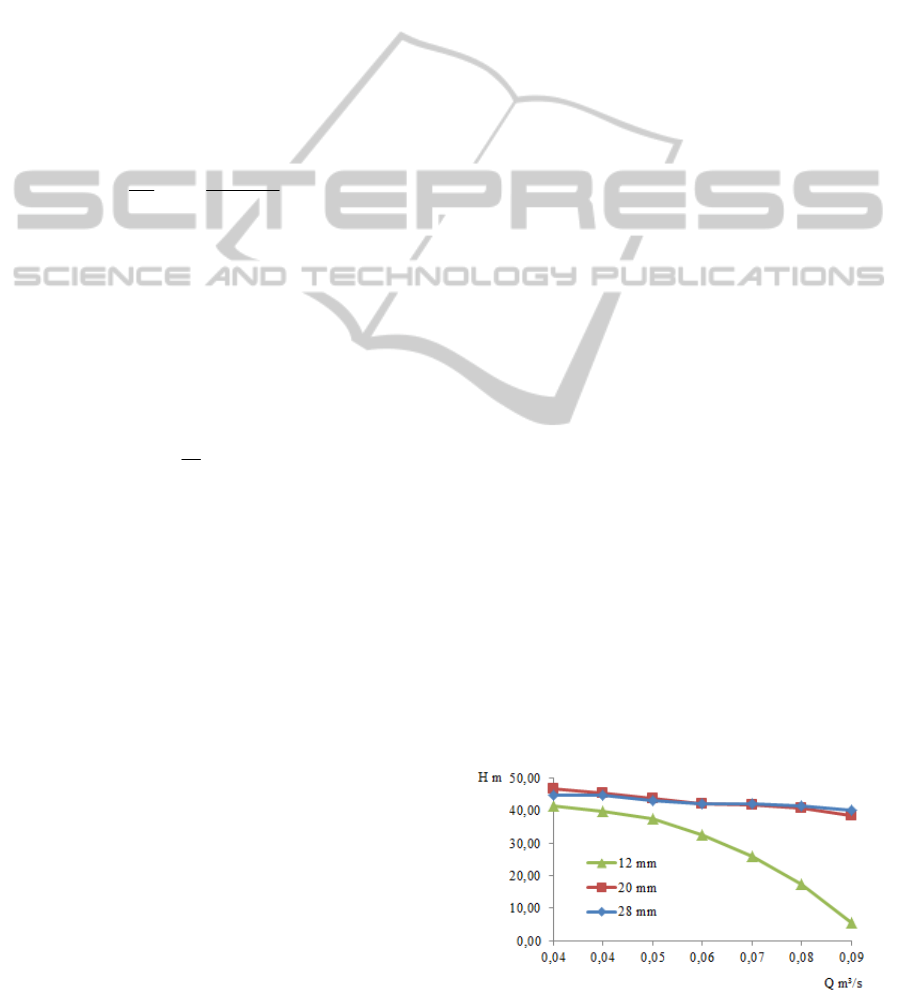
velocity vector, p is the pressure, ρ is the density
(997 kg/m³), μ
eff
is the effective viscosity accounting
for turbulence, ⊗ is a tensor product and B is the
source term. More particularly, for flows in an
impeller rotating at a constant speed ω, the source
term can be written as follows:
()
rxxUx2B
ωω+ωρ−=
(3)
where
r
is the location vector.
In addition, μ
eff
is defined as:
teff
μ+μ=μ
(4)
where μ is the dynamic viscosity (8.899 x 10
-4
Pas)
and μ
t
is the turbulence viscosity (Ansys inc., 2008).
The actual pump head rise is given by:
⎟
⎟
⎠
⎞
⎜
⎜
⎝
⎛
β
−
⎟
⎟
⎠
⎞
⎜
⎜
⎝
⎛
μη=
2b2
2
2
sh
tanA
Q
U
g
U
H
(5)
where η
h
is the hydraulic efficiency, μ
s
is the slip
factor (Peng, 2008), U
2
is the outlet tangential
velocity U
2
, β
b2
is the outlet blade angles and Q is
the volume flow rate. It is given by Q = V
r2
A
2
with
A
2
as the outlet flow passage area normal to the
meridional direction.
The overall efficiency of a centrifugal pump can be
formulated as:
s
h
P
P
=η
(6)
where P
h
is the centrifugal pump horsepower. It is
expressed as
QgHP
h
ρ=
and P
s
is the pump brake
horsepower (Peng, 2008).
To solve Eqs. 1 and 2 numerically while accounting
for the boundary conditions and the turbulence
model k-ε, the ANSYS-CFX code, based on the
finite volume method, was used to obtain the liquid
flow velocity and the pressure distributions.
3 RESULTS AND DISCUSSION
The main data for the reference impeller were: inlet
diameter = 145 mm; outlet diameter = 320 mm; inlet
blade angle = 11.69 °; outlet blade angle = 28°; inlet
blade width = 12 mm; blade thickness = 4 mm;
number of blades = 7; and rotating speed = 1800 rpm.
For the reference diffuser, the main data were:
inlet diameter = 320 mm; outlet diameter = 455 mm;
blade width = 12 mm; blade thickness = 3.401 mm;
inlet blade angle = 11.07°; outlet blade angle =
39.42 °; number of blades = 9.
Concerning the size of the volute, it was
characterized by the volute angle as a function of the
volute radius (255.17 mm for 0° and 350.35 mm for
360°).
For highest accuracy of numerical simulation
results, the convergence criteria based on a RMS
(Root Mean Square) residual value of 10
-4
was used
and mesh-independent solution tests were conducted
in each case study by finding the number of mesh
elements to achieve mesh-independent results.
3.1 Effect of Blade Height
To investigate the impeller and diffuser blade
height’s effect on the pump performance, the blade
heights of 0.012 m, 0.020 m and 0.028 m were
selected, while the other parameters were keep
constant. Fig. 2 shows the pump head as a function
of the volume flow rate with the outlet blade height
as a parameter. There, it is observed that the pump
head increases with increasing blade height until a
certain value of the blade height. This can be
explained by the fact that when the volume flow rate
is kept constant, the increased outlet blade height
leads to the decreasing meridional velocity, which
increases the pump head since the outlet tangential
velocity and the outlet blade angle remain constant.
But when the meridional velocity becomes too small
or zero with increasing blade height, its influence to
the pump head is negligible.
The curves expressing the pump brake
horsepower as a function of the volume flow rate are
shown in Fig. 3, illustrating that the brake
horsepower increases relative to the increased blade
height due to the requested increase in pump shaft
torque relative to the increased blade height.
Moreover, Fig. 4 shows the overall efficiency
curves as a function of the volume flow rate. It can
be seen that the overall efficiency for b
2
= 12 mm
decreases rapidly to the right of the best efficiency
point (BEP). The overall efficiency curves for b
2
=
20 mm and 28 mm increase with increasing volume
flow rate.
Figure 2: Pump head versus volume flow rate.
SIMULTECH2012-2ndInternationalConferenceonSimulationandModelingMethodologies,Technologiesand
Applications
344