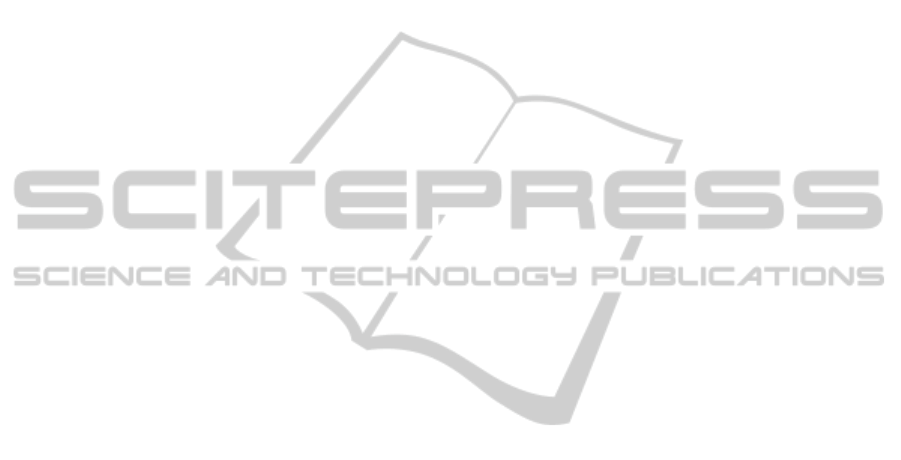
covered with insulators and in high temperature,
transferring heat up to the surface of insulators.
When cooling device is used to cool the pipes in
high temperature, thermal diffusion is disturbed
depending on existence of defects in inside of the
pipes. Insulation effects by defects cause difference
in temperature locally on surface of the pipes. When
IR camera is used to obtain thermal image of the
pipes where such temperature difference occurred,
defects in the pipes are shown in image depending
on existence of defects. Therefore, after examining
various cooling methods and investigating
applicability of such methods, the authors found out
the optimal cooling method to detect defects in
NPP’s pipes with use of infrared thermography.
3.1.1 Tube Air Cooler
A tube air cooler is a cooling device where pathway
of air current is narrowed to increase fluid velocity
as compressed air rotates in high speed, which aims
at separating hot air current from cool air current.
The tube air cooler uses compressed air in a general
compressor to cool air readily. In addition, the
cooler is fundamentally safe because refrigerant,
electricity or any chemicals are not used for the
cooler. The cooler is effective specially for local
cooling even though it has low capacity. However,
the cooler has some drawbacks because it requires
an additional equipment to use compressed air and
needs to be installed with equipment that produces
compressed air in order to be used portably.
3.1.2 Air-cooling and Water-cooling Coolers
A cooler is a device that converts high-temperature
high-pressure gaseous refrigerant to low-temperature
liquid refrigerant. Gaseous refrigerant containing
heat that is taken away from evaporator gets cooled
as it passes through condenser. Therefore, heat is
released to the outside as the gaseous refrigerant is
turned to the liquid refrigerant. Cooler can be
classified to air-cooling cooler and water-cooling
cooler. The air-cooling cooler has the excellent
cooling capability as it prevents degradation of
cooling function that is attributable to increase in
room temperature. Moreover, the air-cooling cooler
enables keeping temperature constant precisely and
can be adjusted in the wide range of use. The water-
cooling cooler uses water from a cooling tower to
work in the condensation cooling method. It
minimizes indoor noise and shows the higher
cooling efficiency than the air-cooling cooler.
3.1.3 Heat Pipe-type Cooler
A heat pipe-type cooler is a cooling device that
transfers heat in large quantity to condenser prior to
using the pin installed in the condenser for cooling
through natural convection or forced convection.
The heat pipe-type cooler uses working fluid of FC-
27 in the maximum thermal load of 1.5 ㎾. In
addition, it has the operating temperature of –
30~120℃ with the high cooling efficiency. Since
water quantity in heat pipe can be adjusted, the heat
pipe-type cooler can be manufactured in various
forms. However, the heat pipe-type cooler has
drawbacks that it takes longer time for cooling than
other coolers and requires the installation of an
additional fan to increase cooling efficiency.
3.1.4 Fan Cooler
A fan is a device that stirs up the wind as wings
installed on the axis of electric motor rotate. The fan
can be classified to desk fan, ventilating fan and
stand fan depending on shape and purpose of use.
Major parts of the fan include stand, pillar, motor,
and wing. It can be adjusted quite freely according
to angle and direction of movement (up and down or
right and left). The pillar of the fan also can be
adjusted upwardly or downwardly. The fan has the
front-side control panel that enables an easy control
as all of the devices are installed on the front side of
stand. The fan can be also classified to turbo fan,
limit fan and sirocco fan depending on shape of
wing. The turbo fan has the wing that its tip is bent
to the backward of rotation direction, which includes
the one with curved wing and the one with straight
wing. The turbo fan shows the high efficiency and
can be operated relatively quietly even at a high
speed. The limit fan is an upgraded version of the
turbo fan and the sirocco fan. It has the streamlined
wing that is manufactured by folding a thin plate.
Therefore, the limit fan can be rotated in a high
speed with low noise. The sirocco fan has a bent
shape as the tip of wing is bent toward the rotation
direction. Compared to other types of fans in the
same capacity, the sirocco fan features the
significantly low number of rotation.
3.2 Selection of a Cooling Method
In this study, the optimal cooling method was
selected to obtain thermal image of defects in
geometric shape in an easier and quicker way with a
view to examining defect size and depth from
DetectionofHotPipeDefectsusingIRThermography
229