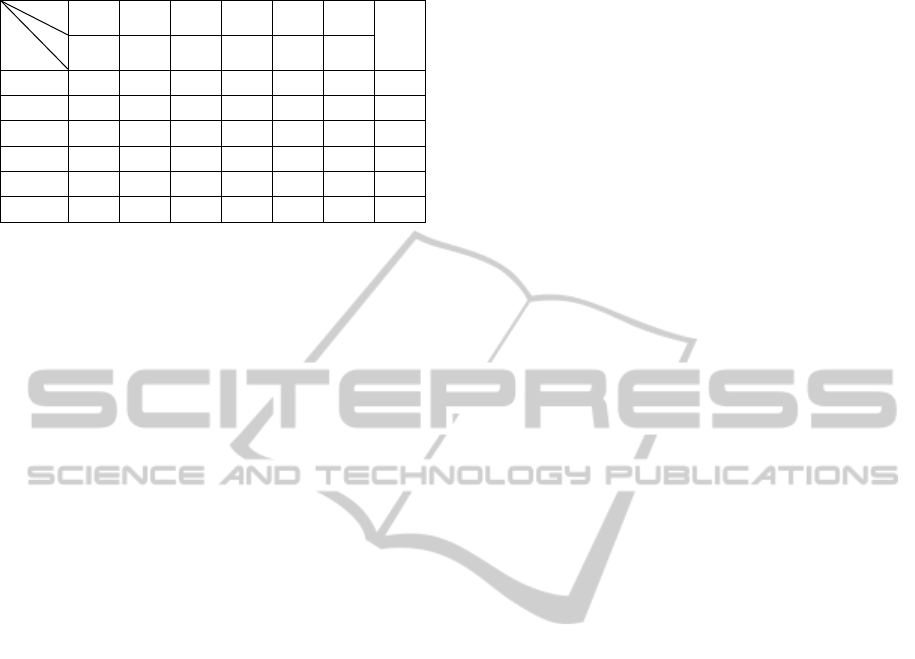
Table 4: Decision matrix of the second supplier.
Ei
Pi
Si
E1 E2 E3 E4 E5 E6
∑
0.15 0.10 0.25 0.20 0.15 0.15
S1 0.24 0.17 -0.17 -0.23 0.25 -0.24 -0.03
S2 0.10 0.17 -0.14 -0.19 0.10 -0.12 -0.04
S3 0.11 0.13 -0.20 -0.13 0.16 -0.12 -0.04
S4 0.17 0.22 -0.22 -0.16 0.13 -0.24 -0.05
S5 0.23 0.13 -0.15 -0.18 0.27 -0.18 -0.01
S6 0.15 0.17 -0.12 -0.11 0.08 -0.12 -0.02
In this example, firm A should choose the fourth
supplier S
2 as its main supplier, and the fifth supplier
S
4 as its second supplier.
If a firm considered more factors when it chooses
suppliers, such as distance, methods and price of
transportation, exchange rate fluctuations, changes
in demand and raw materials cost, etc, these factors
can be transformed to special risk indicators, and use
this model to choose the suitable suppliers.
4 CONCLUSIONS
As one of the most important part of supply chain,
supply disruption may bring great loss to the
enterprise and the whole supply chain, even break
down the whole supply chain. This paper analyses
the composition of supply risk, and methods to
mitigate supply risk, addresses dual-supplier or
multi-supplier supply model may be an effective
method. In order to choose suppliers for the whole
supply chain, a mathematical model is developed
and verified by a numerical example.
ACKNOWLEDGEMENTS
Our thanks go to everyone who supported our work,
and who provided us lots of material. We also thank
the team members from the company who sponsored
this work, whose support is greatly appreciated.
REFERENCES
Jian Li, Shouyang Wang, T. C. E. Cheng, 2010,
Competition and cooperation in a single-retailer
two-supplier supply chain with supply disruption, Int.
J. Production Economics 124, 137–150.
Scott C. Ellis, Raymond M. Henry, Jeff Shockley, 2009,
Buyer perceptions of supply disruption risk: A
behavioural view and empirical assessment, Journal of
Operations Management 28, 34-36.
Xueipng Li, Yuerong Chen, 2009, Impacts of supply
disruptions and customer differentiation on a
partial-backordering inventory system, Simulation
Modelling Practice and Theory 18, 547–557.
Zhang Yi-bin,Chen J un-fang, 2007, A Framework of
Identifying Supply Chain Risks and Their Flexible
Mitigating Polices, Industrial Engineering and
Management, 47-52.
Chen Chang-bin, Miu Li-xin, 2009, An Analysis of
Supply — chain Classification , vulnerability and
Management Method, business economy, 98-101.
Li Leiming, Liu Bingquan, 2010, Research Review of the
Management Research of the Supply Chain Disruption
Risk, Science and Technology Management Research,
236-239.
Lou Shan-zu0,Wu Yao-hua,Lu Wen,Xiao Ji-wei, 2010,
Optimal inventory management under stochastic
disruption, Systems Engineering — Theory &
Practice,469-475.
R. Eglin, 2003, Can suppliers bring down your firm?
Sunday Times (London), appointments sec., p. 6.
Oke, A., Gopalakrishnana, M., 2009, Managing
disruptions in supply chains: a case study of a retail
supply chain. International Journal of Production
Economics 118 (1), 168–174.
Craighead, C. W., Blackhurst, J., Rungtusanatham, M. J.,
Handfield, R. B., 2007, The severity of supply chain
disruptions: design characteristics and mitigation
capabilities. Decision Sciences 38 (1), 131–156.
S. Chopra, M. Sodhi, 2004, Managing risk to avoid
supply-chain breakdown, MIT Sloan Management
Review 46 (1) 53–61.
Sheffi, Y., Rice Jr., J., 2005, A supply chain view of the
resilient enterprise. MIT Sloan Management Review
47 (1), 41–48.
Hendricks, K. B., Singhal, V. R., 2003, The effect of
supply chain glitches on shareholder wealth. Journal of
Operations Management 21 (5), 501–522.
Tomlin, B., 2005, Selecting a disruption-management
strategy for short life-cycle products: diversification,
contingent sourcing, and demand management
Working Paper, Kenan-Flagler Business School,
University of North Carolina.
Tomlin, B., 2006, On the value of mitigation and
contingency strategies for managing supply-chain
disruption risks. Management Science 52, 639–657.
Lariviere, M. A., Porteus, E. L., 2001, Selling to a
newsvendor: an analysis of price-only contracts.
Manufacturing & Service Operations Management 3,
293–305.
Wang, Y., Gerchak, Y., 2003. Capacity games in assembly
systems with uncertain demand. Manufacturing &
Service Operations Management 5, 252–267.
Tomlin, B., 2003. Capacity investment in supply chains:
sharing the gain rather than sharing the pain.
Manufacturing & Service Operations Management 5,
317–333.
ICEIS 2011 - 13th International Conference on Enterprise Information Systems
548