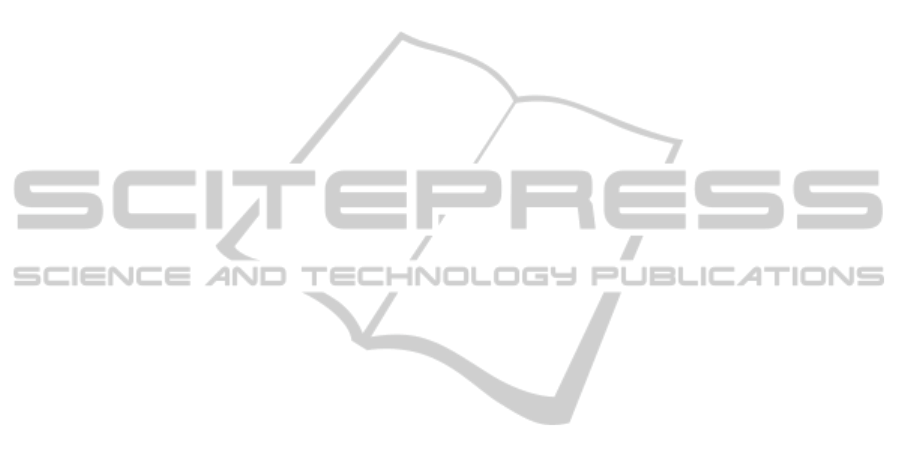
robot needs further information like dimensions
and the mass. Such information the robot can
retrieve from the internet. Then the throwing-robot
has to request the capturing-service from another
robot. After that the transportation can be
performed.
For the transportation of the objects within the
subsystem alternate paths can be used. For that
automatically routing tables can be generated
within the robots similar to the routing tables
within routers in the internet.
5 CONCLUSIONS
In the first part of this paper for the transportation
and handling of workpieces within production
systems a visionary method for throwing and
capturing them by robots was presented. The
advantages of this method would be short times,
high flexibility and the need of few resources. In
several research works it was already proved, that
this method is basically working. On the other hand
further research work is still required to make this
method for practical applications more reliable. In
the second part of the paper it was shown, that the
features of throwing robots provide good conditions
for their integration in IOT-concepts.
REFERENCES
Frank, T., Janoske, U., Mittnacht, A., and Schroedter, C.,
2012. Automated throwing and capturing of cylinder-
shaped objects. In Proceedings of the 2012 IEEE
International Conference on Robotics an Automation
(ICRA 2012), pp. 5264 – 5270.
Frank, T., 2013. Zur Automatisierung des sanften Werfens
und Fangens von Objekten zum Zwecke des
innerbetrieblichen Transports. Bergische Universität
Wuppertal: Dissertation.
Frese, U., Bäuml, B., Haidacher, S., Schreiber, G.,
Schaefer, I., Hähnle, and M., Hirzinger, G., 2001. Off-
the shelf vision for a robotic ball catcher. In
Proceedings of the 2001 IEEE International
Conference on Intelligent Robots and Systems.
Senoo, T., Namiki, A., and Ishikawa, M., 2008. High-
speed throwing motion based on kinetic chain
approach. In Proceedings of the 2008 IEEE
International Conference on Intelligent Robots and
Systems, pp. 3206 – 3211.
Barteit, D. F., 2009. Tracking of thrown objects. Vienna
University of Technology: Dissertation.
Hribernik, K. A., Warden, T., Thoben, K. D., and Herzog,
O., 2010. An Internet of things for transport logistics –
An approach to connecting the information and
material flows in autonomous cooperating logistic
processes. MITIP 2010 – Conference on Modern
Information Technology in the Innovation Processes ,
Aalborg University. Available: http://www.sfb637.uni-
bremen.de/pubdb/repository/SFB637-C2-10-004-IC.pdf
Wagner, T., Haußner, C., Elger, J., Löwen, U., and Lüder,
A., 2010. Engineering processes for decentralized
factory automation systems. InTech. Available:
www.intechopen.com/ books/ factory-automation/engi-
neering-
processes- for- decentralized- factory-automat-
ion- systems
Ten Hompel, M., and Nagel, L., 2008. Cellular transport
systems – Making things move in the „internet of
things.“ Oldenbourg Wissenschaftsverlag, IT- Infor-
mation Technology 50 (2008) 1, pp 59 -65.
Vossiek, M., Miesen, R., and Wittwer, J., 2010. RF
identification and localization - Recent steps towards
the internet of things in metal production and
processing. In Proceedings on 18
th
IEEE International
Conference on Microwave Radar and Wireless
Communications (MIKON).
ICINCO2013-10thInternationalConferenceonInformaticsinControl,AutomationandRobotics
438