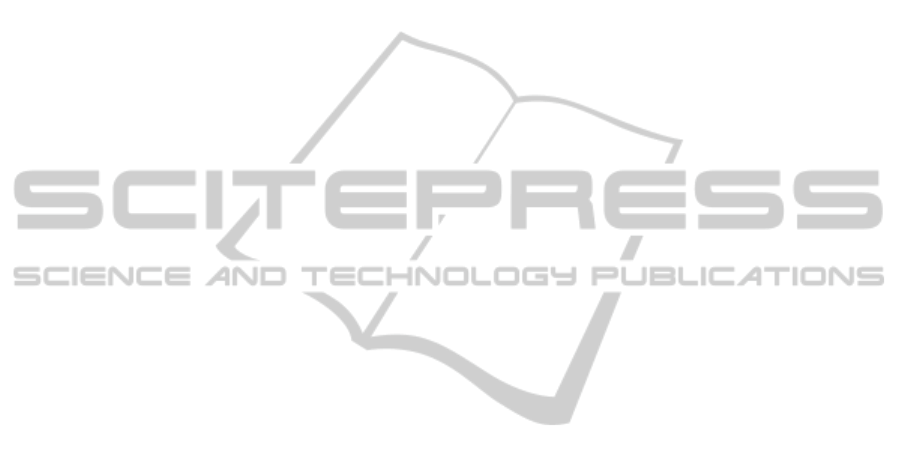
At the tube trial we were looking for the
maximum frequency of any requested address and it
results on 1.88 MHz for the 64x64 retina and 8.33
MHz for the 128x128 retina.
For the 64x64 pixel retina, if we join together the
10 ms obtained at the Lathe scenario between two
consecutive events of the same pixel, that could be
called frame time, and t2+t4+t5+t6 obtained on the
tubes scenario between any two consecutive events,
a maximum to 18867 addresses could be placed on
the AER bus. If we had considered an address space
of 4096 pixel, it would have confirmed the fact of no
lost events.
For the 128x128 pixel retina, it is possible to
pick up a similar case. If we considered the peak of
1.3KHz (769.23 us) like the top spike frequency for
a pixel and join it together with the sum of t2, t4, t5
and t6 obtained on the tubes scenario, it is possible
to place 6410 addresses within the frame time. If we
had considered an address space of 16384 pixel, it
noticed that lost events could appear with the peak
frequency selected, but this situation is not actually
very real because we have considered the peaks of
frequency spikes. If we have taken a frequency of
500 Hz, which is the saturation level for our test, no
lost events appears.
5 CONCLUSIONS
We have presented a study of two different
retinomorphic systems to use them in a visual
surveillance at any industrial environment. We have
checked the upper limit of the first system with a
Lathe, approximately 6000 rpm and no limits for the
second system at usual manufacturing machinery. It
has been tested at an ultra fast CNC Machine up to
10000rpm with an excellent result. Also, the results
reveal that in the worst condition of luminosity
change for our retinas there will be no lost of events
for the first one and at the second one could be some
very improbable lost event. Therefore, these AER
retinas can be used for a visual surveillance system
at any high speed industrial manufacturing
machinery.
ACKNOWLEDGEMENTS
This work was supported by the Spanish grant
VULCANO (TEC2009-10639-C04-02).
Also thanks to group Engineering Materials and
Manufacturing Technologies, TEP-027.
REFERENCES
Fookes, C., Denman, S., Lakemond, et al. 2010. Semi-
Supervised Intelligent Surveillance System for Secure
Environments.
Messinger, G. and G. Goldberg. 2006. Autonomous
Vision Networking - Miniature Wireless Sensor
Networks with Imaging Technology. Proceedings of
SPIE - The International Society for Optical
Engineering.
He, C., Papakonstantinou, A. and Chen, D. 2009. A Novel
SoC Architecture on FPGA for Ultra Fast Face
Detection.
Linsenmeier, Robert A. 2005. Retinal Bioengineering.
421-84.
Lichtsteiner, P. and Delbruck, T. 2005. A 64×64 AER
Logarithmic Temporal Derivative Silicon Retina.
Paper presented at 2005 PhD Research in
Microelectronics and Electronics Conference.
Lausanne. 25 July 2005 through 28 July 2005.
Lichtsteiner, P., C. Posch and T. Delbruck. 2008. A
128x128 120 dB 15 µs Latency Asynchronous
Temporal Contrast Vision Sensor. Solid-State Circuits,
IEEE Journal of 43:566-76.
Mead, C. A. and M. A. Mahowald. 1988. A Silicon Model
of Early Visual Processing. Neural Networks 1:91-7.
Boahen, K. 1996. Retinomorphic Vision Systems. Paper
presented at Microelectronics for Neural Networks,
1996., Proceedings of Fifth International Conference
on.
Culurciello, E., R. Etienne-Cummings and K. A. Boahen.
2003. A Biomorphic Digital Image Sensor. Solid-State
Circuits, IEEE Journal of 38:281-94.
Sivilotti, M.: Wiring Considerations in Analog VLSI
Systems with Application to Field-Programmable
Networks, Ph.D. Thesis, California Institute of
Technology, Pasadena CA (1991).
Serrano-Gotarredona, R., Oster, M., et al. 2009. CAVIAR:
A 45k Neuron, 5M Synapse, 12G connects/s AER
Hardware Sensory-Processing-Learning-Actuating
System for High-Speed Visual Object Recognition and
Tracking. IEEE Transactions on Neural Networks
20:1417-38.
Berner, R., Delbruck, T., et al. 2007. A 5 Meps $100
USB2.0 Address-Event Monitor-Sequencer Interface.
Paper presented at 2007 IEEE International
Symposium on Circuits and Systems, ISCAS 2007.
New Orleans, LA. 27 May 2007 through 30 May
2007.
Pérez-Peña F., Morgado-Estevez A., Linares-Barranco A.
et al. 2011. Frequency Analysis of a 64x64 pixel
Retinomorphic System with AER output to estimate
the limits to apply onto specific mechanical
environment. Proceedings presented at International
Work Conference on Artificial Neural Networks,
IWANN’11.
SIGMAP 2011 - International Conference on Signal Processing and Multimedia Applications
134