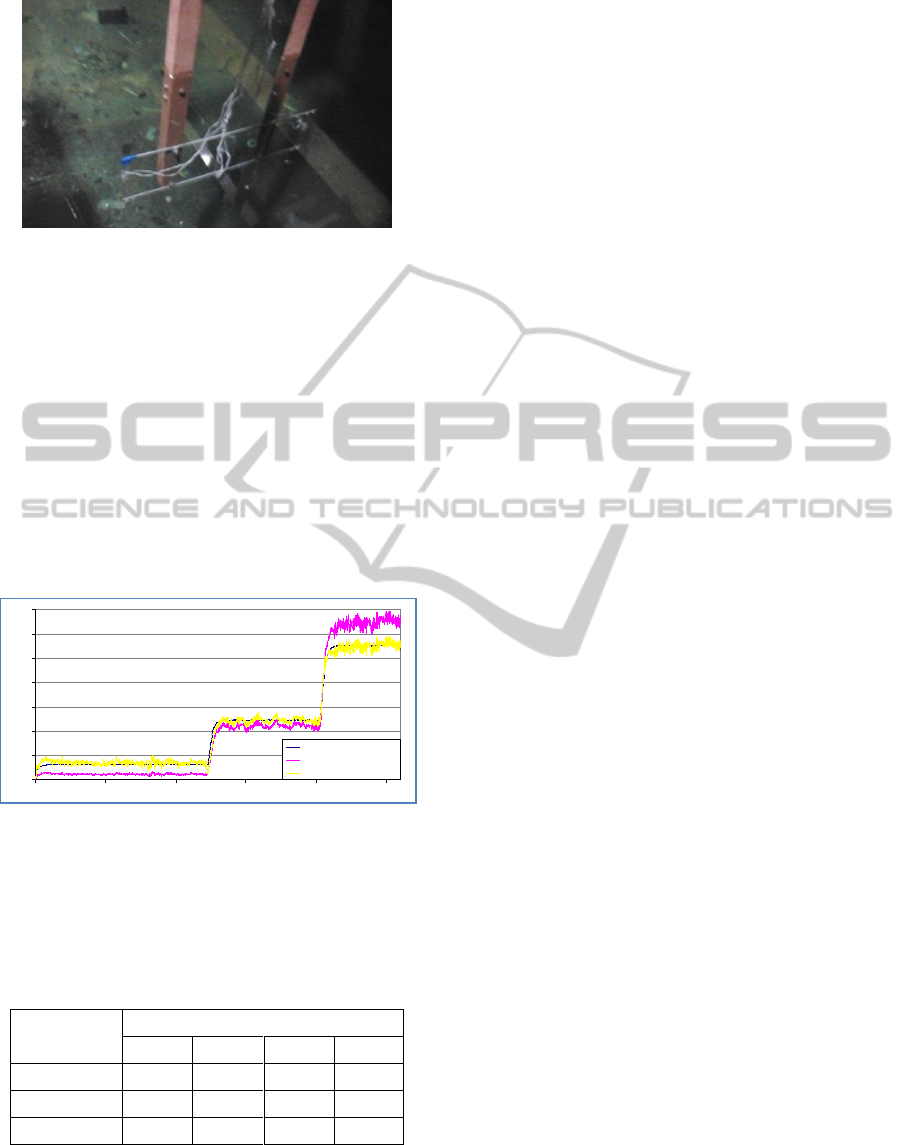
Figure 8: Test Setup – Three Sensor Beams.
6 RESULTS AND DISCUSSION
The experiments were carried out by varying the
speed of towing trolley from 0 knot to 1 knot with
the step increase of 0.5 knot (0.25 m/s).
The result for one of the tests is shown in Figure
9, which shows the comparison of theoretical strain
and the measured strain on the 50 mm width beam
(the graphs in this section are plotted based on the
data points, however, one can easily identify the
speed increase from 0.5 knot to 1 knot and then to
1.5 knots from the graphs).
Figure 9: Results_50 mm Sensor Beam 1.
As the measured strain has constant offset from
actual, we propose to use correction factors as listed
in table 1 to use while using the output of sensor
beam for control of the EUWV.
Table 1: Correction Factors of Sensor Beams.
Using the conventional relationship of force and
strain, the disturbing current velocity is derived
using the strain measured from the sensor beams.
7 CONCLUSIONS
Development of a disturbance velocity measurement
setup using strain gauges is presented in this paper.
Feed forward control strategy and simulation study
showing performance of the proposed control
scheme are presented. Study on the performance of
developed sensor setup of varying thickness and
width has been carried out. Acrylic sensor beam
having 2 mm thickness is selected to use for
implementation and experimental validation of
proposed control scheme. Derived correction factors
for the sensor beams will be used during further
experiments. This method of disturbance force
measurements can be effectively used for station
keeping control of AUVs.
REFERENCES
André Schäfer, Dr.-Ing, 2004, Force, Strain and Pressure
transducers based on foil type strain gauges, HBM
GmbH, Darmstadt, Germany.
Antonelli G., Chiaverini S., Sarkar N. & West M., 2001,
Adaptive control of an autonomous underwater
vehicle: experimental results on ODIN, In
Transactions on Control Systems Technology, IEEE,
Sep 2001.
Blevins, Robert D., 2003, Applied Fluid Dynamics
Handbook. Krieger Publishing Co.
Eric Conrado De Souza, Newton Maruyama, 2007,
Intelligent UUVs: Some Issues on ROV Dynamic
Positioning, In IEEE Transactions on Aerospace and
Electronic Systems.
Eric R. Johnson and William J. Devenport, 2007, Static
Response of a Beam, in experimental manual.
Hoffmann K., 1889, An introduction to measurements
using strain gauges, Hottinger Baldwin Messtechnik
Publisher.
Krut’ko. P. D., 1989, Inverse problems of control system
dynamics: nonlinear models, Nauka Phys. & Math
Publisher, Moscow.
McLain T. W., Rocky S. M., 1992, Experimental
Measurement of ROV Tether Tension, In Proceedings
of ROV, San Diego, CA.
Thomas Kleckers, 2004, Important characteristics of force
transducers, HBM GmbH, Darmstadt, Germany
William A. Lokos, Rick Stauf, 2004, Strain-Gauge Loads
Calibration Parametric Study, In Technical Report of
NASA Centre for Aero Space Information (CASI).
Woods A. J., Penrose J. D., Duncan A. J., Koch R., Clark
D., 1998, Improving the Operability of Remotely
Operated Vehicles, In Appea Journal, pp 849 – 854.
Strain_50 mm Sensor Beam 1
0
200
400
600
800
1000
1200
1400
0 500 1000 1500 2000 2500
50_SB1_Theory
50_SB1_Experiment
50_SB1_Exp. With CF
A Novel Approach to Measure under Water Vehicle Disturbance Force for Station Keeping Control
463