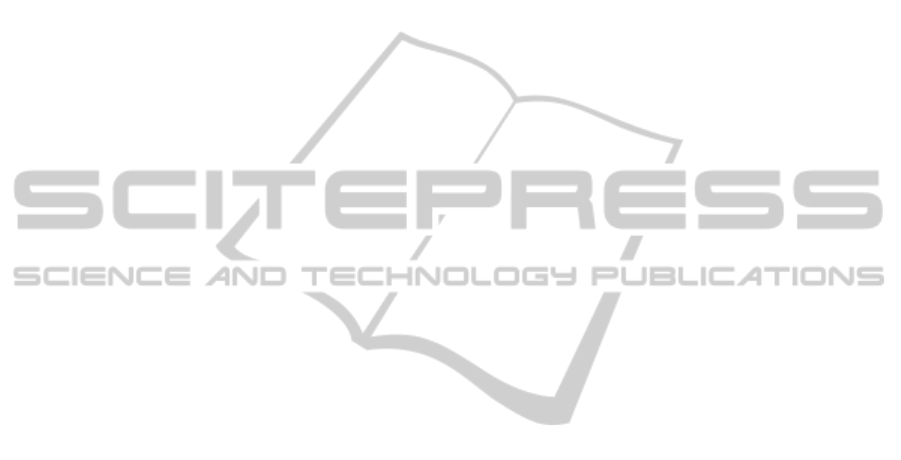
generation prototype, the prototype device is under-
going an optimization process from power consump-
tion/management, data processing and diagnose algo-
rithm perspectives.
ACKNOWLEDGEMENTS
This work has been funded by European seventh
framework programme (FP7) for small medium en-
terprise under research project Mosycousis (Project
reference number: 285848).
REFERENCES
Ayg
¨
un, B. and Gungor, V. C. (2011). Wireless sensor
networks for structure health monitoring: recent ad-
vances and future research directions. Sensor Review,
31(3):261–276.
Bastianini, F., Sedigh, S., Pascale, G., and Perri, G. (2013).
Cost-effective dynamic structural health monitoring
with a compact and autonomous wireless sensor sys-
tem. In Nondestructive Testing of Materials and Struc-
tures, pages 1065–1070. Springer.
Bohse, J. (2013). Acoustic emission. In Handbook of Tech-
nical Diagnostics, pages 137–160. Springer.
Ching, J., To, A., and Glaser, S. (2004). Acoustic emission
source deconvolution: Bayes vs. minimax, fourier vs.
wavelets, and linear vs. nonlinear. Journal of the
Acoustical Society of America, 115(6):3048–3058.
De Silva, C. W. (2010). Vibration monitoring, testing, and
instrumentation. CRC Press.
Grosse, C. U. and Kr
¨
uger, M. (2006). Wireless acoustic
emission sensor networks for structural health moni-
toring in civil engineering. In Proc. European Conf.
on Non-Destructive Testing (ECNDT), DGZfP BB-
103-CD. Citeseer.
Grosse, C. U., Reinhardt, H. W., Motz, M., and Kroplin,
B. (2002). Signal conditioning in acoustic emission
analysis using wavelets. NDT. net, 7(9):1–9.
Im, J.-P., Wang, S.-W., Ryu, S.-T., and Cho, G.-H. (2012).
A 40 mv transformer-reuse self-startup boost con-
verter with mppt control for thermoelectric energy
harvesting. Solid-State Circuits, IEEE Journal of,
47(12):3055–3067.
Ledeczi, A., Hay, T., Volgyesi, P., Hay, D. R., N
´
adas, A.,
and Jayaraman, S. (2009). Wireless acoustic emis-
sion sensor network for structural monitoring. Sensors
Journal, IEEE, 9(11):1370–1377.
L
´
edeczi,
´
A., V
¨
olgyesi, P., Barth, E., N
´
adas, A., Pedchenko,
A., Hay, T., and Jayaraman, S. (2011). Self-sustaining
wireless acoustic emission sensor system for bridge
monitoring. In New Developments in Sensing Tech-
nology for Structural Health Monitoring, pages 15–
39. Springer.
Loutas, T., Kalaitzoglou, J., Sotiriades, G., and Kostopou-
los, V. (2011). The combined use of vibration, acous-
tic emission and oil debris sensor monitored data com-
ing from rotating machinery for the development of a
robust health monitoring system.
Lubieniecki, M. and Uhl, T. (2012). Thermoelectric en-
ergy harvester: Design considerations for a bearing
node. Journal of Intelligent Material Systems and
Structures, 23(16):1813–1825.
Mba, D. and Rao, R. B. (2006). Development of acoustic
emission technology for condition monitoring and di-
agnosis of rotating machines; bearings, pumps, gear-
boxes, engines and rotating structures.
McFadden, P. and Smith, J. (1984). Vibration monitoring
of rolling element bearings by the high-frequency res-
onance techniquea review. Tribology international,
17(1):3–10.
O’Donnell, T. and Wang, W. (2009). Power management,
energy conversion and energy scavenging for smart
systems. Ambient Intelligence with Microsystems,
pages 241–266.
Ramadass, Y. K. and Chandrakasan, A. P. (2011). A battery-
less thermoelectric energy harvesting interface circuit
with 35 mv startup voltage. Solid-State Circuits, IEEE
Journal of, 46(1):333–341.
Rutzig, M. B. (2013). Multicore platforms: Processors,
communication and memories. In Adaptable Embed-
ded Systems, pages 243–277. Springer.
Wang, W., Wang, N., Hayes, M., O’Flynn, B., and
O’Mathuna, C. (2012). Power management for sub-
mw energy harvester with adaptive hybrid energy stor-
age. Journal of Intelligent Material Systems and
Structures.
Weddell, A. S., Magno, M., Merrett, G. V., Brunelli, D.,
Al-Hashimi, B., and Benini, L. (2013). A survey of
multi-source energy harvesting systems. In Design,
Automation and Test in Europe (DATE).
Weddell, A. S., Zhu, D., Merrett, G. V., Beeby, S., and Al-
Hashimi, B. (2012). A practical self-powered sensor
system with a tunable vibration energy harvester. In
PowerMEMS 2012.
Zhu, D., Beeby, S., Tudor, M., and Harris, N. (2012a). Elec-
tromagnetic vibration energy harvesting using an im-
proved halbach array.
Zhu, D., Roberts, S., Mouille, T., Tudor, M. J., and Beeby,
S. P. (2012b). General model with experimental vali-
dation of electrical resonant frequency tuning of elec-
tromagnetic vibration energy harvesters. Smart Mate-
rials and Structures, 21(10):105039.
Multi-sourceEnergyHarvestingPoweredAcousticEmissionSensingSystemforRotatingMachineryCondition
MonitoringApplications
499