality tools. This is
a very challenging task, because a wide range of
applications are concerned, from registration of post-
stroke rehabilitation and sports performance, to
monitoring of movement of disabled and elderly
people, only to give some examples.
Optoelectronic techniques, based on infrared
cameras with reflective markers, for measurements
of human motions and gait analysis, have been
developed. However, these methods are conceived
for maximum reliability and precision in equipped
environments, such as a laboratory, and therefore are
usually expensive and/or not readily transportable,
complicated to set up, and finally do not guarantee
the visibility under all circumstances.
On the other hand, inertial and electromagnetic
sensors, such as accelerometers and gyroscopes, and
new technologies in the field of strain and bend
sensors can lead to the development of wearable
devices to solve the relevant outdoor application
problems in human posture recognition. Special
applications in the field of telerehabilitation are
under study (Draicchio F. et al., 2010 - Giorgino T.
et. al, 2009 - Dipietro L., 2008). Adoption of
wireless technologies allows the removal of wire
ties, which hinder the human motion (Saggio G. et
al., 2009).
In order to measure human body kinematics it is
convenient to adopt sensors, which can measure
bending angles with good precision despite a low
cost. Piezoresistive sensors can be made of a
polyester base material printed on with a special
carbon ink. The polyester acts as a support while the
ink's resistance increases the more it is bent. The ink
is screen printed so it can be applied on virtually any
custom shape and size film to fit to each body joint.
The substrate film material is usually formed by
Kapton and/or Mylar for their properties, stands the
fact that substrate must be able to bend repeatedly
without failure for the sensor to work. The sensor
can be over-molded (for instance with silicon or
urethane) and it can work in dirty environments (oil,
dust). This kind of sensors are available on the
market (Images SI Inc. Staten Island NY, Flexpoint
Sensor Systems Inc. South Draper UT, USA). They
can be applied to body joints as electronic
goniometers, to realize goniometric sock for rotation
assessment of body segments in human posture
recognition, or to goniometric gloves, which enable
multiple finger joint positions to be acquired
244
Orengo G., Saggio G., Bocchetti S. and Giannini F..
EVALUATING STRAIN SENSOR PERFORMANCE FOR MOTION ANALYSIS.
DOI: 10.5220/0003168402440249
In Proceedings of the International Conference on Biomedical Electronics and Devices (BIODEVICES-2011), pages 244-249
ISBN: 978-989-8425-37-9
Copyright
c
2011 SCITEPRESS (Science and Technology Publications, Lda.)