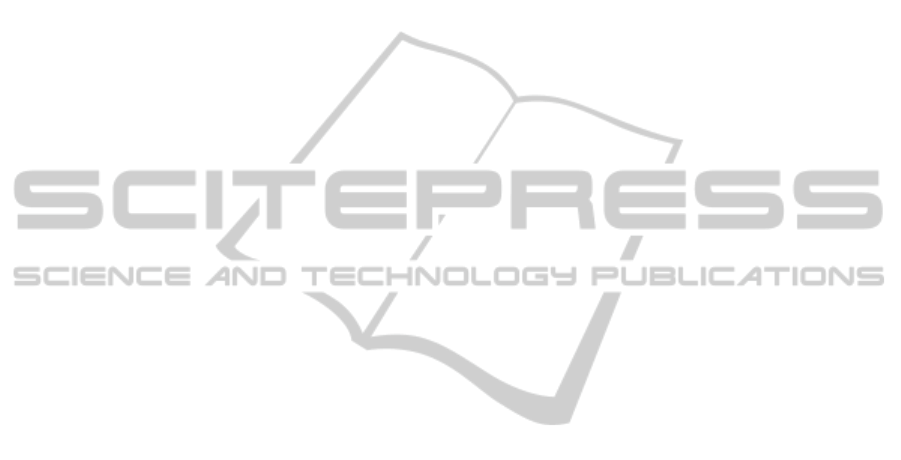
the development of an energy harvesting system
from multiple sources for smart hip prosthesis.
Considering the energy obtained from the movement
as the most abundant in the human body, three
energy harvesting power bio-generators, namely a
piezoelectric-based and two electromagnetic-based
harvesting elements, were designed to harvest energy
from several movements over the femoral component.
They were able to produce energy to supply the
power needs of a telemetric system. This approach
ensures the availability of the electric power supply
and operates autonomously, safely and without
maintenance during the lifetime of the hip prosthesis.
An ongoing optimization of the harvesting elements
is being conducted in order to improve the electric
power bio-generation up to levels required by the
active actuators that would prevent the aseptic
loosening.
ACKNOWLEDGEMENTS
The present work was conducted with the support of
the FCT - Foundation for Science and Technology,
under the PTDC/EME-PME/105465/2008 project.
REFERENCES
Alpuim, P., Filonovich, S., Costa, C., Rocha, P., Vasilevskiy,
M., Lanceros-Mendez, S., Frias, C., Marques, A.,
Soares, R., and Costa, C. (2008). Fabrication of
a strain sensor for bone implant failure detection
based on piezoresistive doped nanocrystalline silicon.
Journal of Non-Crystalline Solids, 354:2585–2589.
Beeby, S., Tudor, M., and White, N. (2006). Energy
harvesting vibration sources for microsystems
applications. Measurement Science and Technology,
17:R175–R195.
Beeby, S. and White, N. (2010). Energy Harvesting for
Autonomous Systems. Artech House, Norwood, MA,
EUA.
Carmo, J., Ribeiro, J., Silva, M., Goncalves, L., and
Correia, J. (2010). Thermoelectric generator and
solid-state battery for stand-alone microsystems.
Journal of Micromechanics and Microengineering,
20:1–8.
Cook-Chennault, K., Thambi, N., and Sastry, A. (2008).
Powering mems portable devices a review of
non-regenerative and regenerative power supply
systems with special emphasis on piezoelectric energy
harvesting systems. Smart Materials and Structures,
17:1–33.
Damm, P., Graichen, F., Rohlmann, A., Bender, A., and
Bergmann, G. (2010). Total hip joint prosthesis for
in vivo measurement of forces and moments. Medical
Engineering & Physics, 32:95–100.
duToit, N., Wardle, B., and Kim, S. (2005). Design
considerations for mems-scale piezoelectric
mechanical vibration energy harvesters. Integrated
Ferroelectrics, 71:121–160.
Frias, C., Reis, J., e Silva, F. C., Potes, J., Sim˜oes, J., and
Marques, A. (2010). Polymeric piezoelectric actuator
substrate for osteoblast mechanical stimulation.
Journal of Biomechanics, 43:1061–1066.
Gilbert, J. and Balouchi, F. (2008). Comparison of energy
harvesting systems for wireless sensor networks.
International Journal of Automation and Computing,
5(4):334–347.
Graichen, F., Bergmann, G., and Rohlmann, A. (1999).
Hip endoprosthesis for in vivo measurement of joint
force and temperature. Journal of Biomechanics,
32:1113–1117.
Heinlein, B., Graichen, F., Bender, A., Rohlmann, A.,
and Bergmann, G. (2007). Design, calibration and
pre-clinical testing of an instrumented tibial tray.
Journal of Biomechanics, 40:S4–S10.
Heinlein, B., Kutzner, I., Graichen, F., Bender, A.,
Rohlmann, A., Halder, A., Beier, A., and Bergmann,
G. (2009). ESB clinical biomechanics award 2008:
Complete data of total knee replacement loading for
level walking and stair climbing measured in vivo with
a follow-up of 610 months. Clinical Biomechanics,
24:315–326.
Ida, N. (2004). Engineering Electromagnetics. Springer,
New York, 2nd edition.
Kalogirou, S. (2000). Applications of artificial
neural-networks for energy systems. Applied
Energy, 67:17–35.
Ka´zmierski, T. and Beeby, S. (2011). Energy Harvesting
Systems - Principles, Modeling and Applications.
Springer, New York, EUA.
Kerzenmacher, S., Ducr´ee, J., Zengerle, R., and von
Stetten, F. (2008). Energy harvesting by implantable
abiotically catalyzed glucose fuel cells. Journal of
Power Sources, 182:1–17.
Kurtz, S., Ong, K., Lau, E., Mowat, F., and Halpern,
M. (2007). Projections of primary and revision hip
and knee arthroplasty in the united states from 2005
to 2030. The Journal of Bone and Joint Surgery
(American), 89(4):780–785.
Lu, M., Zhang, G., Fu, K., Yu, G., Su, D., and Hu, J. (2011).
Gallium nitride schottky betavoltaic nuclear batteries.
Energy Conversion and Management, 52:1955–1958.
Marcelli, E., Scalambraa, F., Cercenelli, L., and Plicchi,
G. (2007). A new hermetic antenna for wireless
transmission systems of implantable medical devices.
Medical Engineering & Physics, 29:140–147.
Marschner, U., Grtz, H., Jettkant, B., Ruwischa, D.,
Woldt, G., Fischer, W., and Clasbrummel, B. (2009).
Integration of a wireless lock-in measurement of hip
prosthesis vibrations for loosening detection. Sensors
and Actuators A: Physical, 156:145–154.
Morais, R., Frias, C., Silva, N., Azevedo, J., Serˆodio, C.,
Silva, P., Ferreira, J., Sim˜oes, J., and Reis, M. (2009).
An activation circuit for battery-powered biomedical
BIODEVICES 2012 - International Conference on Biomedical Electronics and Devices
80