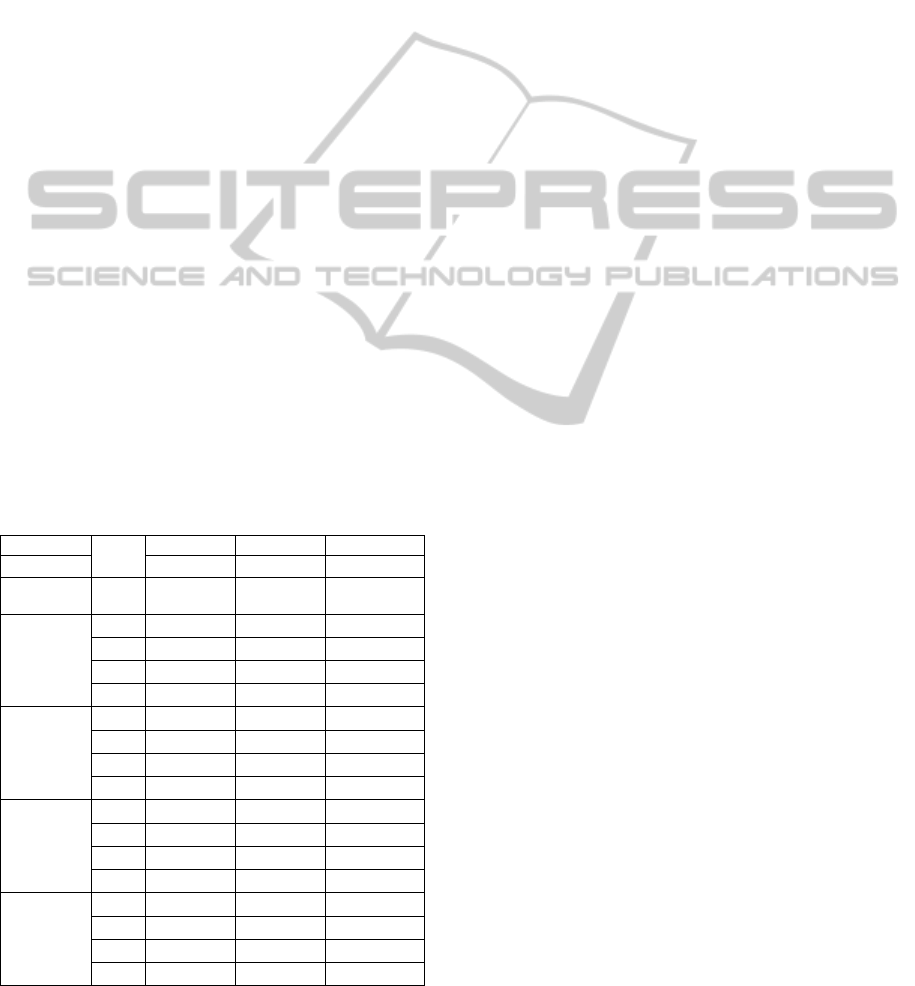
surface, leading finally to a paler shade.
CIE a* value represents redness and greenness of
a sample. The more positive the value of CIE a* is,
the redder the shade of the sample will be and vice
versa. In Table 1, the laser engraved denim fabrics
resulted in all negative values of CIE a* with the
magnitude of the values tending to increase. The
CIE a* value of the untreated denim fabric was 0.50,
which indicating that the original denim fabric was
redder than the laser-engraved fabrics. Upon the
laser treatment with different pixel time and
resolution, the pixel time of 110 µs gave the least
reduction in CIE a* followed by 160, 220 and 300
µs respectively. Since the yarns in denim fabric were
blue indigo ring-dyed, the core of the yarn remained
white in colour. In laser engraving, the fibre
together with the blue indigo dyes in the sheath of
yarn were removed from fibre surface leaving a
paler blue colour remaining in the yarn. Owing to
the thermal effect occurred during laser engraving,
thermal oxidation would occur resulting in yellow
surface colour in the yarn. The yellowing in cotton
yarn together with the remaining blue indigo dye
remained in the fabric surface contributes to a
greenish effect on the fabric surface. Since the laser
power increases correspondingly with the increment
of pixel time and resolution, thus the enhanced
thermal oxidation effect contributing to more yellow
surface colour would be obtained resulting in
increased greenish effect.
Table 1: CIE L*a*b* values of differently laser engraved
denim fabrics.
Sample
CIE L* CIE a* CIE b*
Control 21.63 0.50 -4.45
Pixel time
(µs)
dpi
110
30
31.89 -0.77 -4.05
60
42.56 -1.34 -1.55
80
51.99 -1.49 3.20
100
52.45 -1.55 5.44
160
30
35.59 -1.03 -3.65
60
42.78 -1.38 -0.23
80
53.76 -1.53 5.06
100
54.91 -1.65 6.30
220
30
35.89 -1.13 -3.06
60
47.42 -1.49 3.65
80
54.15 -1.57 5.39
100
54.98 -2.23 6.73
300
30
39.29 -1.26 -2.49
60
51.48 -1.59 3.70
80
55.23 -2.00 5.76
100
55.70 -2.36 6.82
Table 1 shows CIE b* values of the denim fabrics
after the laser engraving with different process
parameters. Generally speaking, CIE b* value
describes the yellowness and blueness of a sample.
The higher the positive the value of b*, the more the
yellowish of the sample will be and vice versa. The
CIE b* value of the untreated denim fabric was -
4.45 but after laser treatment, the CIE b* values
increased. The laser engraved fabrics tended to have
a yellowish shade with the prolonged pixel time and
increased resolution. According to Figure 2, the
increase in pixel time and resolution would increase
the laser power in the engraving process. Thus,
more fibres containing the blue dye could be
removed from the fabric surface resulting in a paler
blue shade with increasing CIE b* values. In
addition, the thermal oxidation effect imparted onto
the fibre could give yellowing effect on the fabric
surface also increase the CIE b* values.
4 CONCLUSIONS
Denim fabrics were engraved by laser with different
process parameters, i.e. resolution and pixel time.
Experimental results revealed that the increased
resolution and pixel time would increase the laser
power density accordingly. Under the influence of
high laser power, a paler surface appearance was
noted on the denim fabric. At the same time, the
K/S
sum
values were reduced accordingly, indicating
that the amount of blue dye on denim fabric was
decreased significantly. Meanwhile, the
measurement results of CIE L*a*b* values revealed
that a lighter shade was obtained for the laser-
engraved denim fabrics and also a green-yellow look
was observed for the denim fabrics. In conclusion,
with the suitable selection of various laser process
parameters, the laser engraving process could be
technically used as a novel dry surface treatment for
creating different shading effects on denim fabric.
REFERENCES
Dascalu, T., Acosta-Ortiz, S. E., Ortiz-Morales, M. and
Compean, I., 2000. Optics and Lasers in Engineering.
34, 179.
Esteves, F., Alonso, H., 2007. Research Journal of Textile
and Apparel. 11(3), 42.
Ferreo, F., Testore, F., 2002. Autex Research Journal.
2(3), 109.
Kamata, K., Suzuki, A., 2004. Journal of Applied Polymer
Science. 92, 1454.
PHOTOPTICS2013-InternationalConferenceonPhotonics,OpticsandLaserTechnology
132