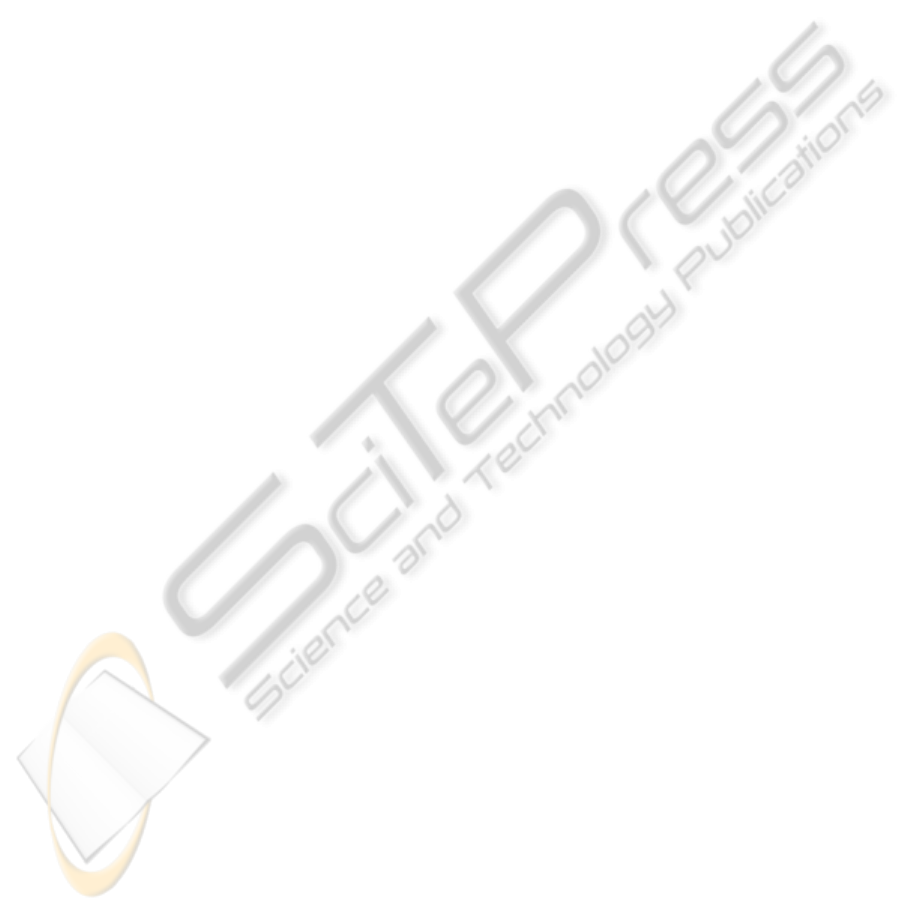
2 OBJECTIVES OF THE STUDY
The manufacturer in this study is currently conducting
a project to increase traceability of its products during
shipping. The project began in late 2008 and will last
three years. Among several technologies, RFID will
be used. On this occasion, a question is raised: Will
system performance be improved if RFID is also used
in internal processes? Indeed, if so, the implementa-
tion of RFID will be facilitated by previous experi-
ence gained through the project.
In addition, the manufacturer is interested in im-
proving its internal processes by other means than
RFID. In fact, improvements upstream of the shipping
may boost performance of the entire supply chain and
profitability of the project. By a careful observation
of the real system, we identified some directions of
improvement such as reallocation of human resources
based on resource utilization or work in process indi-
cators.
Moreover, for different reasons, the manufacturer
has in mind some scenarios and changes in his inter-
nal processes that he wishes to test. For example, us-
ing a single building instead of two (see Section 3).
Another example is processing new types of products.
Therefore, a simulation model was developed to
answer all these questions. Even thought the study
aims to address all the issues previously raised, this
paper will only address RFID issue. Results of the
simulation are an estimation of impact of RFID intro-
duction in the manufacturing case.
3 PROBLEM DESCRIPTION AND
SIMULATION MODEL
In this study, the simulation model represents a real
activity in a factory, in the north of France. The fac-
tory is part of an international group and has dif-
ferent activities. The activity we are interested in
is Configuration-To-Order (CTO) of printers. It is
spread over two buildings: The Logistic Center (LC)
and the Setup Center (SC). In the first building, items
are stored until customers orders are placed. Once this
is done, items are sent to the second building in order
to be assembled together.
3.1 Processes in the Logistic Center
Figure 1 shows the two buildings and processes that
are executed inside them. Even though real and mod-
eled processes are rather complex, they are explained
in a concise and simplified way below.
In the LC (in orange on Figure 1), activity is di-
vided into two rather separate parts: Goods receiving
and storage, on the one hand, and items destocking
and orders preparation, on the other hand.
Regarding the first part of the activity, goods are
delivered by trucks, three times a day. In each truck,
there is a variable number of products. These are
of different types (hundreds types in the real system,
grouped into six types in the model). The arrival of
a truck triggers the beginning of goods receiving pro-
cess. Indeed, LC employees unload the truck, per-
form computer input, bar codes reading, and resize
pallets if needed (in case of oversized and undersized
pallets). When receiving process is finished for the
entire contents of the truck, pallets are stored one by
one in racks.
The second part of the activity in the LC is orders
destocking and preparing. Each order consists of a
single printer and several options. When the demand
is known, items from different orders are grouped
and destocked by tours in order avoid unnecessary
roundtrips of employees and pallet trucks. During
destocking process, some bar codes readings are per-
formed and can be suppressed if we use RFID. After
destocking of all products of a tour, items of the same
order are placed together on a pallet and their bar
codes are read to prevent discrepancies, this process
is called order preparing. From this step, items of the
same order are gathered together on a single pallet.
Therefore, we shall no longer speak about items but
orders or printers. The last process in the LC is ship-
ping of orders to the SC. Indeed, a computer input is
performed for each tour of orders, items are loaded in
a truck and sent to the SC. Note that computer input
can be suppressed by using RFID.
3.2 Processes in the Setup Center
When orders arrive to the SC, employees unload the
truck and execute a computer input process in order
to update the database. Then, orders are unpacked
in parallel workstations. In order to keep traceability,
bar codes on packaging are cut and held with orders
to configuring process. During the latter, printers are
assembled with their options in parallel workstations.
After configuring, some printers may be defective and
require repair. The other printers go to computer input
process at the exit of the building. In addition to com-
puter input, printers are filmed, labeled and placed in
a shipping area in order to wait for shipping trucks
arrival.
SIMULTECH 2011 - 1st International Conference on Simulation and Modeling Methodologies, Technologies and
Applications
524