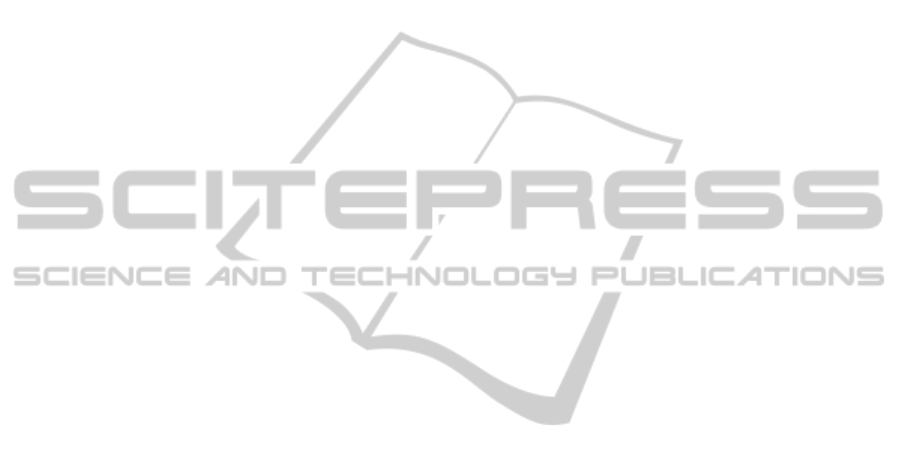
EWjKMLR
n2
(5)
where K
2
=0.8953 [g/(A.day)] is a constant including
Faraday’s constant and the unit conversion factor.
6 DISCUSSION
6.1 Assumptions Discussion
The main assumption used in BEASY CM is the
assumption of the thin layer of electrolyte. This
assumption enables to treat the volume of the
electrolyte as a layer characterized only by the value
of its sheet resistance. Currents flowing through the
layer in the longitudinal direction cause the
continuous distribution of the potential. Mutual
interaction between the electrolyte and the material
of investigated structure is controlled by the
polarization behaviour of the material and is
presented in the electrolyte as a source of current
(positive or negative). This current flows in normal
direction to the surface, represents the corrosion
current and is controlled by the local electrolyte
potential and corresponding polarization curve.
Flow of the current in the volume of the
electrolyte is not solved. This assumption brings
mentioned lowering of computational demand, but
has to be taken into account, when a real situation is
studied. Qualified decision has to be made, if it is
possible to model the situation by BEASY CM or
not. Critical in this case are fine details with
different materials covered by relatively thick layer
of electrolyte. This situation is not common in a case
of atmospheric corrosion, because the thickness of
adsorbed moisture is about 10 – 100 μm. Caution is
needed, when a corrosion in thicker layers is
modeled, for example the layer of stagnant water
covering a part of a car chassis.
Polarization curves are used directly during the
calculation as a binding condition between the
potential of the electrolyte and the flowing corrosion
current. BEASY CM does not solve the mechanisms
of polarization. Therefore, the polarization curves
have to be measured under conditions as close as
possible to those prevailing during the exposition to
the corrosive environment. Factors influencing the
resulting shape of polarization curve are
temperature, composition of the electrolyte,
composition of surrounding atmosphere and the
thickness of the electrolyte layer. For the simulation
of galvanic corrosion by BEASY CM it is necessary
to have a database of polarization curves for all
included materials covering broad spectrum of
measuring conditions or to have a possibility to
arbitrarily measure the curves of included materials
for every specific situation which is to be simulated.
6.2 Input Data Discussion
Because there is no comprehensive database of
polarization data for materials in TEL in the
literature, the measuring of polarization curves is an
essential part of using BEASY CM. Because of large
serial resistance of the TEL, the measuring in the
thin layer requires special techniques. Contactless
measurement (Stratmann, 1990) or a special type of
corrosion cell (Liu, 2010) are most frequently
mentioned in the literature. There is a possibility to
measure polarization curves in TEL in Testing
Laboratories of Aerospace Research and Test
Establishment. The technique is under permanent
development and the minimum achievable thickness
is decreasing.
As mentioned above, the layer of the electrolyte
is characterized with its sheet resistance. This value
is given by a conductivity of the electrolyte and the
thickness of the layer. Factors influencing the
conductivity of an electrolyte are temperature and
the composition of the electrolyte.
The main issue during solving a real situation by
BEASY CM is to determine the thickness of the
electrolyte layer, the composition of the electrolyte
and consequently its conductivity and the
appropriate polarization curve.
7 CONCLUSIONS
Philosophy of a programme BEASY CM for
mathematical modelling of galvanic corrosion was
introduced. As a special tool for modelling of
galvanic corrosion in TEL, the programme uses
mathematical simplifications resulting from physical
description of the situation. The programme solves
the galvanic corrosion as a 2D problem. This
simplification must be considered as a limiting
factor, when decision should be made, if the
software can be used for modelling of particular
situation or not.
On the other hand the programme need special,
precisely measured input data. This data are
polarization curves measured in TEL and the
measuring conditions should cover a broad spectrum
of corrosive environments. The other disputable
variables are the thickness of TEL and the electrical
conductivity of the electrolyte. It is advisable to have
a database of the thicknesses and electrolyte
ApplicationofMathematicalModellingforSimulationofGalvanicCorrosion
465