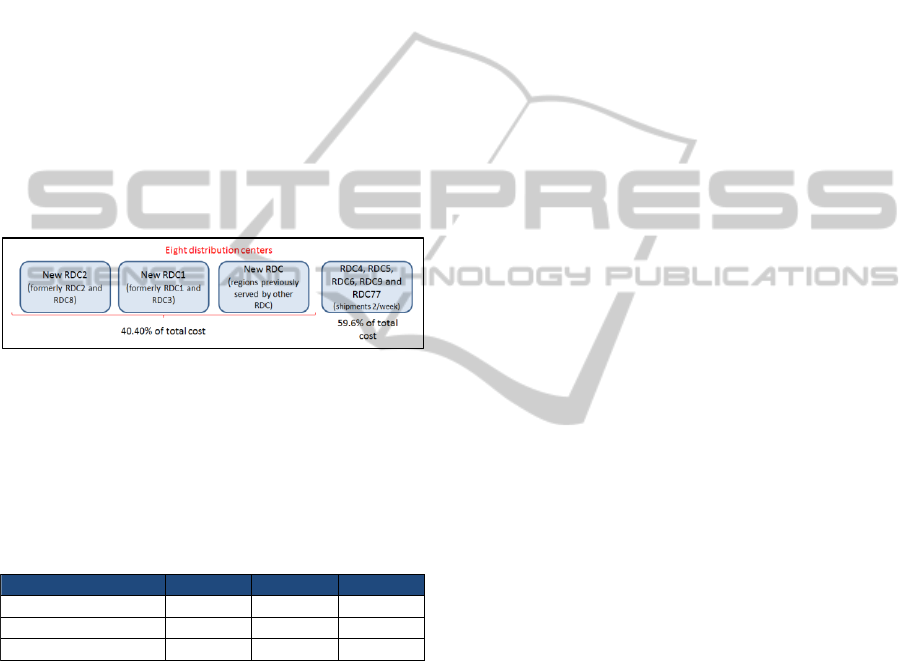
Considering this differences and a target error of
5%, results from simulation model is within
tolerances.
4.2 Improvement Case
The model was used to analyze some alternatives to
improve the distribution network, including:
Opening/Closing/Merging of RDC.
Reassignment of regions to RDC.
Adding delivery frequencies.
Using multiechelon inventories.
About twenty scenarios were simulated and the
model only required adding a small code to manage
the multiechelon inventory and the additional
delivery frequencies. A new distribution network
was found, composed by eight RDC, using
multiechelon inventories and serving twice-per week
to the metro areas, as shown in Figure 6:
Figure 6: Configuration of proposed distribution network
after simulation analysis.
Considering the actual distribution network as
100%, there are significant savings, as shown in
table 1:
Table 1: Comparison of key performance indicators of
base case versus proposed network.
The final savings of 19.3% of the total costs is
important for the company; this savings can be used
to reinforce the competitive position of the firm.
5 CONCLUSIONS
The proposed model, based on a two-echelon system
that can be replicated both forwards and backwards,
has been tested and used in a real situation to
improve a distribution network; its operation has
been fast, and helped to focus on the most important
characteristics of the model.
Finally, it is really critical to consider that any
simulation model, specially a strategic one, must be
designed to support a company to comply with its
strategy. This model must fit within the “reducing
cost” strategy to improve service to the bottom of
pyramid clients.
REFERENCES
Brown, N. and Powers, S. 2000. “Simulation in a box (a
generic reusable maintenance model)” Proceedings of
the 2000 Winter Simulation Conference, Edited by J.
A. Joines, R. R. Barton, K. Kang, and P. A. Fishwick,
1050-1056. Piscataway, New Jersey: Institute of
Electrical and Electronics Engineers, Inc.
Buxton, K., Fuqua, B. y Wyland, B. 2000. “Simulating the
supply chain”. IIE Solutions, 32(1):37-42
Chang, Y. y Makatsoris, H. 2001. “Supply chain modeling
using simulation”. International journal of simulation
systems, science and technology, 2(1):24-30
Cope, D., Sam-Fayez, M., Mollaghasemi, M. And
Kaylani, A. 2007. “Supply chain simulation modeling
made easy: an innovative approach”. Proceedings of
the 2007 winter simulation conference, Edited by S. G.
Henderson, B. Biller, M.-H. Hsieh, J. Shortle, J. D.
Tew, and R. R. Barton, 1887-1896
Hung, W Y., Kucherenko, S., Samsatli, N. y Shah, N.
2004. “A flexible and generic approach to dynamic
modelling of supply chain”. Journal of the operational
research society, 55:801-813
Longo, F., and Mirabelli, G. 2008. “An advanced supply
chain management tool based on modeling and
simulation.” Computers & Industrial Engineering,
54:570-588.
Petrovic, D., Roy, R., y Petrovic, R. 1998. “Modelling and
simulation of a supply chain in an uncertain
environment”. European journal of operational
research, 109:299-309
Porter, M. (1996). “What is strategy?” Harvard Business
Review, 74(6):61-78.
Pundoor, G. And Herrmann, J. 2006. “A hierarchical
approach to supply chain simulation modeling using
the supply chain operations reference model”.
International journal of simulation and process
modelling. 2(3-4): 124-132.
Shanthikumar, J. y Gargent, R. 1983. “A unifying view of
hybrid simulation/analitic models and modeling”.
Operations research, 31(6):1030-1052
Indicator Actual Proposed Savings
Inventory (pieces.) 100% 50.1% 49.9%
Transportation cost $$$ 100% 98.6% 1.4%
Total cost $$$ 100% 80.7% 19.3%
SIMULTECH 2012 - 2nd International Conference on Simulation and Modeling Methodologies, Technologies and
Applications
448