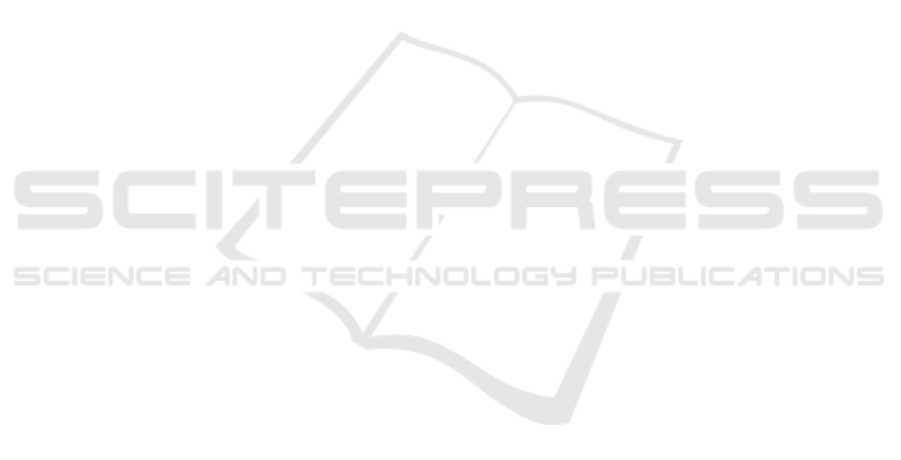
Identification of Fuzzy Measures for Machinery Fault Diagnosis
Masahiro Tsunoyama
1
, Yuki Imai
1
, Hayato Hori
2
, Hirokazu Jinno
2
,
Masayuki Ogawa
2
and Tatsuo Sato
2
1
Niigata Institute of Technology, 1719 Fujihashi, Kashiwazaki, Niigata 945-1195, Japan
2
Flowserve Japan Co.,Ltd. 1-32 Shinbashi, Kashiwazaki, Niigata 945-0056, Japan
Keywords: Fuzzy Measure, Fuzzy Integral, Fault Diagnosis, Vibration Diagnosis.
Abstract: This paper proposes an identification method of fuzzy measure for fault diagnosis of rotating machineries
using vibration spectra method. The membership degrees for spectra in fuzzy set composed of vibration
spectra are obtained from the optimized membership functions. The fuzzy measure is identified by the
proposed method using the partial correlation coefficients between two spectra and the weight of each
spectrum given by skilled engineers. The possibility of faults are determined by the fuzzy integral that is made
by using the membership degrees and fuzzy measures for spectra. This paper also evaluates the method using
field data.
1 INTRODUCTION
Diagnosis of faults in rotating machineries are made
by applying prior knowledge in conjunction with
diagnostic analysis techniques of diagnosing
engineers. The need for diagnosing rotating
machineries is rising due to the increased use of
them in highly reliable systems such as aircrafts and
nuclear power plants. Moreover, due to the increase
of condition based maintenance (CBM) for highly
dependable systems and for cost effective
maintenance, many highly skilled engineers are
required to make accurate diagnoses (Chen et al.,
2002). However, it is difficult to satisfy the current
need of skilled engineers because the requisite
training is lengthy and very expensive.
Several diagnostic systems for rotating
machineries have been developed to satisfy this need
(Liu et al., 2007). Some of them use fuzzy measures
and fuzzy integrals to encompass the existing
knowledge of skilled engineers (Marinai and Singh,
2006). However, they still have several problems,
such as difficulty in isolating faults generating
similar vibration spectra.
This paper proposes an identification method of
fuzzy measures using partial correlation coefficients
of spectra used for fault diagnosis. The possibility of
faults is determined by the fuzzy integral using the
membership degree of spectra and fuzzy measure of
the set of spectra. The membership degrees are
obtained by the optimized membership functions
(Tsunoyama et al., 2010; Tsunoyama et al, 2012),
and fuzzy measures are identified by the partial
correlation coefficients of spectra and the weight of
each spectrum given by skilled engineers.
This paper is organized as follows. The vibration
spectra for faults, and fuzzy measure and fuzzy
integral are described in Section 2. The
identification method of fuzzy measure and variation
of possibility are explained in Section 3. A sample
diagnosis and evaluation of the proposed method are
provided in Section 4. Our conclusions are presented
in Section 5.
2 FAULT DIAGNOSIS
OF ROTATING MACHINERIES
2.1 Faults and Vibration Spectra
Several kinds of faults occur in rotating machineries
including abnormal vibration, oil or water leaks, and
abnormal temperature. The proposed method
diagnoses faults that produce abnormal vibration
since a large number of faults in rotating
machineries are accompanied by vibration.
However, the presence of vibration is not necessarily
indicative of a failure mode when the vibration
power is low. The power level required for
machinery failure is specified by ISO 2372. The
273
Tsunoyama M., Imai Y., Hori H., Jinno H., Ogawa M. and Sato T..
Identification of Fuzzy Measures for Machinery Fault Diagnosis.
DOI: 10.5220/0004629202730278
In Proceedings of the 5th International Joint Conference on Computational Intelligence (FCTA-2013), pages 273-278
ISBN: 978-989-8565-77-8
Copyright
c
2013 SCITEPRESS (Science and Technology Publications, Lda.)