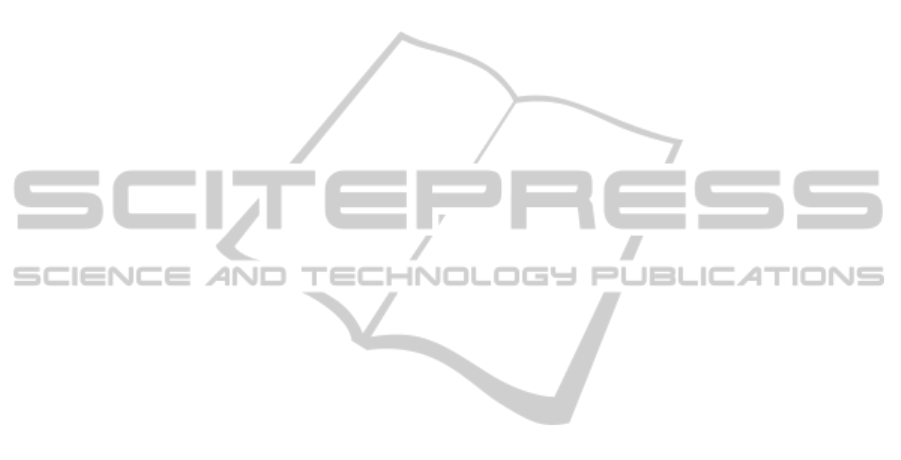
01IS10033D), funded by the German Federal Min-
istry of Education and Research.
REFERENCES
Abdallah, S. and Nijmeh, S. (2004). Two axes sun track-
ing system with plc control. Energy Conversion and
Management, 45(1112):1931 – 1939.
Chandola, V., Banerjee, A., and Kumar, V. (2012).
Anomaly detection for discrete sequences: A survey.
Knowledge and Data Engineering, IEEE Transactions
on, 24(5):823 –839.
Draper, D. (1988). Rank-based robust analysis of linear
models. i. exposition and review. Statistical Science,
3(2):pp. 239–257.
Fu, T.-c. (2011). A review on time series data min-
ing. Engineering Applications of Artificial Intelli-
gence, 24(1):164 – 181.
Gaber, M. M., Zaslavsky, A., and Krishnaswamy, S. (2005).
”mining data streams: a review”. SIGMOD Rec.,
34(2):18–26.
Guenther, J., Rothe, M., Hefer, J., Middendorf, A., and
Lang, K. (May). Condition monitoring system
adapted for photovoltaic power converter. In Environ-
ment and Electrical Engineering (EEEIC), 2011 10th
International Conference on, pages 1–4.
Hill, T. and Lewicki, P. (2005). Statistics: Methods and
Applications. StatSoft, Inc.
Hinkley, D. V. (1971). Inference about the change-point
from cumulative sum tests. Biometrika, 58(3):pp.
509–523.
Keogh, E., Lin, J., and Fu, A. (2005). Hot sax: efficiently
finding the most unusual time series subsequence. In
Data Mining, Fifth IEEE International Conference on,
page 8 pp.
Makhoul, J., Kubala, F., Schwartz, R., and Weischedel, R.
(1999). Performance measures for information extrac-
tion. In In Proceedings of DARPA Broadcast News
Workshop, pages 249–252.
Middendorf, A., Nissen, N., Guttowski, S., and Lang, K.
(2011). Electronics condition monitoring for improv-
ing sustainability of power electronics. In Seliger,
G., Khraisheh, M. M., and Jawahir, I., editors, Ad-
vances in Sustainable Manufacturing, pages 171–175.
Springer Berlin Heidelberg.
Moore, L. M. and Post, H. N. (2008). Five years of oper-
ating experience at a large, utility-scale photovoltaic
generating plant. Progress in Photovoltaics: Research
and Applications, 16(3):249–259.
Oozeki, T., Yamada, T., Otani, K., Takashima, T., and Kato,
K. (2010). An analysis of reliability in the early stages
of photovoltaic systems in japan. Progress in Photo-
voltaics: Research and Applications, 18(5):363–370.
Papadakis, K., Koutroulis, E., and Kalaitzakis, K. (2005).
A server database system for remote monitoring and
operational evaluation of renewable energy sources
plants. Renewable Energy, 30(11):1649 – 1669.
Peng, Z. and Chu, F. (2004). Application of the wavelet
transform in machine condition monitoring and fault
diagnostics: a review with bibliography. Mechanical
Systems and Signal Processing, 18(2):199 – 221.
Perpian, O. (2009). Statistical analysis of the performance
and simulation of a two-axis tracking pv system. Solar
Energy, 83(11):2074 – 2085.
Robbins, M., Gallagher, C., Lund, R., and Aue, A. (2011).
Mean shift testing in correlated data. Journal of Time
Series Analysis, 32(5):498–511.
Sanz-Bobi, M. A., Roque, A. M. S., de Marcos, A., and
Bada, M. (2012). Intelligent system for a remote di-
agnosis of a photovoltaic solar power plant. Journal
of Physics: Conference Series, 364(1):012119.
Saravanan, N., Siddabattuni, V. K., and Ramachandran, K.
(2010). Fault diagnosis of spur bevel gear box us-
ing artificial neural network (ann), and proximal sup-
port vector machine (psvm). Applied Soft Computing,
10(1):344 – 360.
Sundheim, B. M. (1992). Overview of the fourth message
understanding evaluation and conference. In Proceed-
ings of the 4th conference on Message understanding,
MUC4 ’92, pages 3–21, Stroudsburg, PA, USA. As-
sociation for Computational Linguistics.
Toliyat, H. A., Nandi, S., Choi, S., and Meshgin-Kelk,
H. (2012). Electric Machines: Modeling, Condition
Monitoring, and Fault Diagnosis. CRC Press.
Venkatasubramanian, V., Rengaswamy, R., Kavuri, S. N.,
and Yin, K. (2003). A review of process fault de-
tection and diagnosis: Part iii: Process history based
methods. Computers and Chemical Engineering,
27(3):327 – 346.
Wayne, T. A. (2000). Change-point analysis: A power-
ful new tool for detecting changes. CTAN: http://
www.variation.com/cpa/tech/changepoint.html.
Widodo, A. and Yang, B.-S. (2007). Support vector ma-
chine in machine condition monitoring and fault di-
agnosis. Mechanical Systems and Signal Processing,
21(6):2560 – 2574.
Wirth, H. (2013). Aktuelle Fakten zur Photovoltaik
in Deutschland. http://www.ise.fraunhofer.de/de/
veroeffentlichungen/veroeffentlichungen-pdf-dateien/
studien-und-konzeptpapiere/aktuelle-fakten-zur-photo
voltaik-in-deutschland.pdf.
SMARTGREENS2013-2ndInternationalConferenceonSmartGridsandGreenITSystems
164