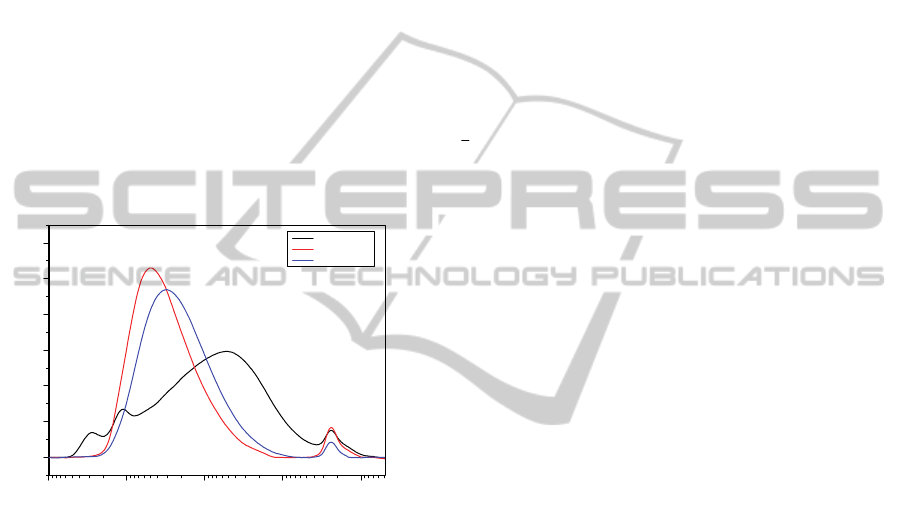
vulcanization, in terms of both vulcanization
velocity and maximum torque reached.
In order to interpret theoretically experimental
results obtained, a peroxide decomposition kinetic
model is presented, considering the complex set of
reactions that characterize peroxide crosslinking,
namely homolytic cleavage of peroxide, hydrogen
abstraction, polymer radicals formation, polymer
radicals coupling, cross-link formation and polymer
scission.
Starting from the above -most probable- kinetic
scheme, a system of non-linear differential equations
with few variables is obtained and solved
numerically, after suitable variable substitutions, by
means of a Runge-Kutta algorithm. Crosslinking
density is thus evaluated numerically and compared
to rheometer experimental curve, which may provide
a reliable indication of the average cured rubber
crosslinking, once suitably scaled to unitary values.
Figure 1: Molecular weight distribution of Vistalon 1703
compared with other two distributions of common
industrial products.
By means of the numerical approach proposed,
an estimation of the kinetic constants per single
reaction, once known kinetic decomposition laws,
may be evaluated and hence the activity of each
peroxide may be estimated using a few experimental
data at only two different temperatures.
By means of the additional experimental and
numerical evaluation of the stress-strain curves of
the vulcanized samples, it is also possible to
establish a correlation between tensile strength and
maximum torque obtained with the rheometer test,
again useful for an optimization of the production
processes.
It has to be finally considered that, for thick
items exceeding 5 mm, a numerical algorithm is
already at disposal to determine the most suitable
temperatures and exposition times to be used in the
industrial production, in order to guarantee that the
core results not under-vulcanized and the skin not
over-vulcanized.
2 RETICULATION KINETIC OF
EPDM VULCANIZED WITH
PEROXIDES
The basic chemistry in the generally accepted
mechanism of peroxide cure of EPDM have been
reviewed by van Duin and co-workers (Dees and
van Duin, 2008); (van Duin, 2002), and may be
summarized by means of the following partial
reactions occurring in series and parallel:
(addition)
HEP(D)MEP(D)MEP(D)MEP(D)MEP(D)MEP(D)M
on)(combinati
EP(D)M-EP(D)M2EP(D)M
nabstractio-H
HROH/R'EP(D)M/R'ROH-EP(D)M
initiation
R'ROROOR
2
1
(1)
The chain of free-radical reactions is initiated by
thermal decomposition of the peroxide, yielding
primary alkoxy (RO) or secondary alkyl radicals
(R). Subsequent abstraction of H-atoms from the
EPDM polymer results in the formation of EPDM
macro-radicals (EPDM). Calculations based on
kinetic data for H-abstraction indicate that H-
abstraction mainly occurs along the saturated EPM
polymer backbone, Van Duin (2002), whereas
several electron paramagnetic resonance (EPR)
spectroscopy studies have shown the selective
formation of allyl radicals derived from the diene
monomer.
Considering the energy required for the
abstraction of the H-atoms, see Figure 2, within the
formation of the back-bone, the allyl radicals are
more probable than the others, because of the lowest
energy required by the abstraction of the H-atoms ,
Knox and Palmer (1961).
The actual cross-linking proceeds via two
pathways, which have been shown to be additive.
Two EPDM macro-radicals either combine or,
alternatively, a macro-radical adds to an EPDM
unsaturation. Visible spectroscopy has confirmed the
conversion of the EPDM unsaturation upon peroxide
cure, Dickland and van Duin (2002). It is noted that
in practical EPDM/peroxide compounds usually co-
agents, such as triallyl (iso)cyanurate,
trimethylolpropane trimethacrylate or m-
phenylenebis(maleimide), are included to increase
the peroxide curing efficiency, Hofmann (1989),
which obviously affects the mechanism of peroxide
1E7 1000000 100000 10000 1000
0,0
0,2
0,4
0,6
0,8
1,0
1,2
a.u
PM (g/mol)
V1703 norm
CO-058 norm
V785 norm
NumericalModelforthePredictionofFinalMechanicalPropertiesofEPDMVulcanizedwithPeroxides-PartI:Basisof
theNumericalModelandExperimentalCampaign
59