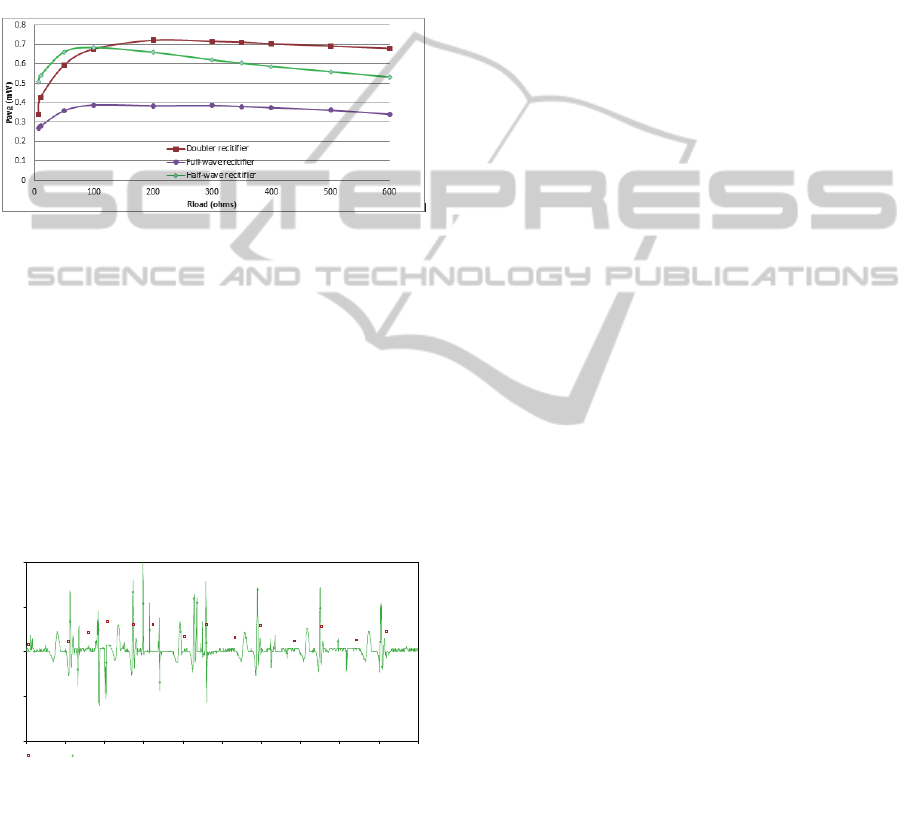
simulations were performed with the aid of pSpice
simulation software (Cadence Design Systems, UK)
for each type of rectifier with several load
resistances and capacitors values, and the results are
shown in Figure 4. The source used in each
simulation is represented by the generator open-
circuit waveform and a 6Ω resistor representing coil
resistance. In order to maximise the output power,
the PMEG 2010EH diodes were used as they present
lower forward voltage (Caroll, 2005).
Figure 4: Simulations results of maximum output power
for rectification circuits depending on load resistances for
3.5mF capacitor.
Due to the overall reduced voltage drop across
the diodes in the full- wave rectifier circuit, the
doubler circuit performed the best. The maximum
output power was achieved for 250 Ω, with a peak
instantaneous power value of 3 mW. Due to the fact
that the rectification was performed for a pulsed type
of power a capacitance value of 3.5mF was used, as
it provided increased values for the output voltage.
Figure 5 presents the input and the rectified
waveforms for the optimum load resistance.
Figure 5: Typical waveform generated by the prototype
during walking and the rectified waveform with a doubler
circuit for the optimum load resistance (250Ω).
5 CONCLUSIONS
Two different energy harvesting techniques have
been compared in order to prove their suitability to
power an activity monitoring device. The
electromagnetic generator has proved to be superior
to the piezoelectric system. With the given space of
50x15x15 mm
3
the generator produced power levels
of 4.5 mW AC and 0.8 mW for pulsed DC, almost
sufficient to meet the requirements of the nRF chip.
Work is on-going to investigate the effect of the
additional half coils over the output power.
However, the optimum speed being around 7-8 km/h
might make this type of energy harvesting system
more suitable for more active people. For the
piezoelectric system, the selection of materials
available for this work has not given the desired
outcome, with the piezoceramic disks giving low
output powers and being subjective to damage due
to repeated stress caused by the constant pressure
applied during walking. Although piezoelectric
components are capable of providing high output
voltage, the output power is limited by the loading
of the capacitive impedance.
REFERENCES
L. Mateu, F. Moll, and U. Polit, “Review of Energy
Harvesting Techniques and Applications for
Microelectronics,” Energy.
J. Paulo and P. D. Gaspar, “Review and Future Trend of
Energy Harvesting Methods for Portable Medical
Devices,” Engineering, vol. II, 2010.
H. A. Sodano, D. J. Inman, and G. Park, “Comparison of
Piezoelectric Energy Harvesting Devices for
Recharging Batteries,” Power, vol. 16, no. 10, pp.
799-807, 2005.
Arnold, D.P.; ‘Review of microscale magnetic power
generation’, IEEE Transactions on Magnetics, Vol.
43, No. 11, November 2007, pp. 3940 – 3951
Carroll. D, Duffy. M, Modelling, design, and testing of an
electromagnetic power generator optimized for
integration into shoes, Journal Article 2011, 8
September 9, 2011, Proceedings of the Institution of
Mechanical Engineers, Part I: Journal of Systems and
Control Engineering, Volume 226 issue 2, pages 256-
270
E. Lefeuvre, Badel, C. Richard, L. Petit, and D. Guyomar,
“A comparison between several vibration-powered
piezoelectric generators for standalone systems,”
Sensors and Actuators A: Physical, vol. 126, no. 2, pp.
405-416, Feb. 2006.
S. R. Anton and H. Sodano, “A review of power
harvesting using piezoelectric materials (2003–2006),”
Smart Materials and Structures, vol. 16, no. 3, pp.
R1–R21, Jun. 2007.
J. Kymissis, C. Kendall, J. Paradiso, and N. Gershenfeld,
“Parasitic power harvesting in shoes,” Digest of
Papers. Second International Symposium on Wearable
Computers (Cat. No.98EX215), pp. 132–139.
J. Perttunen, "Foot loading in normal and pathological
ime
5.0s 5.5s 6.0s 6.5s 7.0s 7.5s 8.0s 8.5s 9.0s 9.5s 10.0s
V(0,R2:1) V(R1:1,V1:-)
2.0V
1.0V
0V
1.0V
2.0V
BIODEVICES2013-InternationalConferenceonBiomedicalElectronicsandDevices
276