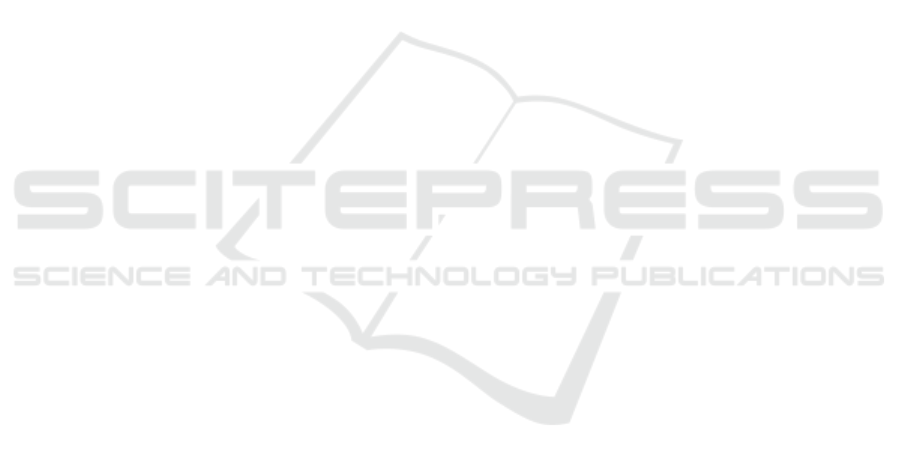
COOPERATIVE MODELING AND DYNAMICS SIMULATION
OF FLEXIBLE MULTI-BODY SYSTEM FOR PARALLEL ROBOT
Yongxian Liu
1
, Chunxia Zhu
1
and Jinfu Zhao
2
1
School of Mechanical Engineering and Automation, Northeastern University, Shenyang, China
2
Liaoning Energy Key Project Investment, Limited Liability Company, Beiling Street, Huanggu District, Shenyang, China
Keywords: Parallel robot, Dynamics of flexible multi-body, Cooperative, Modeling, Simulation, ADAMS, ANSYS.
Abstract: Based on the cooperative thought, a method of modeling and simulation of multi-flexible-body dynamics
for a kind of mechanism is proposed in this paper. A multi-flexible-body dynamics simulation model of 3-
TPT parallel robot is created, and its multi-body dynamics simulation is implemented by using the multi-
body dynamics simulation software ADAMS and finite element analysis software ANSYS. For more
accurate explanation of the analysis, simulation results of rigid body are compared with those of flexible
body. The simulation results have shown that forces applied on flexible bodies are highly nonlinear because
of the flexible characteristics, which is consistent with the reality. Compared with other simulation method,
the simulation proposed of the multi-flexible body system are more authentic, nicety and can reflect actual
dynamics characteristic of parallel robot with more accuracy. Therefore this is an effective method of
analysis for design and optimization of parallel robot.
1 INTRODUCTION
Flexible multi-body system generally consists of
rigid body and flexible body which interact with
each other the motion of these components unit may
be translational or rotational under the effect of
power. The traditional multi-body system dynamics
research is carried out mainly in the multi-rigid-body
field, however, because of the rigid assumption
sometimes its result will lose certain precision, even
can't be accepted (Shabana A. A, 1997). With
development of modern mechanical system towards
to high speed, heavy load, high-precision direction,
designers pay more and more attention to dynamic
stress of the component and the service life
prediction of product, elastic dynamics issue
resulting from the coupling between rigid motion
and the deformation itself of the system has already
become the common problems needed to be resolved
and key technology in this field. Therefore
considering the flexible of all the parts in order to
improve the precision of the simulation analysis
becomes an important direction of parallel robot
research (Fattah et al., 1995; Gamarra, 1999).
Robot dynamics simulation analysis is an
important content of robot design, the model
established in the previous analysis, whose
components belong to a rigid body, and don’t have
elastic deformation when making motion analysis.
But in fact, on the condition of the larger load, or
acceleration and deceleration, it will have larger
deformation and displacement after the mechanism
got forced, resulting in vibration. In order to solve
these problems, we should establish the reasonable
elastic dynamics model of the parallel robot, based
on this research the impact of its dynamic
performance and structure and geometrical
parameters on dynamic properties, put forward the
corresponding structure optimization design method
(Chen, 2001).
ADAMS software is well-known mechanical
system dynamics simulation software, its analysis
object is basically the multi-rigid-body, but the
ADAMS provides a flexible body module, the
module can be used to achieve motion simulation
analysis of flexible body and substitute elastic body
for rigid body. ANSYS software is a universal finite
element analysis software, with a friendly cross-
section before and after the treatment, accurate and
efficient solver, has been widely used in various
fields, it can effectively integrated the finite element
analysis with CAD, CAE organically. In this paper,
combining advantages of two kinds of software, the
flexible multi-body system is established to conduct
321
Liu Y., Zhu C. and Zhao J..
COOPERATIVE MODELING AND DYNAMICS SIMULATION OF FLEXIBLE MULTI-BODY SYSTEM FOR PARALLEL ROBOT.
DOI: 10.5220/0003566303210324
In Proceedings of the 8th International Conference on Informatics in Control, Automation and Robotics (ICINCO-2011), pages 321-324
ISBN: 978-989-8425-75-1
Copyright
c
2011 SCITEPRESS (Science and Technology Publications, Lda.)