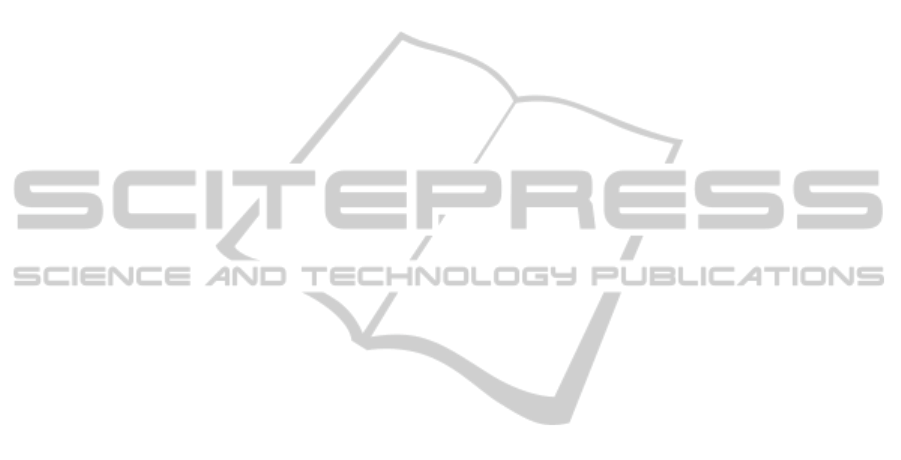
trust-region-reflective algorithm is used. This
algorithm is a subspace trust-region method and is
based on the interior-reflective Newton method.
Each iteration involves the approximate solution of a
linear system using the method of preconditioned
conjugate gradients (PCG).
3.2 Numerical Simulations
To assess model results, some experimental data
available, Milani & Milani (2011b) (cure-meter
curves for a commercial blend called Dutral TER
4049) are considered as reference data. To perform a
numerical optimization of the kinetic model
proposed, experimental cure values are normalized
dividing each point of the curve by the maximum
torque values, so that experimental data are always
within the range 0-1. In Figure 6 and Figure 7, a
comparison between cure curves provided by the
present approach and experimental results is
sketched for Dutral TER 4049, for a temperature
equal to 160°C and 200°C. Data for 180°C are also
available, but are not reported here for the sake of
conciseness.
As it is possible to notice, an almost perfect
agreement between the experimental data and the
numerical procedure proposed is found in both
cases, meaning that the simple second order
differential equation model proposed may represent
a valuable tool for all practitioners interested in a
fast evaluation of the reticulation degree of rubber
compounds vulcanized with accelerated sulphur.
4 CONCLUSIONS
From the results presented in this paper, the
following conclusions can be drawn:
1. Both the GA and the AT approaches are able to
determine optimal input parameters to optimize the
production of medium and high voltage power
cables, as well as of thick 3D items.
2. Numerical simulations have shown how different
mixtures of peroxides may: a) reduce optimal curing
time at almost constant optimized tensile strength or
b) increase optimal tensile strength with an
acceptable increase of curing time. Therefore, the
numerical procedure proposed may represent a
valuable tool for practitioners to obtain high quality
vulcanized items, limiting total curing time required.
3. For sulphur vulcanization, we have proposed a
mathematical kinetic model to predict EPDM
compounds reticulation level, which is based on a
best fitting procedure of experimental cure curves
obtained through rubber process analyzers (RPA
2000) following the ASTM D 5289 method or
ASTM D 2084-81 in a predetermined temperature
range. A simple second order non homogeneous
differential equation model has been derived directly
from the partial reactions occurring in series and
parallel during vulcanization with accelerated
sulphur. The model has demonstrated good
performance when compared to experimental cure-
curves available from a previous experimentation by
the authors.
REFERENCES
ASTM D 2084-81 and ASTM D 5289, Standard Test
Methods for Vulcanized Rubber and Thermoplastic
Elastomers.
Brydson, J. A., 1988. Rubbery Materials and Their
Compounds, Elsevier Science Publishers LTD, Essex.
Ding, R., Leonov, I., 1996. A kinetic model for sulfur
accelerated vulcanization of a natural rubber
compound. Journal of Applied Polymer Science, 61:
45.
Evans, G., Blackledge, J., Yardley, P., 2001. Numerical
methods for partial differential equations. Springer-
Verlag, Berlin, 2nd edition.
Goodyear, C., 1844. US Patent 3633.
Kresja, M. R., Koenig, J. L., 1993. A review of sulphur
cross-linking fundamentals for accelerated and
unaccelerated vulcanization.Rubber Chemistry and
Technology, 66: 376.
Milani, G., Milani, F., 2008. Genetic algorithm for the
optimization of rubber insulated high voltage power
cables production lines. Computers & Chemical
Engineering, 32: 3198-3212.
Milani, G., Milani, F., 2009. Optimization of power cable
production lines for EPM/EPDM elastomers by
Genetic Algorithm with different peroxides. Journal of
Applied Polymer Science, 111(1): 482-507.
Milani, G., Milani, F., 2010b. Optimal vulcanization of
2D-3D EPM/EPDM thick elements through peroxidic
mixtures. Journal of Mathematical Chemistry 47(1),
pp. 229-267.
Milani, G., Milani, F., 2010a. A new simple numerical
model based on experimental scorch curve data fitting
for the interpretation of sulphur vulcanization. Journal
of Mathematical Chemistry, 48: 530–557.
Milani, G., Milani, F., 2011a. A three function numerical
model for the prediction of vulcanization-reversion of
rubber during sulphur curing. Journal of
AppliedPolymer Science, 119(2), pp. 419–437.
Milani, G., Milani, F., 2011b. Simple kinetic model fitting
rheometer data for EPDMacceleratedsulphur. Under
review.
Treloar, L. R. G., 1975. The Physics of Rubber
Elasticity,3d ed., Clarendon Press, Oxford.
SIMULTECH 2011 - 1st International Conference on Simulation and Modeling Methodologies, Technologies and
Applications
92