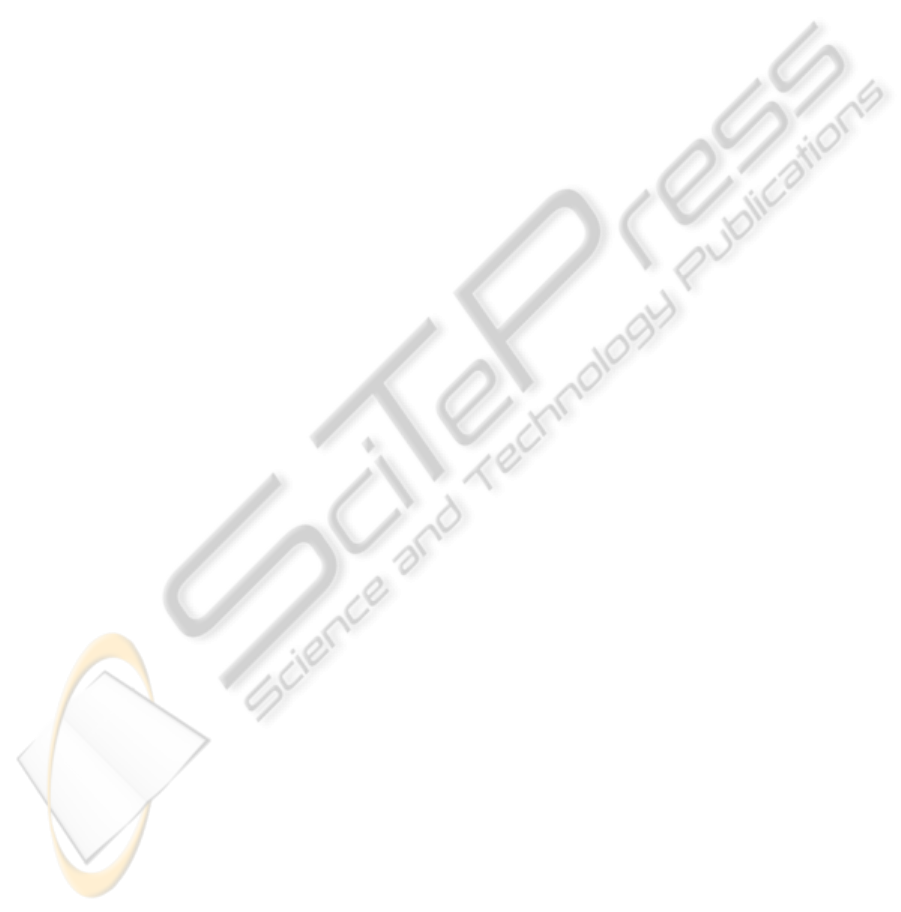
The thermal behaviour of power modules can
change significantly depending on the density of
chips, the used materials and the module geometry.
Starting from the thermal impedance curves,
obtained by 3-D numerical simulation or by
experimental measurements, the methodology will
allow to find a suitable circuital network topology
able to reproduce both the single chip behaviour and
the thermal coupling between different chips.
In summary the main expected outcomes are
two. The first one is the definition of a methodology
to design lumped parameter models reproducing the
thermal behaviour of high power modules.
The second expected outcome is the availability
of particularly simply models for fast simulation of
thermal behaviour of high power modules.
REFERENCES
Y. B. Wu, G. Y. Liu, N. H. Xu and Z. C. Dou, “Thermal
Resistance Analysis and Simulation of IGBT Module
with High Power Density”, Applied Mechanics and
materials Vols 303-306, pp 1902-1907, 2013.
I. Swan, A. Bryant, P. A. Mawby, T. Ueta, T. Nishijima,
and K. Hamada, “A Fast Loss and Temperature
Simulation Method for Power Converters, Part II: 3-D
Thermal Model of Power Module”, IEEE
Transactions on power electronics, vol. 27, no. 1,
January 2012
I. R. Swan, A. T. Bryant, and P. A. Mawby, “Fast 3D
thermal simulation of power module packaging”, Int.
J. Numer. Model., vol 25, pp 378–399, July 2012.
S. Dutta, B. Parkhideh, S. Bhattacharya, G. K.
Moghaddam, R. Gould “Development of a Predictive
Observer Thermal Model for Power Semiconductor
Devices for Overload Monitoring in High Power High
Frequency Converters”, Applied Power Electronics
Conference and Exposition (APEC), pp 2305-2310,
February 2012
U. Drofenik, D. Cottet, A. Musing, J-M. Meyer and J. W.
Kolar, “Computationally Efficent Integration of
Complex Thermal Multi-Chip Power Module Models
into Circuit Simulators”, Power Conversion
Conference, Nagoya, 2007.
Z. Khatir, S. Carubelli and F. Lecoq, “Real-Time
Computation of Thermal Constraints in Multichip
Power Electronics Devices”, IEEE Transaction on
components and packaging technologies, Vol. 27, No.
2, June 2004.
S. Carubelli, Z. Khatir, “Experimental validation of a
thermal modelling method dedicated to multichip
power modules in operating conditions”,
Microelectronics Journal 34, pp.1143–1151, 2003.
R. W. Lewis, K. Morgan, H. R. Thomas and K. N.
Seetharamu, The Finite Element Method in Heat
Transfer Analysis. New York: Wiley, 1996.
C. S. Yun, P. Regli, J. WaldMeyer, and W. Fichtner,
“Static and dynamic thermal characteristics of IGBT
power modules”, In Proc. 11th Int. Symp. Power
Semiconductor Devices & ICs, pp. 37-40, May 1999.
Z. Khatir, S. Lefebvre, “Thermal Analysis of Power
Cycling Effects on High Power IGBT Modules by the
Boundary Element Method”, Semiconductor Thermal
Measurement and Management, Seventeeth Annual
IEEE Symposius, 2001.
F. Profumo, A. Tenconi, S. Facelli, B. Passerini,
“Implementation and Validation of a New Thermal
Model for Analysis, Design, and Characterization of
Multichip Power electronics Devices”, IEEE
Transaction on industry applications, vol. 35, no. 3,
May/June 1999.
N. Y. A. Shammas, M. P. Rodriguez, F. Masana, “A
simple method for evaluating the transient thermal
response of semiconductor devices”, Microelectronics
Reliability 42, pp. 109-117, 2002.
Y. A. Cengel, Heat Transfer: A practical Approach,
Mcgraw-Hill, 2nd edition, 2002.
Infineon Ltd, Thermal equivalent circuit models,
Application Note, v1.0, 2008 published at
http://www.infineon.com.
ABB Ltd, Thermal Design and Temperature Ratings of
IGBT Modules, application note published at
http://www.abb.com/semiconductors.
OntheInvestigationofLumpedParameterModelsforThermalCharacterizationofHighPowerModules
7