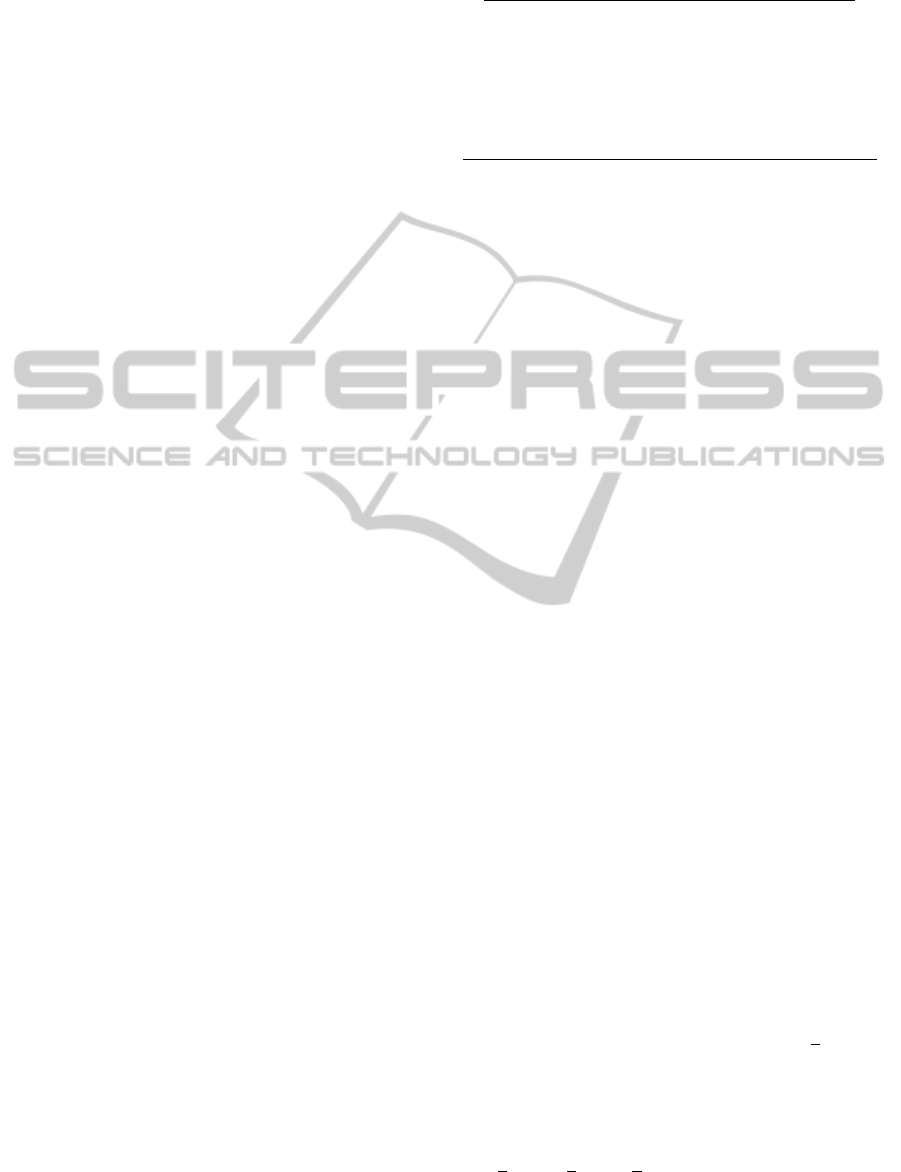
R-at-W2-Flag, R-at-W4-Flag, F-Flag and I-Flag has
the value of 0, the work is detected as a defect at W7.
Such defects are sorted according to the values of the
flags and are dropped into appropriate cells. Sensor
M checks the presence of a work at W8. If it finds
a work, the values of R-at-W2-Flag, R-at-W4-Flag,
F-Flag and I-Flag for the work are examined. If any
of them is 0, it means that the work is failed to be
detected as a defect at W7 and “FDD Al” is issued
where FDD means Failure to Detect a Defect. After
W8, each work is passed over to W9 without doing
anything and reaches W10 where it is pushed out into
a tray as a finished product. Necessary statistics are
also collected at W10 to see if the cumulative yield
of finished products stays above a pre-specified level.
