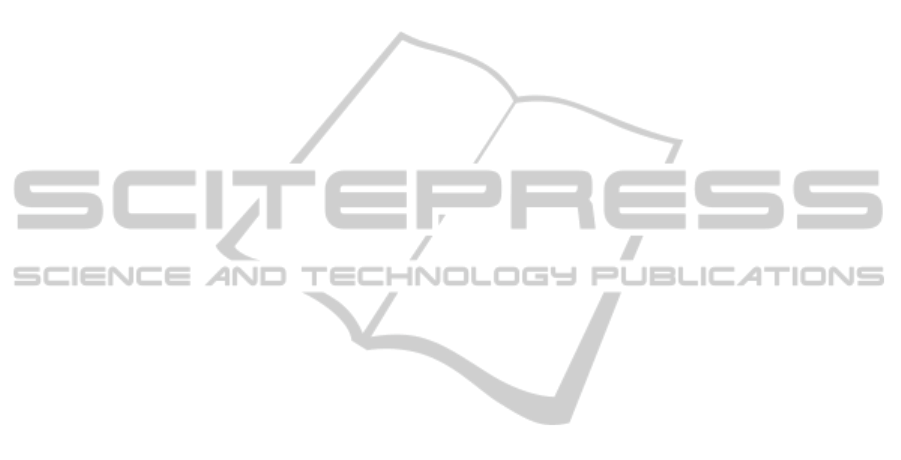
for quality management. The content of these
standards and instructions for the application and
implementation is published widely, e.g. Mahoney
and Thor (1994). An important concept of ISO 9000
for our work is Process-based Quality Management
(PQM) which is also called process-oriented
Management by some authors. Some of the key
characteristics are:
Important activities and resources in enterprises
shall be described as processes and shall be
controlled accordingly
Cross-functional processes need to be identified,
understood and controlled accordingly
The continuous improvement (CI) of the
processes is a permanent goal of an organization
One of the reasons why these standards became well
known was the fact that organizations could be
certified according to ISO 9000 by specific
legitimated third-party agencies. In this paper we are
not focusing on certification but on the principles of
ISO 9000 as these principles can guide every
organization who is implementing a QM system, and
are therefore of high interest in this context.
As mentioned, quality of spatial data is
investigated intensively but process quality and
quality management have not been discussed much
in the geographic domain. The application of PQM
to production processes of geographic data
especially to so-called GIS based Facility
Management Systems (FM-Systems) within utility
companies were investigated by Stürmer (2007).
Within the framework of a project funded by the
research unit of the German Society for Quality
(DGQ), a PQM related to update processes for
geographic data in utilities was developed
(Bockmühl and Reinhardt, 2008). This project
triggered the idea to evaluate the concepts developed
in a practice study over a longer period. The
intended goal of the study is to measure the effects
of changes in processes, e.g. when new data check
methods have been introduced which in other words
is the implementation of a continuous improvement
cycle for geographic data production processes. For
this reason suitable measures had to be developed. In
this paper our main focus is put on introducing a
developed methodology of CI as well as the results
of a case study where this methodology was applied.
Also we focus on explaining which measures can be
used to unveil the effects of changes of processes.
The remainder of this paper is organized as
follows: In section two we will give an overview
about principles of process tracing and general
approaches for CI. We will discuss approaches to
define process quality in general and outline how
this can be applied for geographic data production
processes. In section three some basics of PQM and
its application to FM-systems at utility companies
within the framework of the project “PQM-NIS”
will be outlined. This is followed by a description of
the case study which has been carried out, its
background, organizational requirements and goals
as well as the basic approach of the study, the
analysis of ratios, developed from process related
data and the results of the study. Finally some
conclusions are drawn.
2 PROCESSES – BASICS,
QUALITY MODEL
AND CONTINUOUS
IMPROVEMENT
2.1 Background and Overview
A process in the context of this paper is understood
as any kind of single or connected activities which
has / have input and output. These activities shall be
targeted on the output, for example a product of
required quality, see e.g. (Masing, 1994).
As already mentioned, processes have to be
monitored and checked (and improved if necessary)
continuously. As a general approach for this task the
method DMAIC (Define - Measure - Analyse -
Improve - Control) is very suitable (see Mahoney
and Thor, 1994). It includes the following steps:
Define: Define the goals of the process together
with the customer (user). Emphasize on the process
output and specific characteristics which are chosen
together with the customer.
Measure: Measure the characteristics through
suitable metrics (indicators) to determine the actual
state of the process.
Analyze: Analyze the characteristics of the process
and detect the reason for weaknesses and
deficiencies.
Improve: Improve the process based on the results
of the analyses and discussions with the customer
Control: Check the results of the re-organized
processes.
Figure 1 illustrates the CI process adapted to
geographic production processes. These general
concepts give us guidelines for the CI methodology
we have to develop. But we further need:
A quality model suitable for geographic data
production processes which includes proper
ContinuousImprovementofGeographicDataProductionProcesses-ApproachandResultsofaCaseStudy
345