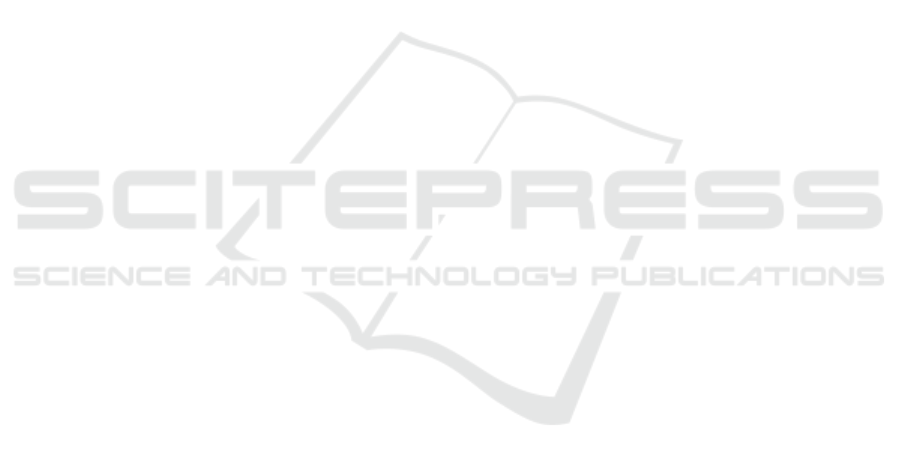
Development of a Wheelchair with a Lifting Function
Yoshikazu Mori
1
, Norikatsu Sakai
2
and Kaoru Katsumura
3
1
Department of Intelligent Systems Engineering, Ibaraki University, Nakanarusawa 4-12-1, Hitachi, 316-8511, Japan
2
SMC Corp., Akihabara UDX15F, 4-14-1, Sotokanda, Chiyoda-ku, 101-0021, Japan
3
Tamron Co., Ltd., 1385 Hasunuma, Minuma-ku, Saitama-city, Saitama 337-8556, Japan
Keywords: Medical and Welfare Assistance, Mechatronics, Design, Disabled Person, Care Lift, Transferring.
Abstract: A wheelchair with a lifting function is designed to assist a caregiver when transferring a wheelchair user not
only indoors but also outdoors. The target user is typically a severely disabled person with disabled upper
and lower limbs, and therefore needs the physical support when using a toilet or transferring from a bed to a
wheelchair and so forth. Both the wheelchair and the lift are driven by their respective motors. The user can
approach above the toilet stool or the bed from the rear because the large driving wheels are located in front
of the body and the seat can be folded. This wheelchair is allowed to travel on public roads because of the
mechanism of folding the frame for lifting. This paper presents the concept design and the experimental
results of a full-sized prototype wheelchair with the lifting function, which confirms the design
effectiveness.
1 INTRODUCTION
Persons with disabilities attributable to the lower
limbs are becoming increasingly numerous
worldwide. In Japan, they number about 3,480,000
(severely disabled persons were about 760,000) in
2006. Most of them use wheelchairs in daily life.
Representative nursing care in daily life entails
basing, evacuating, and feeding. Transfer when
basing, evacuating, and other processes causes back
pain to caregivers. Matsumoto et al. reported that
77% of caregivers and 64% of nurses have back pain
(Matsumoto and Kusunose, 1999). Consequently,
various devices and robots have been developed.
Molift Inc. developed the “Quick Raiser 2”, which
lifts a user with a linear actuator and supports the
standing-up and seating motions (Molift, 2012).
Sankai proposed some exoskeleton-type power-
assisted systems using electric motors and air
actuators (Satoh et al., 2009). Bostelman et al.
developed a robot system that a user himself wears
and enables him to use a toilet, a bed, and so forth
(Bostelman and Albus, 2007). A caregiver robot “RI-
MAN” developed at RIKEN is aimed at realizing
autonomous motion transfer (Onishi et al., 2007).
Some of those tools and robots are, however,
expensive and are limited for use in indoor
environments.
We take notice of a transfer tool that can be used
even when going away. Similar to some commercial
transfer products, “Komawari-san” is a simple tool
based on lever principles (HEARTS-EIKO, 2012).
These tools, however, are too large and heavy to
carry over long distances. “RODEM” is a new type
of electric wheelchair on which the user can ride
from the backside and which can run outdoors, but
the target is limited to mild patients (VEDA, 2012).
This paper presents a wheelchair with a lifting
function that is intended mainly for use by an
electric wheelchair user with disabled upper and
lower limbs. This equipment has good
maneuverability. Moreover, it can move over a step
because of the front driving wheels. It realizes easy
and safe transfer from/to a bed and a toilet stool by
virtue of the opposite wheel allocation of a usual
wheelchair. Furthermore, the mechanism of folding
the frame for lifting allows this wheelchair to travel
on public roads. We demonstrate its design
effectiveness through several indoor and outdoor
experiments.
2 CONCEPTUAL DESIGN
We assume a single caregiver for the use of this
wheelchair. It helps alleviate the burden of the
caregiver when a disabled person moves between the
wheelchair and toilet/bed easily and safely.
489
Mori Y., Sakai N. and Katsumura K..
Development of a Wheelchair with a Lifting Function.
DOI: 10.5220/0004114904890492
In Proceedings of the 9th International Conference on Informatics in Control, Automation and Robotics (ICINCO-2012), pages 489-492
ISBN: 978-989-8565-22-8
Copyright
c
2012 SCITEPRESS (Science and Technology Publications, Lda.)