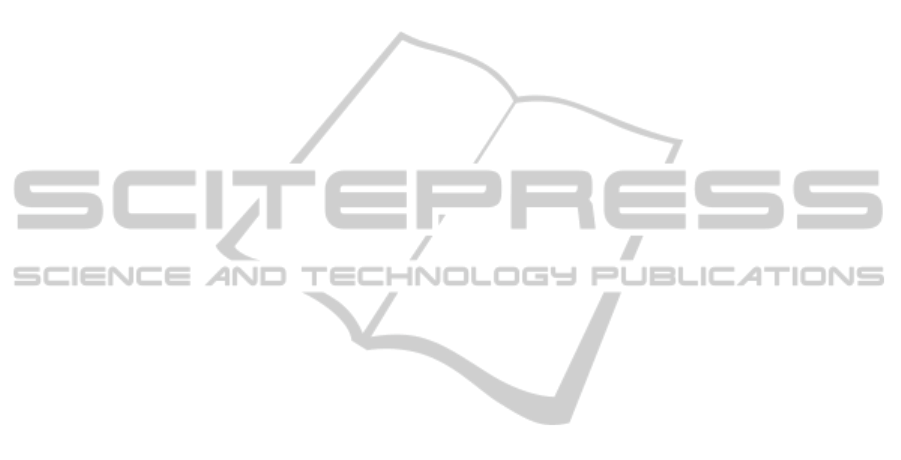
The lessons learned from the paper reflect the
complex and multidimensional characteristics of
manufacturing flexibility. Its achievement
challenges especially industrial organizations to
establish a dynamic decision making based on
comprehensive performance analyses. The issue is
supportable by MES and OpBI, but there is no
unisonous and abstract procedure universally valid
across all manufacturing industries. This sheds an
ambiguous light on flexibility, because of its
presence regarding to the manufacturing itself as
well as for the underlying decision support.
Considering subsequent research actions, the
paper gives an impulse for case specific
implementations and for benchmarking studies of
all-embracing industries. Thereby, the initial
discussion gets enriched by further insights
including comprehensive statistical evaluations with
respect to a particular and a global view on
manufacturing flexibility in context of a dynamic
decision making.
REFERENCES
Alpar, P., Louis, J. P., 2007. Eine empirische
Untersuchung der Softwareunterstützung bei der
Fertigung und Qualitätssteuerung. Philipps-
Universität Marburg.
Barret, J., Barger, R., 2010. Supply Chain Strategy for
Industrial Manufacturers: The Handbook for
Becoming Demand Driven. Retrieved April 16, 2012,
from www.gartner.com/id=1430728.
Beach, R., Muhlemann, A. P., Price, D. H. R., Paterson,
A., Sharp, J. A., 2000. A review of manufacturing
flexibility. European Journal of Operational
Research, 122, 41-57.
Browne, J., Dubois, D., Rathmill, K., Sethi, S. P., Stecke,
E., 1984. Classification of flexible manufacturing
systems. The FMS Magazine, 22, 114–117.
Eckerson, W. W., 2007. Best Practices in Operational BI:
Converging Analytical and Operational Processes.
TDWI Best Practices Report, Renton (WA).
Felden, C., Chamoni P., Linden M., 2010. From Process
Execution towards a Business Process Intelligence. In
Abramowicz, W. and Tolksdorf, R. (Eds.) Business
Information Systems 13th International Conference,
May 3-5, Berlin, Germany, 195-206.
Gebauer, J., Lee, F., 2005. Towards an "Optimal" Level of
Information Systems Flexibility: A Conceptual Model.
In Proceedings of the 13th European Conference on
Information Systems, May 26-28, Regensburg,
Germany.
Gluchowski, P., Kemper, H., Seufert, A., 2009. Innovative
Prozess-Steuerung. BI-Spektrum, 4, 1, 8-12.
Hänel, T., Felden, C., 2011. Limits or Integration?
Manufacturing Execution Systems and Operational
Business Intelligence. In Amercias Conference on
Informations Systems, August 05-07, Detroit, USA.
Hayes, R. H., Wheelwright, S. C., 1984. Restoring our
Competitive Edge: Competing Through
Manufacturing. Wiley, New York.
ISA ANSI/ISA-95.00.01-2000, 2000. Enterprise Control
System Integration, Part 1: Models and Terminology.
ISA technical paper.
ISO 9000, 2005. Quality management systems:
Fundamentals and vocabulary. European Committee
for Standardization, Brussels.
Flick, U., (2006). An introduction to qualitative research.
SAGE Publications, London.
Kletti, J., 2007. Manufacturing Execution Systems.
Springer, Berlin.
Koch, M., Lasi, H., Baars, H., Kemper, H. G., 2010.
Manufacturing Execution Systems and Business
Intelligence for Production Environments. In
Proceedings of the Sixteenth Americas Conference on
Information Systems, August 12-15, Lima, Peru.
KPMG, 2011. Global Manufacturing Outlook: Growth
while Managing Volatility. Retrieved April 16, 2012,
from www.kpmg.com/global/en/issuesandinsights/
articlespublications/global-manufacturing-outlook/
pages/growth-while-managing-volatility.aspx.
Patel, P. C., Terjesen, S., Li, D., 2011. Enhancing effects
of manufacturing flexibility through operational
absorptive capacity and operational ambidexterity,
Journal of Operations Management,
doi:10.1016/j.jom.2011.10.004.
Rodriguez, R.A., 2007. Aligning IT to Business Processes.
Retrieved April 16, 2012, from www.appian.com/
bpm-resources/papers_reports/report_aberdeen1.pdf.
Rogalski, S., 2011. Flexibility Measurement in Production
Systems, Springer, Berlin.
Rolón, M., Martínez, E., 2012. Agent-based modeling and
simulation of an autonomic manufacturing execution
system. Computers in Industry, 63, 53-78.
Saenz de Ugarte, B., Artiba, A., Pellerin, R., 2009.
Manufacturing execution system: a literature review.
Production Planning and Control, 20(6), 525-539.
Schrödl, H., 2006. Business Intelligence. Hanser,
München, Wien.
Upton, D., 1994. The management of manufacturing
flexibility. California Management Review, 36, 72-89.
Vokurka, R. J., O’Leary-Kelly S. W., 2000. A review of
empirical research on manufacturing flexibility.
Journal of Operations Management, 18, 485–501.
White, C., 2006. The Next Generation of Business
Intelligence: Operational BI. Retrieved April 16,
2012, from certification.sybase.com/content/1041416/
Sybase_OperationalBI_WP-071906.pdf.
Yin, R. K., 2009. Case Study Research: Design and
Methods. SAGE, Los Angeles.
Younus, M., Peiyong, C., Hu, L., Yuqing, F., 2010. MES
Development and Significant Applications in
Manufacturing - A Review. In 2nd International
Conference on Education Technology and Computer,
June 22-24, Shanghai, China.
KMIS2012-InternationalConferenceonKnowledgeManagementandInformationSharing
112