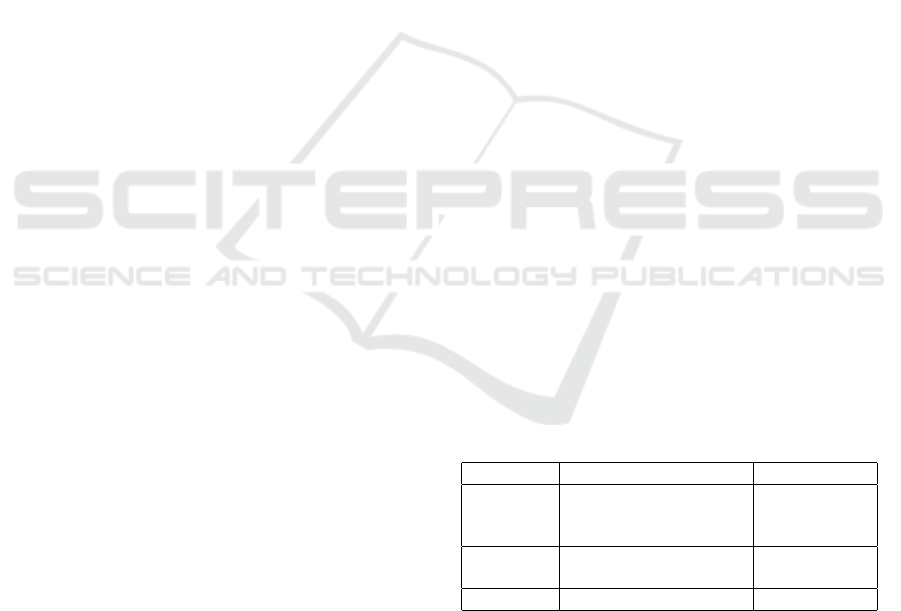
Modeling and Simulation of Humanoid Robot Spine Vertebra
M. Souissi, V. Hugel and P. Blazevic
Université de Versailles Saint Quentin en Yvelines, Versailles, Île-de-France, France
Keywords:
ROMEO Robot, Simulation, Vertebral Column, Mechanical Structure, Kinematics.
Abstract:
In this paper, a parallel mechanism is proposed for the design of humanoid vertebra. This mechanism is
inspired by a flight simulator system, and has been adapted and optimized to enable pitch and roll motion
of a humanoid trunk at reduced energy cost. The system consists of a bottom platform and a top platform
connected by two articulated arms and a vertical central rod. A 3D model of the system has been elaborated
for simulation and design.
1 INTRODUCTION
Robots are expected to live among humans to assist
them in their daily tasks. Current humanoid robots
are not fully suitable for working in our daily environ-
ment. They can do a few limited tasks compared with
what a human can do. Walking humanoids robots
equipped with joints in the trunk are listed in table 1 in
increasing order of spine DOF number starting from
pelvis. All of them feature a yaw joint in the trunk.
The yaw joint is particularly useful for taking larger
strides. It can also be used to compensate for yaw
moment between feet and ground. It allows the robot
to increase the working volume of its upper body for
manipulation. Existing humanoids that have a yaw
joint in the trunk are Asimo presented by (Sakagami
et al, 2002), KHR2, Hubo in (Kim, 2005), Johnnie
analysed by (Loffler et al, 2005), and Lola (Lohmeier
et al, 2006). An additional pitch joint in the trunk
extends the skills of the robot. The pitch joint is help-
ful for the robot to sit down on a chair. Examples of
robots that can sit down are the series of REEM-A/B
presented in (Tellez, 2008). This robot is manufac-
tured by Pal Technology Robotics. Humanoids with
a pitch joint in the trunk can also stand up from lying
position. The HRP2 robot demonstrated its capacity
to lie on the ground and to stand up again using its
pitch joint in the trunk (Kaneko, 2008). Roll joints
can be added to enhance locomotion capacities. That
is the case of the last generation of Wabian robots de-
veloped by Waseda University in Japan (Ogura et al,
2006). Wabian II features two additional roll joints –
one in the middle of the pelvis and the other one at
the end of the trunk kinematic chain – that were in-
troduced to implement new locomotion skills. This
robot is capable of stretching the knee during walk
when the supporting leg comes below the hip. Pitch
and roll joints also increase the working space of the
upper body and they can be used to bend the trunk
forward and /or sideways to grasp something or to re-
sist some perturbation at shoulder level. The DOF in
Table 1: Walking humanoid robots with DOF in the trunk.
DOF type of DOF Prototypes
1 yaw KHR2, Hubo,
Johnnie,
Asimo
2 yaw +pitch HRP-2-3-4,
Reem A/B
4 roll + yaw + pitch + roll Wabian II
the trunk are therefore task-dependent. It is interest-
ing for humanoids to have a vertebral column to deal
with both movement and manipulation skills.
The contribution of this paper consists of adapt-
ing an existing parallel mechanism of flight simulator,
found in thses of (Emilie, 2004), to the design of a
pitch-roll vertebra joint, taking into account the spec-
ifications of forward, backward and left/right side-
ways bending amplitudes given for a humanoid robot.
The objective of the study is to optimize the different
length ratios of the mechanism in order to have a re-
duced torque required for the bending motions.
Section II deals with the description of the paral-
lel mechanism. Section III presents simulation and
results. Section IV is devoted to conclusion and per-
spectives.
415
Souissi M., Hugel V. and Blazevic P..
Modeling and Simulation of Humanoid Robot Spine Vertebra.
DOI: 10.5220/0004013904150418
In Proceedings of the 9th International Conference on Informatics in Control, Automation and Robotics (ICINCO-2012), pages 415-418
ISBN: 978-989-8565-22-8
Copyright
c
2012 SCITEPRESS (Science and Technology Publications, Lda.)