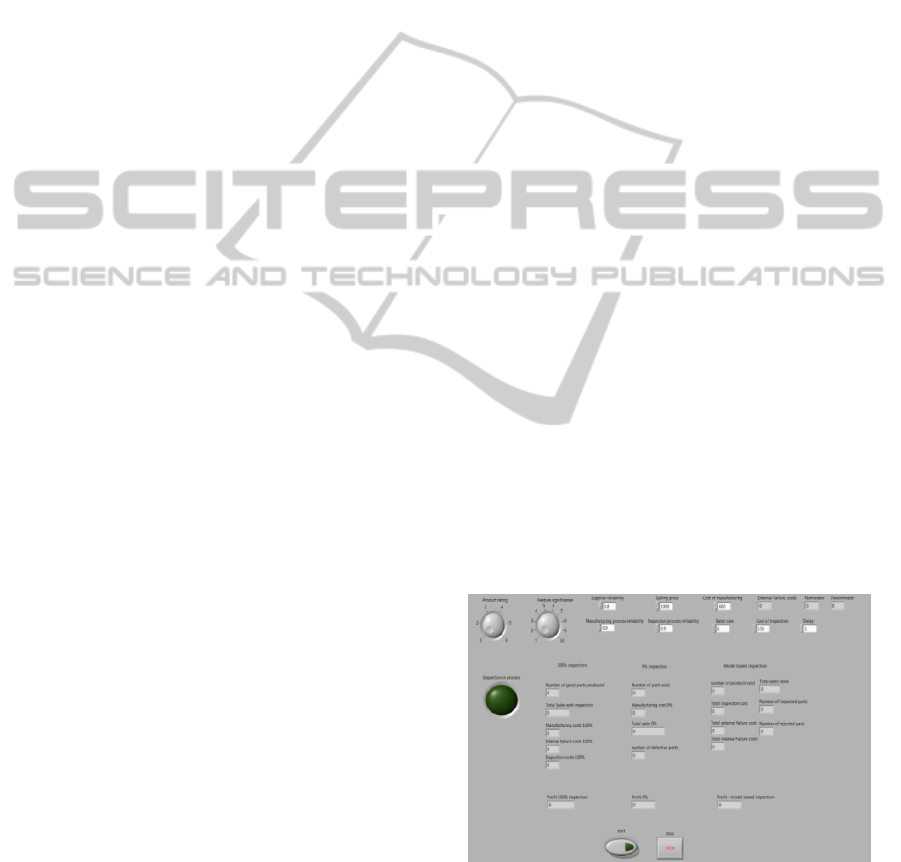
The twentieth trial involved a batch size of 100 000.
Due to the high product rating, the difference in
profit between the 100% and 0% inspection
strategies was extreme. The model was however
able to obtain the same profit a with the 100 %
inspection.
5 CONCLUSIONS
Advanced manufacturing environments involve
frequent changes in product design and process
configuration in accordance with changes in
customer requirements. The supply chain for such an
environment would also have to be dynamic to
accommodate these changes. A model to determine
the frequency of inspection at a strategically located
inspection station was developed using the expected
value formula. The inspection criteria considered
were the costs associated with the product, the
significance of the product to the customer as well as
the supplier and process reliabilities. Twenty trials
were performed whilst varying the inspection
criteria parameters to obtain an overall average
performance of the system. The results from the
simulation were compared to results of simulations
performed to quantify the performance of 100% and
0% inspection process strategies. The 0% inspection
strategy was best suited to processes involving high
reliabilities and low customer significance ratings.
The 100% inspection strategy was best suited to
high customer significance ratings. The model-
based inspection showed an overall increase in
profits gained, for both low and high customer
significance ratings, with a minimisation of the COQ
and was therefore considered to be more suitable to
manufacturing environments which experienced
frequent reconfigurations due to changes in
customer requirements. Further research into
reconfigurable manufacturing systems is currently
being performed globally. A fully functional
manufacturing environment is currently being
implemented at the University of KwaZulu-Natal
manufacturing laboratory. On completion, further
results will be generated and obtained for simulation
of industrial applications.
REFERENCES
Crosby, P. B., Quality is Free. 1979, New York, N. Y.:
McGraw-Hill.
Da Silveira, G., Borenstein, D., & Fogliatto, F. S., 2001.
Mass customization: Literature review and research
directions, International Journal of Production
Economics, 72, (1).
Davrajh, S., Bright, G., 2012. Implementation of
Commercial Products for Reconfigurable Quality
Inspection, M2VIP, NZ
Foster, S. T., 1996 An examination of the relationship
between conformance and quality-related costs,
International Journal of Quality & Reliability
Management, Vol. 13 Iss: 4, pp.50 - 63
Goetsch, D. L., Davis, S. B., 2010. Quality Management
for Organizational Excellence: Introduction to Total
Quality, Pearson, N. J.
ASQ, http://asq.org/learn-about-quality/cost-of-quality/
overview/overview.html, 2013
http://www.statlect.com/expval1.htm, 2013
Juran, J. M., 1951. Quality Control Handbook. 1st ed.,
New York, NY: McGraw-Hill.
Koren, Y., Heisel, U., Jovane, F., Moriwaki, T.,
Pritschow, G., Ulsoy, G., and Van Brussel, H.:
‘Reconfigurable Manufacturing Systems’, CIRP
Annals - Manufacturing Technology, 1999, 48, (2),
pp. 527-540
Nambiar, A. N.: ‘Mass customization : where do we go
from here?’,World Congress on Engineering , WCE
2009, 2009, pp. 687
Pollard, D., Chuo, S., Lee, B., 2008. Strategies For Mass
Customization, In Journal of Business & Economics
Research, 6, (7)
Tseng, M. M., and Du, X., 1998. Design by Customers for
Mass Customization Product, CIRP Annals -
Manufacturing Technology, 47, (1), pp. 103-106
www.ni.com/labview, 2013
Zaklouta, H., 2011. Cost of quality tradeoffs in
manufacturing process and inspection strategy
selection,MSc Thesis, MIT
APPENDIX
Figure A1: GUI for the inspection simulation.
ICINCO2013-10thInternationalConferenceonInformaticsinControl,AutomationandRobotics
556