If this level is not met, “YF Al” is reported with YF
meaning Yield of Finished products.
The wheel mechanism continues to rotate over
W11 and Sensor N at W12 examines to make sure
that there is no work present at W12. If any, it im-
plies that a finished product was not taken out appro-
priately at W10 and “FRF Al” is issued where FRF
stands for Failure to Retrieve a Finished product. The
definitions of the flags are provided in Table 1. The
ten minor-stoppages of principal interest to this paper
discussed above are summarized in Table 2.
3 DEVELOPMENT OF
ASSOCIATION RULES FOR
PREVENTING
MINOR-STOPPAGES BASED
ON SEQUENTIAL DATA
For analytical purposes, we define a “window” as a
set of works constituting a production lot, typically
with its size in the range from 5000 to 60000 and its
average around 30000. All orders under considera-
tion are then expressed as a sequence of windows of
length K along the time axis for each testing machine.
The purpose of this section is to develop association
rules, each of which indicates that the occurrence of
a certain combination of minor-stoppages in a certain
pattern within 2 consecutive windows would be likely
to result in the occurrence of specific minor-stoppages
in the immediately following window.
The problem of how to mine association rules
from a large-scale data set has been addressed by
many researchers, represented by (Agrawal et al.,
1993) and (Agrawal and Srikant, 1994). Sub-
sequently, the association rule approach has been
applied to sequential data for prediction, see e.g.
(Agrawal and Srikant, 1995), (Lu et al., 1998), (Jiang
Table 1: The definitions of the flags.
Name Position Sensor
R-at-W2-Flag Recognizable at W2 W2 G
R-at-W4-Flag Recognizable at W4 W4 I
F-Flag Frequency W5 -
I-Flag Insulation W6 -
Table 2: The ten minor-stoppages.
Name Position Sensor
PF-Stuck Al Parts Feeder Stuck Linear-feeder D,E,F
WC Al Work Completion Linear-feeder E,F
WS-F Al Work Supply Failure W1 F
PASM Al Pre-Alignment W3,W4 G,H,I
Sucking Miss
WL-at-W5 Al Work Left at W5 W5 J
WL-at-W6 Al Work Left at W6 W6 K
SM Al Sucking Miss W7 F,L
FDD Al Failure to Detect a Defect W8 M
YF Al Yield of Finished product W10 -
FRF Al Failure to Retrieve W12 N
a Finished product
and Gruenwald, 2006) and (Qin and Shi, 2006) to
name a few. However, these papers are exclusively
dealing with marketing problems. To the best knowl-
edge of the authors, the sequential association rule ap-
proach has not been applied to production control.
Real data have been collected from a semi-
conductor factory producing SAW devices. The data
set consisting of K
L
windows would be used as the
learning data and a set of association rules would be
established tentatively by following the procedure de-
scribed in this section. The next K
T
windows would
be then used as the testing data, where a tentative as-
sociation rule is chosen to be a formal rule if the ac-
curacy of the association rule over the testing data ex-
ceeds a pre-specified level. For each of such formal
rules, an action plan is devised so as to reduce the
minor-stoppages.
In practice, the learning data may be collected for
3 months, while the testing data may consist of the
windows over the subsequent 2 months. The result-
ing selected association rules would be applied to real
data for 1 month following the testing period so as to
reduce minor-stoppages. This learning-testing proce-
dure would be repeated monthly on a rolling horizon
basis for updating the selected association rules.
Let N = {1,...,N} be the set of types of
minor-stoppages under consideration, and define
the minor-stoppage occurrence vector x
T
(k) =
[x(k,1),... ,x(k,i),... ,x(k, N)], where x(k,i) denotes
the number of minor-stoppages of type i occurred in
the k-th window. We intend to establish association
rules by observing the incremental changes
∆x
T
(k) = x
T
(k) − x
T
(k− 1), k = 2,...,K
L
, (1)
in relative to its mean and variance over the entire K
L
ICORES 2012 - 1st International Conference on Operations Research and Enterprise Systems
352