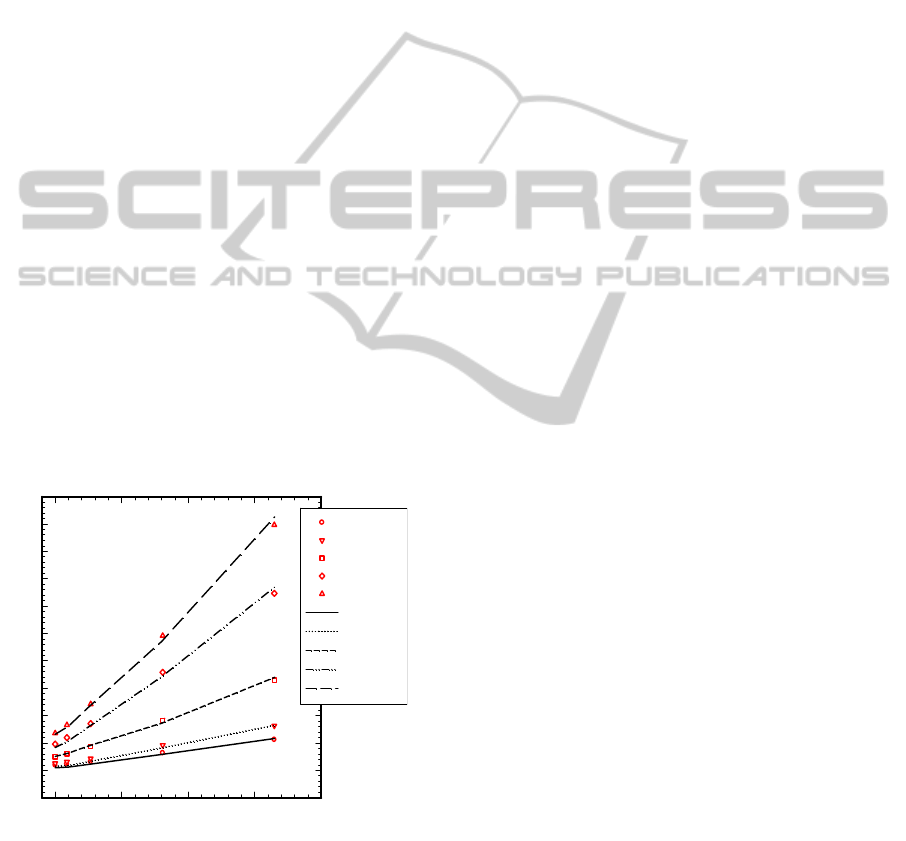
6.2 Viscoelastic Modeling
It is again instructive to compare individual
distributions of pressure and temperature between
the viscous and the viscoelastic models. This is done
in Fig. 5, where we show the pressure results from
the K-BKZ models for the several pressure drops as
in Fig. 3. The viscoelastic pressures are markedly
higher than the viscous ones, and in fact they predict
the experimental data very well. More detailed
simulation results for various cases have shown that
the K-BKZ equation is capable of capturing all
important effects including the effects of
compressibility, pressure, viscous heating and
entrance pressure on the overall pressure required in
the capillary flow of LDPE.
7 CONCLUSIONS
A commercial low-density polyethylene melt
(LDPE) has been studied in entry flows through
tapered dies with different L/D ratios. The
experiments have shown a distinct pressure-
dependence of viscosity with a pressure coefficient
to be a power-law function of pressure. Full
rheological characterization was carried out both
with a viscous (Carreau-Yasuda) and a viscoelastic
(K-BKZ) model. All necessary material properties
data were collected for the simulations.
L / D
0 10203040
Δ
P (MPa)
-5
0
5
10
15
20
25
30
35
40
45
50
γ
A
=5 s
-1
γ
A
=11 s
-1
γ
A
=64 s
-1
γ
A
=390 s
-1
γ
A
=1000 s
-1
γ
A
=5 s
-1
γ
A
=11 s
-1
γ
A
=64 s
-1
γ
A
=390 s
-1
γ
A
=1000 s
-1
LDPE,
T=160
o
C
symbols=exp.
K-BKZ lines
.
.
.
.
.
.
.
.
.
.
Figure 5: The effect of L/D on the pressure for the LDPE
melt at 160
o
C at various values of apparent shear rate.
Non-isothermal simulations with the K-BKZ model with
pressure-dependence of the viscosity (variable
β
p
).
The viscous model was found to underestimate
the extrusion pressures. The viscoelastic model
showed a very good agreement with the
experimental results, which appears to be the first in
the literature for the elastic LDPE melt. The
simulations showed that: (a) compressibility is not
important in these steady flows; (b) viscous
dissipation is important, especially for the more
severe conditions (high L/D and apparent shear
rates); and (c) the pressure-dependence of viscosity
is very important and its correct function has to be
found experimentally. This is the first time that all
these effects are taken into account in a viscoelastic
simulation.
ACKNOWLEDGEMENTS
Financial assistance from the Natural Sciences and
Engineering Research Council (NSERC) of Canada
and the programme “PEBE 2009-2011” for basic
research from NTUA are gratefully acknowledged.
REFERENCES
Aho J., Syrjälä S., J. App. Polym. Sci., 117, 1076-1084
(2010).
Ansari M., A. Alabbas, E. Mitsoulis, S.G. Hatzikiriakos,
Intern. Polym. Proc., 25, 287-296 (2010).
Dealy, J. M., Wissbrun, K. F., Melt Rheology and its Role
in Plastics Processing - Theory and Applications, Van
Nostrand Reinhold, New York (1990).
Bagley, E. B., J. Appl. Phys., 28, 193-209 (1957).
Barakos, G., Mitsoulis, E., J. Non-Newtonian Fluid Mech.,
62, 55-79 (1996).
Barakos, G., Mitsoulis, E., J. Rheol., 39, 193-209 (1995a).
Barakos, G., Mitsoulis, E., J. Non-Newtonian Fluid Mech.,
58, 315-329 (1995b).
Béraudo, C., Coupez, T., Fortin, A., Demay, Y., Vergnes,
B., Agassant, J.-F., Proc. XIIth Int. Congr. Rheology,
Eds. A. Ait-Kadi, J.M. Dealy, D.F. James, M.C.
Williams, Quebec City, Canada, pp. 417-418 (1996).
Cardinaels R., Van Puyvelde P., Moldenaers P., Rheol.
Acta, 46, 495-505 (2007).
Carreras, E. S., El Kissi, N., Piau, J.-M., Toussaint, F.,
Nigen, S., Rheol Acta, 45, 209–222 (2006).
Couch M. A., Binding, D. M., Polymer, 41, 6323-6334
(2000).
Dinh, S. M., Armstrong, R. C., AIChE J., 28, 294-301
(1982).
Feigl, K., Öttinger, H. C., J. Rheol., 38, 847-874 (1994).
Guillet, J., Revenue, P., Béreaux, Y., Clermont, J.-R.,
Rheol. Acta, 35, 494-50 (1996).
Hatzikiriakos, S.G., Mitsoulis, E., Rheol. Acta, 35, 545-
555 (1996).
Laun H. M., Rheol. Acta, 42, 295–308 (2003).
Kajiwara, T., Barakos, G., Mitsoulis, E., Int. J. Polymer
Analysis & Characterization, 1, 201-215 (1995).
CFDintheCapillaryRheometryofPolyethyleneMelts
295