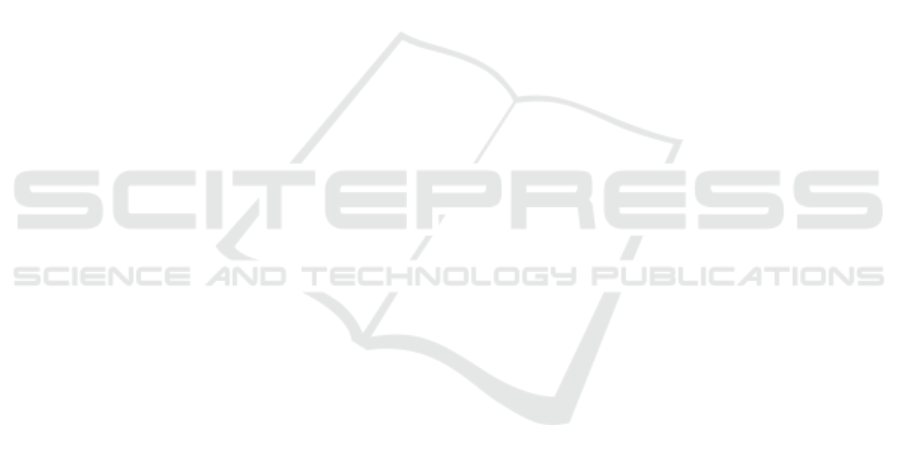
Developing A New Variables Sampling Scheme for Product
Acceptance Determination
Chien-Wei Wu
1
and James C. Chen
2
1
Department of Industrial Management, National Taiwan University of Science and Technology, Taipei, Taiwan
2
Department of Industrial Engineering and Engineering Management, National Tsing Hua University, Hsinchu, Taiwan
Keywords: Decision Making, Acceptance Sampling, Fraction of Defectives, Quality Assurance.
Abstract: Acceptance sampling is a useful tool for determining whether submitted lots should be accepted or rejected.
With the current increase in outsourcing production processes and the high quality levels required, it is very
desirable to have an efficient and economic sampling scheme. This paper develops a variables repetitive
group sampling (RGS) plan based on the third generation of process capability index. The plan parameters
are determined by minimizing the average sample number (ASN) for inspection and fulfilling the classical
two-point-condition on the operating characteristic (OC) curve. Besides, the efficiency of the proposed plan
is investigated and compared with the existing variables single sampling plan. Tables of the plan parameters
are also provided.
1 INTRODUCTION
Acceptance sampling is one of the most practical
tools in classical quality control and assurance
applications, which deal with quality contracts for
product orders between factories and their
customers. Acceptance sampling plans provide the
producer and the consumer with a general criterion
for lot sentencing. A well-designed sampling plan
can substantially reduce the difference between the
required and the actual supplied product quality
(Pearn and Wu, 2006; Pearn and Wu, 2007).
Unfortunately, it cannot avoid the risk of accepting
unwanted poor product lots, nor can it avoid the risk
of rejecting good product lots without implementing
100% inspection (e.g., Montgomery, D. C., 2009).
The criteria used to measure the performance in an
acceptance sampling plan are usually based on the
operating characteristic (OC) curve, which
quantifies the risks of producers and consumers. The
OC curve plots the probability of accepting a lot
against the actual quality level of the submitted lots.
In other words, the OC curve shows the
discriminatory power of the sampling plan, which
provides the producer and the buyer with a common
base for judging whether the sampling plan is
appropriate.
Sherman (1965) developed a new type of
sampling plan, called the repetitive group sampling
(RGS) plan, for attributes. The operating procedure
of this RGS plan is similar to that of the sequential
sampling plan. Balamurali and Jun (2006) extended
the RGS concept to variables inspection for a
normally distributed quality characteristic. They also
compared the efficiency of the variables RGS plan
with the variables single and double sampling plans.
These results indicate that the variables RGS plan
give the desired protection with the minimum
average sample number (ASN).
It is highly desirable to have an efficient and
economic acceptance sampling scheme, especially
when the required quality level is very high.
Therefore, the main purpose of this paper is to
develop a new variables sampling scheme for
product acceptance determination.
2 PROCESS CAPABILITY
INDICES
Process capability indices (PCIs), including C
p
, C
pk
,
C
pm
and C
pmk
, are convenient and powerful tools for
measuring process performance from different
perspectives. These indices establish the relationship
between actual performance and the specification
limits, and convey critical information regarding
whether a process is capable of reproducing items
satisfying customer requirements. For thorough
589
Wu C. and Chen J..
Developing A New Variables Sampling Scheme for Product Acceptance Determination.
DOI: 10.5220/0003972505890593
In Proceedings of the 9th International Conference on Informatics in Control, Automation and Robotics (OMDM-2012), pages 589-593
ISBN: 978-989-8565-22-8
Copyright
c
2012 SCITEPRESS (Science and Technology Publications, Lda.)