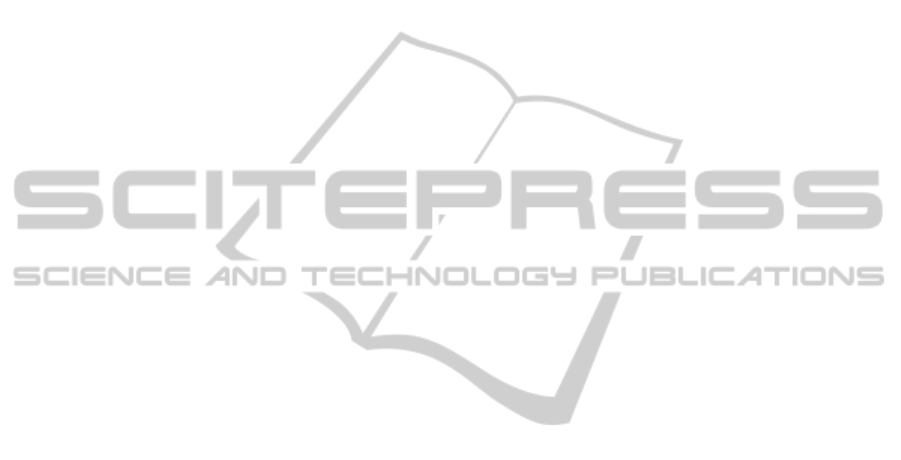
With respect to the mentioned facts an efficient
and application-oriented modelling of the current
state of the production system with a method called
Method for Multi-Scale Production System
Modelling (MePro) is supported (Figure 3).
6 ROADMAP TO MEPRO
The development of a method for structured and
multi-scale modelling of an existing production
system is a new and complex research topic where
future steps are of huge interest. Thus, the next
research steps for building the foundations of MePro
are the analysis and evaluation of:
• System theory for production system modelling;
• Application fields for production system modelling
and of existing modelling methods;
• Existing production system resource libraries;
• Metamodels for modelling processes;
The research results will be merged in a MePro.
Different challenges have to be considered on this
way:
• Development of criteria for application-oriented
modelling method selection;
• Development of workflows for an application-
oriented modelling of a production system;
• Development of a supporting resource library with
predefined and/or configurable objects and
interdependencies.
REFERENCES
Bertalanffy, L., 1968. General System Theory:
Foundations, Development, Applications, George
Braziller Inc. New York, 2nd edition.
Brinkkemper, S., 1999. Method engineering: engineering
of information systems development methods and
tools. In Information & Software Technology 38, pp.
275-280.
Feig, M., Karanicolas, J., Brooks, C. L., 2004. MMTSB
Tool Set: enhanced sampling and multi-scale
modeling methods for applications in structural
biology. In Journal of Molecular Graphics and
Modelling 22, pp. 377-395.
Herrmann, C., 2010. Ganzheitliches Life Cycle
Management-Nachhaltigkeit und Lebenszykluso
rientierung in Unternehmen, Springer. Berlin.
Hernández Morales, R., 2003. Systematik der
Wandlungsfähigkeit in der Fabrikplanung, VDI
Verlag, Düsseldorf.
Hitzler, P., Krötzsch, M., Rudolph, S., Sure, J., 2008.
Semantic Web Grundlagen, Springer, Berlin.
Jovane, F., Westkämper, E., Williams, D., 2009. The
Manufuture Road: Towards Competitive and
Sustainable High-Adding-Value Manufacturing,
Springer. Berlin.
Lankhorst, M., 2009. Enterprise Architecture at Work -
Modelling, Communication and Analysis, Springer,
Berlin, 2nd edition.
Mertins, K., Süssenguth, W., Jochem, R., 1994.
Modellierungsmethoden für rechnerintegrierte
Produktionsprozesse: Unternehmenmodellierung –
Softwareentwurf – Schnittstellendefinition –
Simulation, Hanser. München.
Mirbel, I., Jolita, R., 2005. Situational method
engineering: combining assembly-based and roadmap-
driven approaches, Springer. London.
Ropohl, G., 2009. Allgemeine Technologie. Eine
Systemtheorie der Technik, Universitätsverlag,
Karlsruhe, 3rd edition.
Schady, R., 2007. Methode und Anwendung einer
wissensorientierten Fabrikmodellierung, Dissertation,
Magdeburg.
Scheer, A.W., 1994. Prozessorientierte Unternehmens-
modellierung Grundlagen – Werkzeuge –
Anwendungen, Gabler. Wiesbaden.
Schenk, M., Wirth, S., Müller, E., 2004. Fabrikplanung
und Fabrikbetrieb. Methoden für die wandlungsfähige
und vernetzte Fabrik, Springer, Berlin.
Schenk, M., Wirth, S., Müller, E., 2010. Factory Planning
Manual: Situation-Driven Production Facility
Planning, Springer, Berlin.
Shen, H., Wall, B., Zaremba, M., Chen, Y., Browne, J.,
2004. Integration of business modelling methods for
enterprise information system analysis and user
requirements gathering. In Computers in Industry 54,
pp. 307-323.
Söderström, E., Andersson, B., Johannesson, P., Perjons,
E., Wangler, B., 2002.Towards a Framework for
Comparing Process Modelling Languages. In
Proceedings of the 14th International Conference on
Advanced Information Systems Engineering, pp. 600-
611. Springer.
Vajna, S., Weber, C., Bley, H., Zeman, K., 2009. CAx für
Ingenieure: Eine praxisbezogene Einführung,
Springer. Berlin.
Vernadat, F. B., 2002. Enterprise Modelling and
Integration (EMI): Current Status and research
perspectives. In Annual Reviews in Control 26, pp. 15-
25.
Wenzel, S., Jessen, U., Jochen, B., 2005. Classifications
and conventions structure the handling of models
within the Digital Factory. In Computers in Industry
56, pp. 334-346.
Westkämper, E., Zahn, E., 2009. Wandlungsfähige
Produktionsunternehmen: Das Stuttgarter
Unternehmensmodell, Springer. Berlin.
SIMULTECH 2011 - 1st International Conference on Simulation and Modeling Methodologies, Technologies and
Applications
216