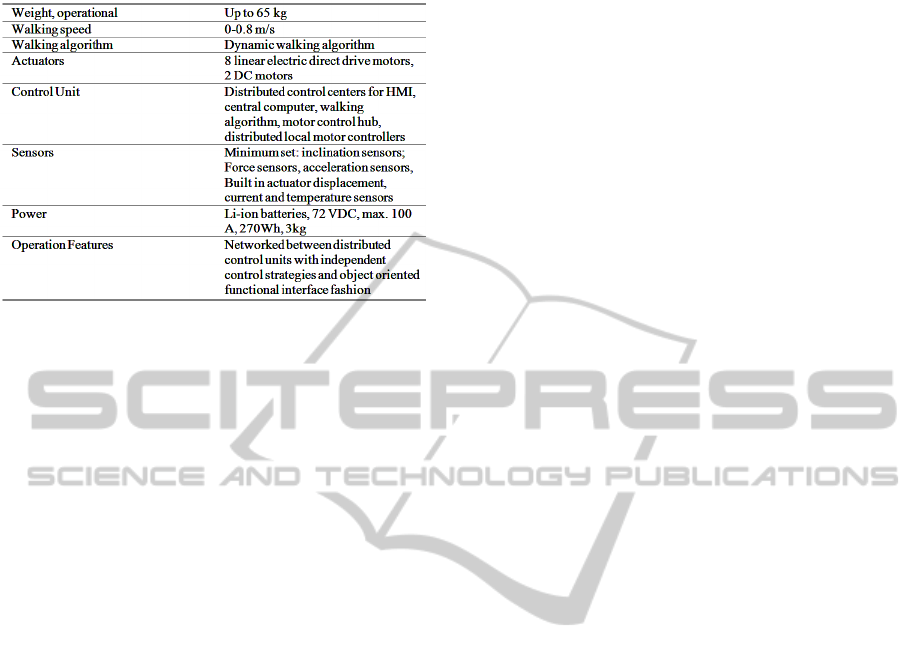
Table 2: The SWAY specification.
length of walking sequence. Further work may
employ different brand or custom made linear
electric direct drive motors.
7 CONCLUSIONS
We have proposed and developed a biped robot
which key aspects are the anthropomorphism and the
use of linear electric direct drive actuation. The
robot bears comparable anthropomorphic geometric
and mass values to serve further studies and
experiments for dynamical walking. Its control
structure follows modularity principles with its
components functionally distributed but each are
completely integrated. The proposed robot design’s
incremental testing and justification is underway and
reached the stage of its complete but preliminary
postural balance control. The biped’s motion is
smooth and silent. Further work shall address the
control algorithms which capable to exploit the
kinematical advantages of the proposed mechanism.
REFERENCES
Akachi, K., Kaneko, K., Kanehira, N., Ota, S., Miyamori,
G., Hirata, M., Kajita, S., Kanehiro, F., 2005.
Development of humanoid robot HRP-3P. 5th IEEE-
RAS International Conference on Humanoid Robots,
vol. 5(5), pp. 50 – 55.
Delude, C. M., 2005. MIT closes in on bionic speed.
Available online at http://web.mit.edu/newsoffice/
2005/muscle.html.
Geyer, H., 2011, What breakthroughs does the field of
legged dynamics need? Dynamic Walking 2011.
Geyer, H., Seyfarth A., Blickhan R., 2006, Compliant leg
behaviour explains basic dynamics of walking and
running. Proc R Soc B 273: 2861–2867.
Hirose, M., Ogawa, K., 2007. Honda humanoid robots
development, Phil. Trans. R. Soc. A 2007 365, 11-19.
Honda, Online,
http://world.honda.com/ASIMO/history/technology3.h
tml, Available 1.2.2012.
LinMot, Online, Data Book: Industrial Linear Motors,
(Edition 15). Available: http://www.linmot.com/
Lim, H., Takanishi, A., 2007, Biped walking robots
created at Waseda University: WL and WABIAN
family. Phil. Trans. R. Soc. A 2007 365, 49-64.
Hurst, J., W., J. Chestnutt, E., Rizzi, A., A., 2007. Design
and Philosophy of the BiMASC, a Highly Dynamic
Biped. 2007 IEEE International Conference on
Robotics and Automation, vol. 10(14), pp. 1863 –
1868.
National Research Council, 2008. Soldier Protective
Clothing and Equipment. The National Academic
Press. (Design Challenge: Robotic Capability for
PETMAN).
Muscato, G., Spampinato, G., 2005. A Multi Level
Control Architecture for a Pneumatic Robotic Leg.
ETFA2005 10th IEEE International Conference on
Emerging Technologies and Factory Automation,
Catania, Italy, 19-22 September 2005.
MYOROBOTICS, A framework for musculoskeletal
robot development. 7th Seventh Framework
programme, European Communities.
Osuka, K., Sugimoto, Y., 2005, Where is the Secret of
Walking Concealed? IEEE Int’l Conf. on Robotics and
Biomimetics. pp. 788-792.
Peralta, J., Ylikorpi, T., Gulzar, K., Jakubik, P., and
Halme, A.,2009, Novel Design of Biped Robot Based
on Linear Induction Motors. in Proc. International
Conference on Humanoid Robots.
Robinson, D., W., Pratt, J., E., Paluska, D., J., Pratt, G.,
A., 1999. Series Elastic Actuator Development for a
Biomimetic Walking Robot. International Conference
on Advanced Intelligent Mechatronics, September 19-
23, 1999 Atlanta, USA.
Sardain, P., Rostami, M., Bessonnet, G,, 1998, An
Antropomorphic Biped Robot: Dynamic Concept and
Technological Design. IEEE Tr. On SMC, Part A, Vol.
28, No. 6.
Vukobratović, M., Borovac, B., 2004. Zero-moment
point—Thirty five years of its life. International
Journal of Humanoid Robotics, Vol. 1, No. 1.
Vukobratović, M., Borovac, B., 2009. Why Should
Robots in Unstructured Environments Perform a
Dynamically Balanced Regular Gait? Acta
Polytechnica Hungarica vol. 6(1).
ICINCO2012-9thInternationalConferenceonInformaticsinControl,AutomationandRobotics
176