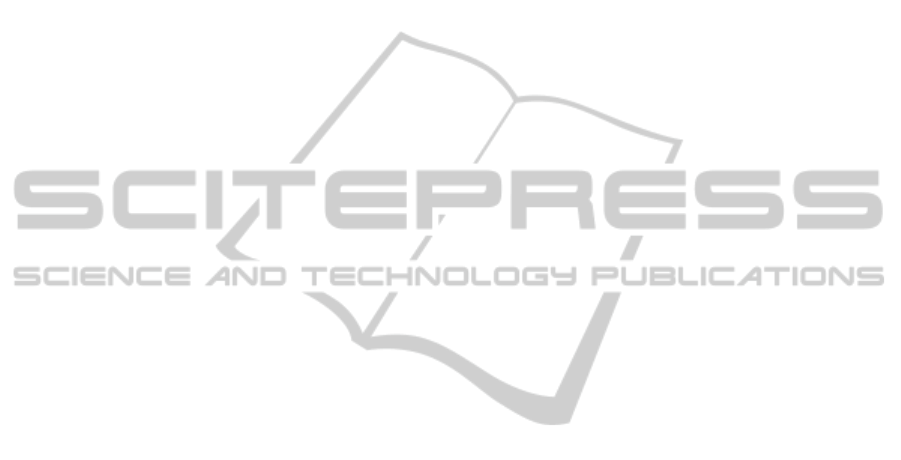
software. In total, this change of layout
configuration had completely vacated the third flow,
hence, opened a 16,00 square feet space to offer as
potential rental income, eliminated more or less
$50,000 of manufacturing operation expenses,
moved 50 pieces of fabricating machinery, moved
three 5-Axis CNC machines, and created an
improved material flow, cycle/delivery times, and
manufacturing work environment. The move was
performed under the leadership and coordination of
one of the authors with minor disruptions of
operations, no loss of production time and no
interruption of employee work efforts. Table 4
shows what area originally existed on the third floor
and how much area was actually needed on the
second floor.
Before the new configuration the shop was
crowded and darker. Pictures taken before and after
change of layout, although not allowed to be
reproduced in this paper, are available with special
permission of WCVFC Inc. Now, the second floor is
brighter and better air flow is available because this
floor has an air exchange system that was not
available on the third floor. In addition, material
flow is in the west to east direction.
The lighting on the second floor is improved
over that on the third floor which was not painted
and occasioning the light to be more absorbed in the
room. The window wall is on the west side of the
building. The elevator and shipping doors are in the
east side. Additionally, work flows were altered to
minimize conflicting movement patterns and make
material flow one way without conflicts.
Arranging CNC machines in such a manner that
accommodated one operator to run two CNC
machines or one CNC and other work bench
routines simultaneously has reduced operator idle
time during machine cycle time, thus, eliminating
non value added operator downtime. In the new
configuration a single operator is able to run two
machines located next to each other when prior to
the move machines were located on two different
floors forcing the need of one operator for each
machine.
Finally, to capture the significance of the savings
generated by the change in layout from the three-
floor operations to a two-floor organization, two
products were particularly tracked through their
entire process before and after implementation of the
lean changes and elimination of some non-value
adding activities. A time process map showing
different steps in these product processes is depicted
in Figure 1 above. An analysis of the diagram
reveals an improvement in cycle time and machine
use. In this illustration, the string of white boxes
shows the current process and the gray and yellow
boxes show the future process. The future process
map shows a saving of 4.8 days per year for the two
products. Considering that these products represent
only two of 35 to 50 varieties of products which run
across these machines it can be easily seen and
concluded that the potential of duplicating this
saving scenario among other products is very high.
REFERENCES
Al-Mubarak, F., Khumawala, B. M. and Canel, C., 2003.
Focused Cellular Manufacturing: An alternative to
Cellular Manufacturing. International Journal of
Operations & Production Management, 23, 3/4,
ABI/INFORM Global: 277-299.
Balakrishnan, J. and Cheng, C. H., 2005. Dynamic
Cellular Manufacturing Under Multiperiod Planning
Horizon. Journal of Manufacturing Technology
Management, 16, 5/6, ABI/INFORM Global: 516-530.
Cheng, T. C. E. and Podolsky, S., 1996, Just-in-Time
Exercising JIT Practices to Support Pull Production
control in a job shop environment. Journal of
Manufacturing Technology Management, Vol. 16 Iss:
7, pp.765 - 783
Kanan, V. R. and Ghosh, S., 1996. A Virtual cellular
Manufacturing Approach to Batch Production.
Decision Sciences, 27, 3: 519-539.
Ron Bialek, Grace L. Duffy, and John W. Moran, 2009.
The Public Health Quality Improvement Handbook.
Milwaukee, WI: ASQ Quality Press.
Schonberger, R. J., 1986. World Class Manufacturing: The
Lessons of Simplicity Applied. Free Press, New York,
NY.
Shafer, S. M. and Charnes, J. M., 1993. Cellular vs.
Functional Layouts Under a Variety of Shop
Operations. Decision Sciences, 24, 3: 665-682.
Wemmerlov U, Johnson D. J., 1997. Cellular Manufacture
at 46 User Plants: Implementation Experiences and
Performance Improvements. International Journal of
Production Research 35:29-49
ICINCO 2012 - 9th International Conference on Informatics in Control, Automation and Robotics
524