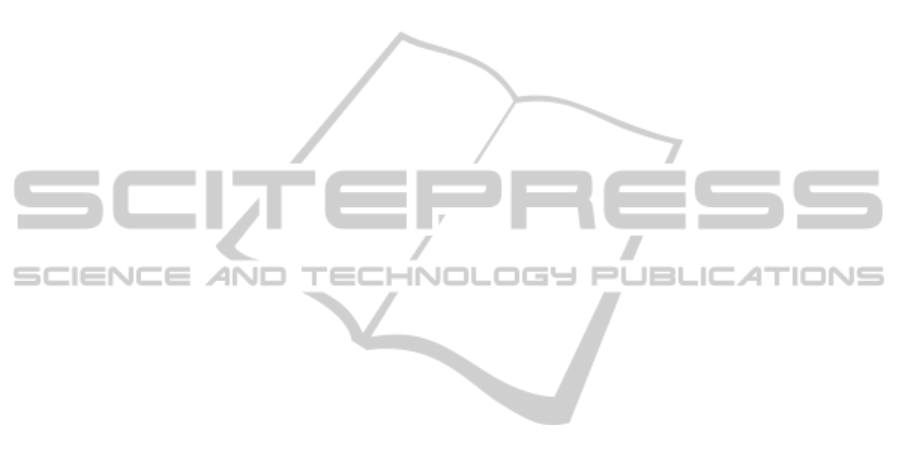
now relies upon a far greater corporate team effort
than in the past.
A significant challenge facing companies is to
facilitate the collaboration of all employees within
geographically dispersed teams in order to meet
common goals while sharing, developing and
retaining knowledge and ideas during on-going PD
processes. The use of collaborative web-based
technologies is seen as providing the potential to
address this challenge by allowing project review
teams to access data, records of knowledge
contributions and social interactions, all of which
would benefit subsequent PD activities (McAdam,
O’Hare and Moffett, 2008).
It has also been suggested that companies must
“create initiatives to dismantle organisational silos
and foster collaboration” (McAdam, O’Hare and
Moffett, 2008). Such initiatives are necessary
because collaboration is dependent upon the
voluntary exercise of discretionary time by
employees (CSC, 2006). Effective enterprise
collaboration may again be facilitated by the
integration of people, processes, information and
knowledge through technologies.
In the past, collaboration would often have taken
place by phone, fax or in face to face meetings, at
significant financial and time costs to organisations.
With the rapid growth in the popularity and use of
the internet today, however, members of PD teams
can now be located thousands of miles apart and still
retain the ability to share and address issues with
minimal loss of time and cost. The World Wide Web
(WWW) can provide an interoperable means for
collaboration, utilising software applications on a
variety of platforms and frameworks.
3 KNOWLEDGE MANAGEMENT
AND WEB 2.0
Businesses recognise that organisational knowledge
has an essential role to play in responding to
competitive pressures and, for an increasing number
of companies, opportunities to establish competitive
advantage lie in their ability to enhance ideas and
intellectual know-how. By making more effective
use of their knowledge assets, organisations can
benefit from product development breakthroughs
and improved processes and practices.
Information and Communication Technology
(ICT) tools and, in particular, the internet have a key
role to play in supporting KM as they can facilitate
“efficient transfer, storage and integration of
knowledge” (Rebolledo and Nollet, 2011, Carlsson,
2003). Their role cannot be ignored as they impact
directly on the quantity, speed and efficiency of data
flow across both geographical and organisational
boundaries (Scott, 2000).
While it is recognised that businesses often
cannot identify what is known within their
organisations and as a result, best practices,
expertise and knowledge and skills cannot easily be
applied and transferred (Lockwood, 2008), digital
technologies offer the prospect of transferring both
tacit as well as explicit knowledge (Rebolledo and
Nollet, 2011); (Carlsson, 2003).
Web 2.0 technologies and the relatively new
phenomenon of social media with its emphasis on
user-generated content, can help eradicate such
barriers encouraging open communication and
information sharing. Expertise and solutions to
problems need no longer remain “hidden” as they
can be actively sought out and exploited within a
Web 2.0 collaborative environment. Web 2.0 tools,
which commonly incorporate semantic web
techniques such as meta-tagging, allow for more
meaningful information sharing and improved
searchability and encourage greater interaction with
content by employees during the collaborative
process.
4 INDUSTRIAL INVESTIGATION
BAE Systems is a multi-national organisation
employing approximately 100,000 people worldwide
across its range of businesses. The organisation is
the second largest aerospace, defence and security
company in the world, and, in 2010, reported sales
of over £22bn ($34.6bn). The organisation is
involved in the design, manufacture and provision of
advanced products and services for worldwide
military forces (BAE Systems, 2011).
An independent bench marking study,
commissioned by BAE Systems in 2008, showed
that practices in relation to learning and knowledge
management were judged to be “average” when
compared to similar types of organisations (Milton,
2008). The study concluded that BAE Systems’ KM
performance, as a world-leading development and
manufacturing enterprise, could be raised to “best in
class” by following forty-nine recommended
actions. The actions identified included the creation
of a common collaborative platform for engineering
and product development across the company and
the embedding of KM activities into various
corporate processes including Performance and
KMIS2012-InternationalConferenceonKnowledgeManagementandInformationSharing
114