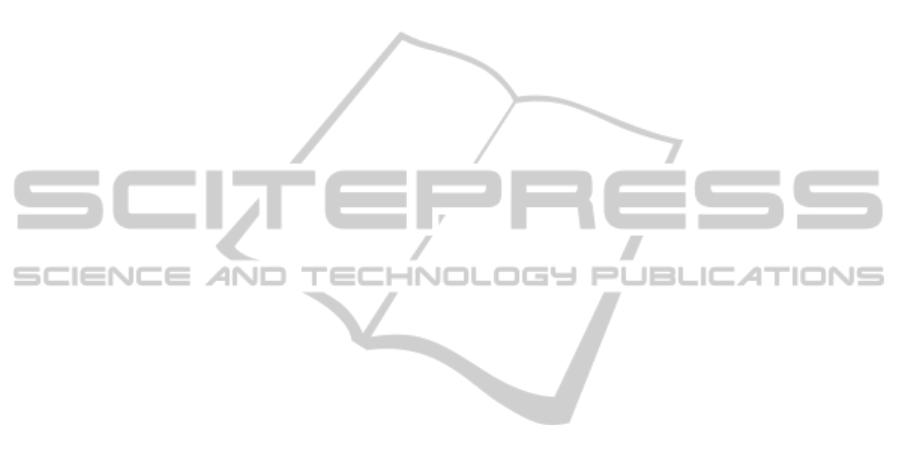
Sharma, V., Sahay, B. S., Sardana, G. D., 2008. “An
Empirical Assessment of the Impact of SCM Practices
on Quality Performance: A Case in the Indian
Automobile Industry,” Supply Chain Forum 9(1), 28 -
40.
Walker, K., 2009. “Ingredients for a Successful Supply
Chain Management System Implementation,” Supply
Chain Forum 10(1), 44 - 50.
Scarsi, R., 2007. “Recovering Supply Chain Cost
Efficiency Through Original Logistics Solutions: A
Case in the Steel Industry,” Supply Chain Forum 8(1),
74 - 82.
Stevens, G. C., 1989. “Integrating the Supply Chain,”
International Journal of Physical Distribution &
Logistics Management 19(8), 3-8.
Potter, A., Mason, R., Naim, M., Lalwani, C., 2004. “The
evolution towards an integrated steel supply chain: A
case study from the UK,” International Journal of
Production Economics 89, 207-216.
Chae, B. K., 2009. “Developing key performance
indicators for the supply chain: and industry
perspective,” Supply Chain Management: An
International Journal 14(6), 422-428.
Ulungu, E.L., Teghem, J., and Fortemps, Ph., 1995.
“Heuristic for multi-objective combinatorial
optimization problems by simulated annealing,” in: J.
Gu, G. Chen, Q. Wei, S. Wang (Eds), MCDM: Theory
and Applications, Sci-Tech, 229–238.
Alrefaei, M. H., and Ali Diabat., 2009. “A Simulated
Annealing Technique for Multi-Objective Simulation
Optimization,” Applied Mathematics and
Computation, 215, 3029-3035.
Yanling, W., Deli, Y., Guoqing, Y., 2010. “Logistics
supply chain management based on multi-constrained
combinatorial optimization and extended simulated
annealing,” 2010 International Conference on
Logistics Systems and Intelligent Management, 188-
192.
Jahangirian, M., Eldabi, T., Naseer, A., Stergiouslas, L.
K., Young, T., 2010. “Simulation in manufacturing
and business: A review,” European Journal of
Operational Research 203, 1-13.
Terzi, S., Cavalieri, S., 2004. “Simulation in the supply
chain context: a survey,” Computers in Industry 53, 3-
16.
Longo, F., Mirabelli, G., 2008. “An advanced supply
chain management tool based on modeling and
simulation,” Computers & Industrial Engineering 54,
570–588.
Diabat, A., Richard, J. P., Codrington, C. W., 2013. “A
Lagrangian relaxation approach to simultaneous
strategic and tactical planning in supply chain
design,” Annals of Operations Research, 203(1), 55-
80.
Jung, J. Y., Blau, G., Pekny, J. F., Reklaitis, G. V.,
Eversdyk, D., 2004. “A simulation based optimization
approach to supply chain management under demand
uncertainty,” Computers & Chemical Engineering 28,
2087-2106.
Yoo, T., Cho, H., Yücesan, E., 2010. “Hybrid algorithm
for discrete event simulation based supply chain
optimization,” Expert Systems with Applications 37,
2354-2361.
Ingalls, R. G., 1998. “The value of simulation in modeling
supply cha
in,” In Proceedings of the 1998 winter
simulation conference, Washington DC, 1371–1375.
Metropolis, N., A. Rosenbluth, M. Rosenbluth, A., Teller,
E., 1953. “Equation of state calculations by fast
computing machines,” Journal of Chemical Physics,
21, 1087-1092.
Eglese, R. W., 1990. “Simulated annealing: a tool for
operational research,” European Journal of
Operational Research 46(3), 271- 279.
Laarhoven, P. J. M. and E. Aarts, 1987. “Simulated
Annealing: Theory and Applications,” D. Reidel
Publishing Company, Holland.
Lanner Group Inc., 2011. http://www.lanner.com/
Heidrich, J., 2002. “Implementation of supply chain
management systems in steel industry,” Industry
Management, 18(5), 46-49.
Chopra, S. and Meindl, P. 2007. Supply Chain
management; Strategy, Planning, and Operations.
Prentice Hall, New Jersey.
ICEIS2013-15thInternationalConferenceonEnterpriseInformationSystems
562