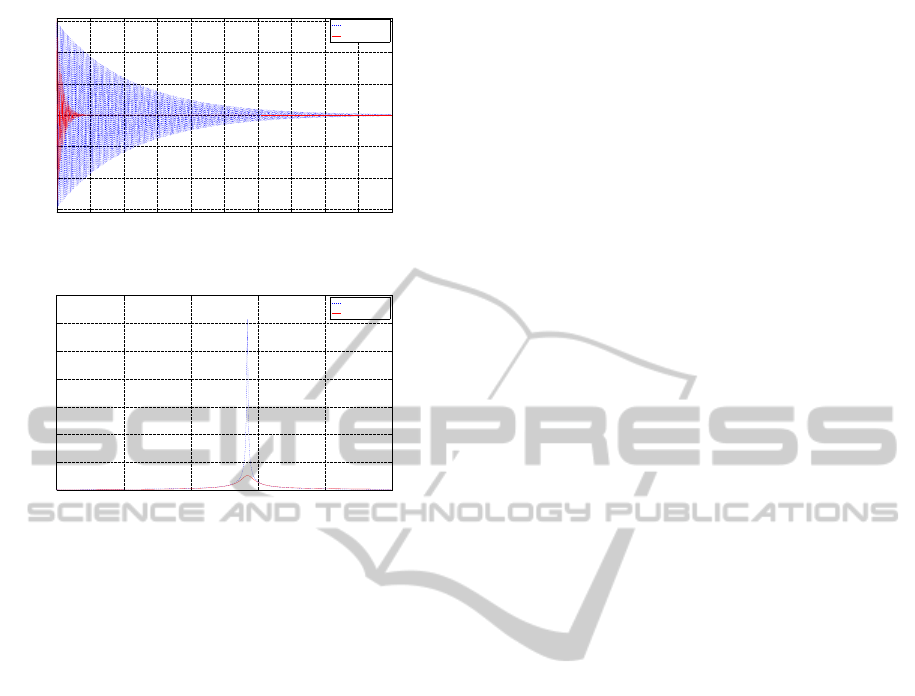
20 22 24 26 28 30 32 34 36 38 40
−0.03
−0.02
−0.01
0
0.01
0.02
0.03
Time, (s)
Tip displacement, (m)
No control
SRF control
Figure 9: Tip displacement vs. time with the SRF controller.
0 5 10 15 20 25
0
0.01
0.02
0.03
0.04
0.05
0.06
0.07
Frequency (Hz)
Magnitude (mm)
No control
SRF control
Figure 10: The FFT spectrum of the smart beam.
will be controlled, and other control strategies (e.g.
positive position feedback, PID controllers...etc) will
be investigated and implemented.
REFERENCES
Adhikari, S. (2000). Damping Models for Structural Vibra-
tions. PhD thesis, Cambridge University.
Bailey, T. (1984). Distributed-parameter vibration con-
trol of a cantilever beam using a distributed-parameter
actuator. Master’s thesis, Massachusetts Institute of
Technology.
Bailey, T. and Hubbard, J. (1985). Distributed piezoelectric-
polymer active vibration control of a cantilever beam.
AIAA Journal of Guidance and Control, 6:605–611.
Balas, M. (1978). Active control of flexible systems. Jour-
nal of Optimization Theory and Applications, 25:415–
436.
Chowdhury, I. and Dasgupta, S. (2003). Computation of
rayleigh damping coefficients for large systems.
Craig, R. and Bampton, M. (1968). Coupling of substruc-
tures for dynamic analysis. AIAA Journal, 6:1313–
1319.
Crawley, E. and Anderson, E. (1990). Detailed models of
piezoceramic actuation of beams. Journal of Intelli-
gent Material Systems and Structures, 1:4–24.
Crawley, E. and de Luis, J. (1987). Use of piezoelectric
actuators as elements of intelligent structures. AIAA
Journal, 25:1373–1385.
Fanson, J. and Chen, J., editors (1986). Structural Control
by the use of Piezoelectric Active Members, volume 2
of Proceedings of NASA/DOD Control-Structures In-
teraction Conference. NASA. CP-2447.
Fei, J. and Fang, Y., editors (2006). Active Feedback Vibra-
tion Suppression of a Flexible Steel Cantilever Beam
Using Smart Materials. Proceedings of the First Inter-
national Conference on Innovative Computing, Infor-
mation and Control (ICICIC’06).
Ghareeb, N. and Radovcic, Y. (2009). Fatigue analysis of a
wind turbine power train. DEWI Magazin, 35:12–16.
He, J. and Fu, Z. (2001). Modal Analysis. Butterworth-
Heinemann.
Hort, H. (1934). Beschreibung und versuchsergebnisse aus-
gefhrter schiffsstabilisierungsanlagen. Jahrb. Schiff-
bautechnik Ges., 35:292–312.
Khalil, H. (1996). Nonlinear Systems. Prentice Hall, Madi-
son.
Ko, W. and Olona, T. (1987). Effect of element size on the
solution accuracies of finite-element heat transfer and
thermal stress analysis of space shuttle orbiter. Tech-
nical Memorandum 88292, NASA.
Lee, J. B. J. and Davidson, B. (2004). Experimental deter-
mination of modal damping from full scale testing. In
13th World Conference on Earthquake Engineering,
number 310, Vancouver, Canada.
Mallock, A. (1905). A method of preventing vibration in
certain classes of steamships. Teans. Inst. Naval Ar-
chitects, 47:227–230.
Narayanan, S. and Balamurugan, V. (2003). Finite element
modelling of piezolaminated smart structures for ac-
tive vibration control with distributed sensors and ac-
tuators. Journal of Sound and Vibration, 262:529–
562.
Newman, S. (1992). Active damping control of a flexible
space structure using piezoelectric sensors and actua-
tors. Master’s thesis, U.S. Naval Postgraduate School,
California.
Petyt, M. (2003). Introduction to Finite Element Vibration
Analysis. Cambridge University Press.
Preumont, A. (2002). Vibration Control of Active Struc-
tures, An Introduction. Kluwer Academic Publishers.
Rayleigh, L. (1877). Theory of Sound, volume 1, 2. Dover
Publications, New York.
Rickelt-Rolf, C. (2009). Modellreduktion und Substruk-
turtechnik zur effizienten Simulation dynamischer
teilgesch¨adigter Systeme. PhD thesis, TU Carolo-
Wilhelmina zu Braunschweig, Germany.
Spears, R. and Jensen, S., editors (2009). Approach
for Selection of Rayleigh Damping Parameters Used
for Time History Analysis, Proceedings of PVP2009,
ASME Vessels and Piping Division Conference,
Prague, Czech Republic.
ModelingandActiveVibrationControlofaSmartStructure
147