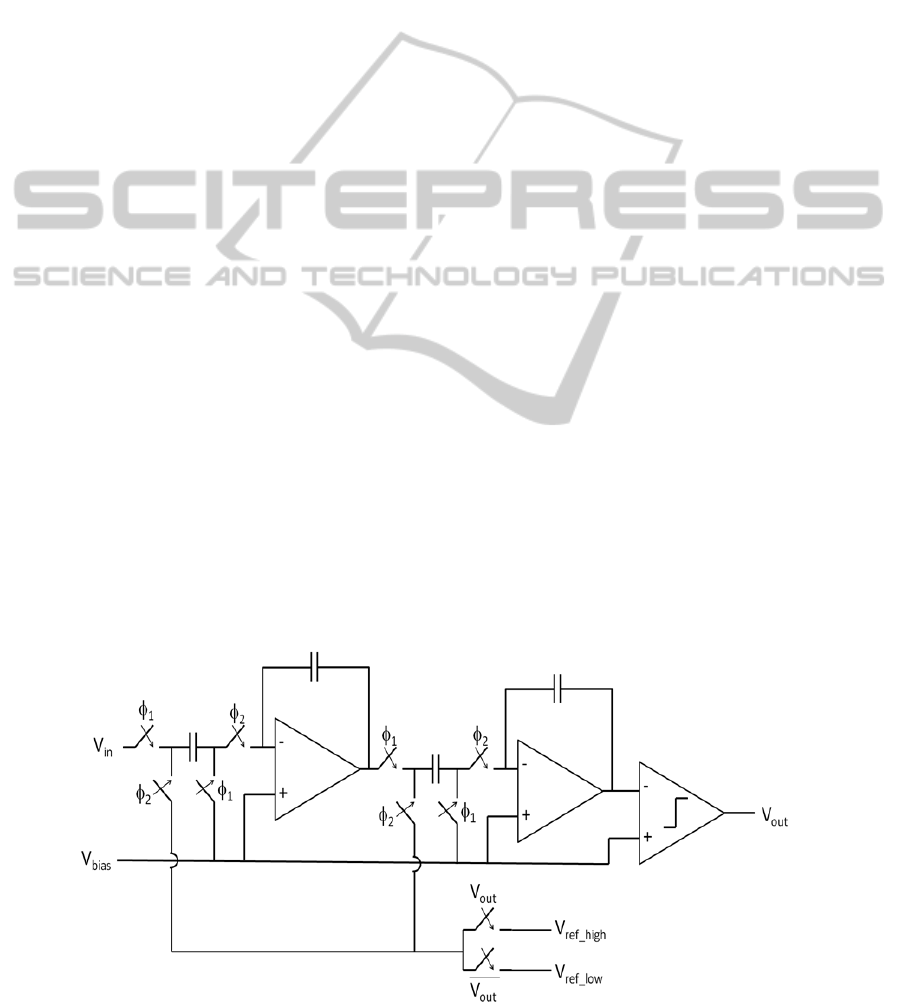
the top-level schematic of the biosensor system.
In order to create an accurate chemical image, the
electrodes need to be spaced at distances comparable
to the size of individual cells within the tissue sam-
ple. Electrode pitches of 10µm to 25µm are desirable.
Ideally, each electrode should have its own dedicated
circuitry; however with the extremely small electrode
pitch this is not realistic. Regardless, minimizing
the area of the circuitry is important to reduce the
number of shared electrodes per circuit block. Like-
wise, power consumption should be minimized since
the biosensor will contain many copies of the detec-
tion circuitry running in parallel. Power consumption
must also be limited to avoid heat build-up within the
tissue, possibly causing damage.
The chemical signals detected with the potentio-
stat typically have very low bandwidths; nitric ox-
ide signals do not normally exceed 1 kHz. While
bandwidth requirements are low, measurement ac-
curacy is much more important. Noise and signal
distortion must be avoided to preserve the integrity
of the small signals inherent in bio-electric systems.
Sigma-Delta ADCs are ideal for biosensor applica-
tions because they inherently have higher resolution
and lower bandwidth than other ADC topologies.
Many different designs for low-power Sigma-
Delta Modulators have been presented. The de-
signs in both (Zhang, 2010) and (Jasutkar, 2011) are
based on 0.18µm CMOS processes with nominal 1.8V
power supplies. These designs use standard archi-
tectures and standard techniques for reducing power.
The design in (Zhang, 2010) was intended for au-
dio applications, while (Jasutkar, 2011) presents a
design for biomedical applications such as electo-
cardiograms. The designs presented in (Goes, 2006)
and (Lee, 2006) also use 0.18µm CMOS processes
but they use supply voltages of 0.9V and 0.8V re-
spectively to reduce power. Besides lowering the sup-
ply voltage, these designs modify the standard archi-
tecture to save power. (Goes, 2006) shares a single
op-amp between multiple integrator stages and (Lee,
2006) is able to be used at different speeds depending
on the application to maximize efficiency. The design
presented in this paper explores the efficiency of using
a reduced power supply to lower power consumption
while still using a standard, easy to implement archi-
tecture.
All of these designs are also fully differential ar-
chitectures while the proposed design is single ended.
The use of differential design has the advantage of
expanded output range; however, our application fo-
cuses on NO which has a narrow activation range.
Therefore, a single-ended design is chosen for re-
duced silicon area. In switched-capacitor circuits
where capacitors can occupy a large percentage of the
total area, this is critical. Section II of the paper will
detail the design of the modulator and its components,
and Section III will cover the proposed physical lay-
out and present simulation results.
2 PROPOSED LOW POWER
MODULATOR DESIGN
2.1 Top Level Design
The overall block level diagram of the proposed mod-
ulator is shown in Figure 3. The design is imple-
mented using a standard 0.18µm silicon process and
a supply voltage of 900mV. The overall topology is
a single ended, second order, Sigma-Delta modulator.
This topology uses two integrators, a comparator, and
a 1bit DAC to provide feedback. With accuracy and
Figure 3: Top level modulator schematic.
BIODEVICES2013-InternationalConferenceonBiomedicalElectronicsandDevices
6