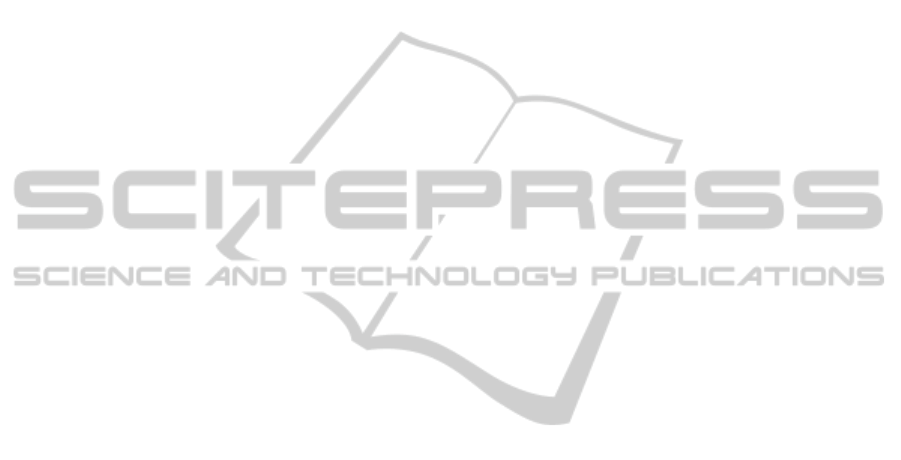
Since the volume of the proposed actuator
(141.3mm
3
) is smaller than that of commercial linear
resonance actuators (360 mm
3
), the proposed
actuator can be easily embedded in mobile devices.
3 CONCLUSIONS
In this paper, we presented a tiny vibrotactile
actuator, which is easily embedded into mobile
devices, consisting of the moving part, two solenoids,
a steel housing, and two covers. Since the proposed
actuator provides enough working frequency and
output force to stimulate human skin, it can
selectively stimulate human’s mechanoreceptors.
According to the current input, the moving part runs
from the initial position to the other end and collides
with a silicon bumper attached to the end of the
solenoid coils in order to generate vibration. Our
work underscores the importance of the proposed
haptic actuator to enable users to experience
immersion while interacting with mobile devices.
ACKNOWLEDGEMENTS
This research was supported by the Basic Science
Research Program through the National Research
Foundation of Korea (NRF) funded by the Ministry
of Education, Science and Technology (grant
number : 2011- 0009757).This research was also
supported by the Dual Use Program Cooperation
Center (Development of tactile display device for
Virtual reality-based flight simulator, 12-DU-EE-03)
REFERENCES
Amemiya, T., Ando, H., and Maeda, T., 2008. Lead-me
interface for a pulling sensation from hand-held
devices. ACM Trans.Appl.Percept., 5(3), 1-17.
Blackberry storm2 touchscreen phone. http://us.
blackberry.com/smartphones/ blackberry-storm-2.html
Cruz, M., & Grant, D. (2011). High Definition Haptics for
Consumer Electronics. IEEE International. Conference
on Consumer Electronics (ICCE), Las Vegas, USA,
57-58
IHS iSuppli, 2012, http://gigaom.com/mobile/ by-2013-it-
will-be-a-smartphone-majority-world/
Johansson, R. S., & Vallbo, A. B., 1979. Tactile
Sensibility in the Human Hand: Relative and Absolute
Densities of Four Types of Mechanoreceptive Units in
Glabrous Skin. Journal of Physiology, 286, 283-300
Johnson, K. O., Yoshioka, T., & Bermudez F.V., 2000.
Tactile functions of mechanoreceptive afferents
innervating the hand. Journal of Clinical
Neurophysiology, 17, 538-558
Katz, D.,1989. The World of Touch. Erlbaum, Hillsdale
Kweon, S. D., Park, I. O., Son, Y. H., Choi, J., & Oh, H.
Y., 2008. Linear vibration motor using resonant
frequency. US PATENT, 7, 358633 B2
Lederman, S. J., 1997. Skin and Touch. Encycloedia of
Human Biology, Second Edition, 8, 49-61
Lylykangas, J., Surakka, V., Salminen, K., Raisamo, J.,
Laitinen, P., Rönning, K., & Raisamo, R., 2011.
Designing Tactile Feedback for Piezo Buttons. ACM
CHI Conference on Human Factors in Computing
Systems, Vancouver, BC, Canada, 3281-3284
Microsoft Tag, 2012. http://tag.microsoft.com/community/
blog/t/the_growth_of_mobile_marketing_and_tagging.
aspx
Poupyrev, I., Maruyama, S., & Rekimoto, J., 2002.
Ambient Touch: Designing Tactile Interfaces for
Handheld Devices, ACM Symposium on User
Interface Software and Technology, Paris, France,
October
Wagner, M., Roosen, A., Oostra, H., Hoppener, R., &
Moya, M. D., 2005. Novel Low Voltage
Piezoactuators for High Displacements. Journal of
Electroceramics, 14 (3), 231-238
SIGMAP2013-InternationalConferenceonSignalProcessingandMultimediaApplications
128