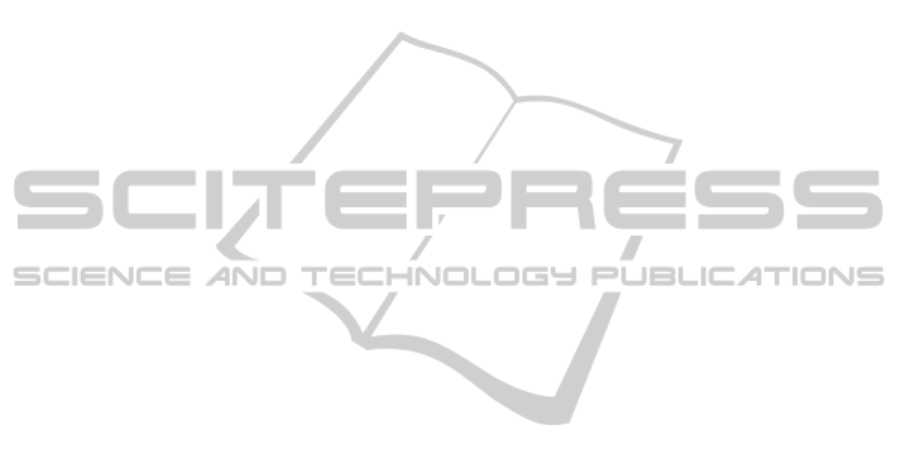
membrane approximates a linear function, as it
steadily decreases with increasing pyramid size. The
upper graph in Fig. 5 shows the membrane
deflection for different pyramid sizes. One important
aspect to point out is the constant maximum
deflection value for the membrane, not at a single
point, but under the complete pyramid base area.
This last effect cannot be modelled by using the
mathematical formulation presented in Section 3,
even if we modify it to increase its accuracy in order
to get closer to the results obtained by FE analysis.
Fig. 4 and Fig. 5 also show that the presence of a
pyramid on top of the membrane of our capacitive
MEMs pressure sensor produces a smaller deflection
than expected in the fault-free case. Thus, this faulty
condition implies a sensitivity loss of the sensor that
can compromise its reliability, which is a critical
issue for implantable devices.
Therefore, it is important to count on an accurate
behavioural model for its main component, the
membrane, valid for both fault-free and faulty
conditions. As said before, its deflection can have an
acceptable analytical solution in the fault-free case.
However, in this work we have proven that this
mathematical formulation is no longer valid for
modelling the membrane with certain kinds of faults
as, for example, the formation of pyramids on top of
the membrane. Therefore it is necessary to create
additional mathematical models that accurately
describe the behaviour of the membrane under faulty
conditions, considering the deflection results
obtained through FE simulations. Especially for
those faulty cases which significantly affect the
geometry and/or material properties of the
membrane.
5 CONCLUSIONS
In this work test-related problems for implantable
capacitive MEMS pressure sensors for the early
detection of in-stent restenosis have been presented.
The typical failure mechanisms and defects that can
give raise to the faulty behaviour of a
microelectromechanical system have also been
explained.
The deflection problem of circular membranes
has been proven to be analytically or numerically
solvable for a fault-free case, in order to build a
behavioural model of the sensor. Nevertheless, this
mathematical model is not valid to describe certain
faulty conditions where the geometry or the material
properties of the membrane are seriously affected.
So as to obtain a realistic fault model in these cases a
finite-element analysis must be performed.
REFERENCES
Castillejo A., Veychard D., Mir S., Karam J., Courtois B.,
Failure Mechanisms and Fault Classes for CMOS-
Compatible Microelectromechanical Systems, IEEE
International Test Conference, pp. 541–550, 1998.
Chang S.-P., Lee J.-B., Allen M.G., Robust capacitive
pressure sensor array, Sensors and Actuators A:
Physical, vol. 101, pp. 231–238, September 2002.
Huang Y., Vasan A. S. S., Doraiswami R., Osterman M.,
Pecht M., MEMS Reliability Review, IEEE
Transactions on Device and Materials Reliability, vol.
12, no. 2, pp. 482-493, June 2012.
Landsberger L. M., Nashed S., Kahrizi M., Paranjape M.,
On Hillocks Generated During Anisotropic Etching of
Si in TMAH, Journal of Microelectromechanical
Systems, vol. 5, no. 2, pp. 106-116, 1996.
Mir S., Charlot B., Courtois B., Extending Fault-Based
Testing to Microelectromechanical Systems, Journal
of Electronic Testing: Theory and Applications, vol.
16, pp. 279–288, 2000.
Mukherjee T., Fedder G. K., Blanton R. D., Hierarchical
design and test of integrated microsystems, IEEE
Design and Test of Computers, vol. 16 (4), pp.18–27,
1999.
OECD (2010), Health at a Glance: Europe 2010, OECD
Publishing. http://dx.doi.org/10.1787/health_glance-
2010-en
Rosing R., Reichenbach R., Richardson A., Generation of
component level fault models for MEMS,
Microelectronics Journal, vol. 33, pp. 861–868, 2002.
Takahata K., Gianchandani Y. B., Wise K. D.,
Micromachined antenna stents and cuffs for
monitoring intraluminal pressure and flow, Journal of
Microelectromechanical Systems, vol 15(5), pp. 1289–
1298, October 2006.
Teegarden D., Lorenz G., Neul R., How to model and
simulate microgyroscope systems, IEEE Spectrum 35
(7), pp. 66–75, 1998.
Timoshenko S., Theory of Plates and Shells, McGraw-
Hill, New York, 1940.
Wang L-T., Stroud C. E, Touba N. A., System-on Chip
Test Arquitectures. Nanometer Design for Testability,
1st. ed., Elsevier: Morgan Kaufmann Series, 2008.
BIODEVICES2013-InternationalConferenceonBiomedicalElectronicsandDevices
158