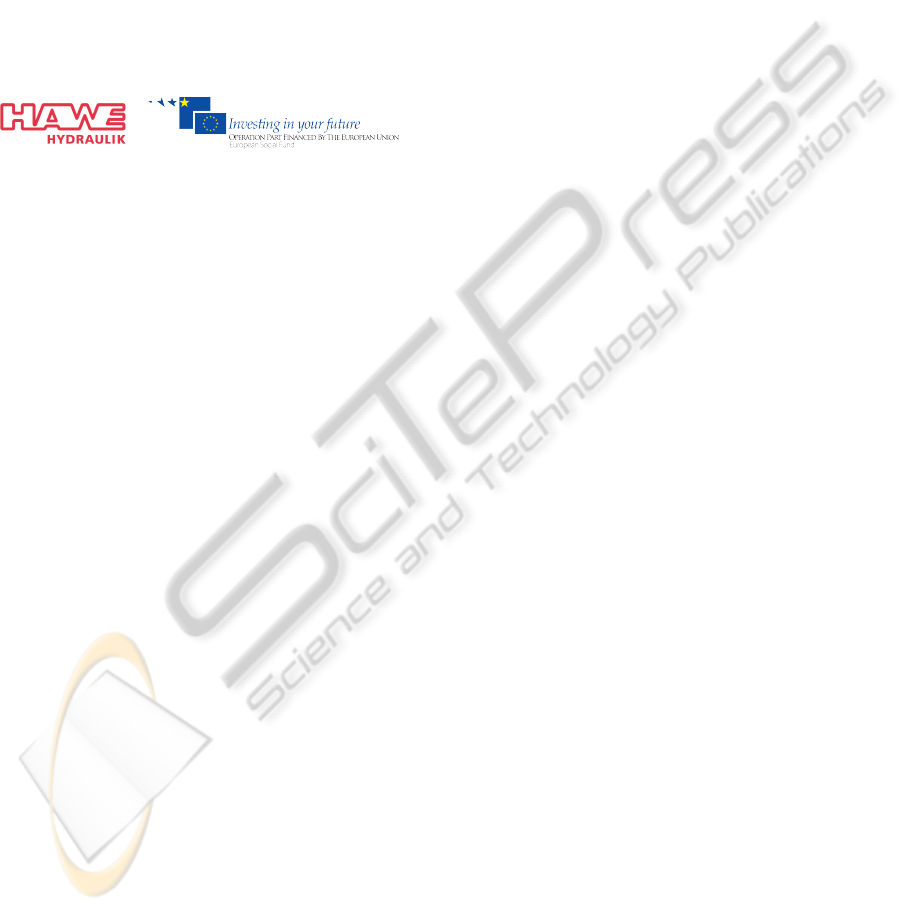
these two. A further contribution to the hydraulic sys-
tem developers’ community will be an experimentally
proven mathematical model for the simulations of dif-
ferent hydraulic drive concepts. Such a model may
be used for optimising the energy-efficiencies of ex-
isting and new hydraulic machinery, as well as effi-
ciency prediction when building new hydraulic sys-
tems. Moreover it may also be used for determining
the most suitable drive concept for a hydraulic system
with a predefined operating cycle.
ACKNOWLEDGEMENTS
Operation part financed by the European Union,
European Social Fund. Operation implemented in the
framework of the Operational Programme for Human
Resources Development for the Period 2007-2013,
Priority axis 1: Promoting entrepreneurship and
adaptability, Main type of activity 1.1.: Experts and
researchers for competitive enterprises.
REFERENCES
Delaleau, E., Louis, J.-P., and Ortega, R. (2001). Modelling
and control of induction motors. International Jour-
nal of Applied Mathematics and Computer Science,
11(1):105–129.
Diaz, A., Saltares, R., Rodriguez, C., Nunez, R., Ortiz-
Rivera, E., and Gonzalez-Llorente, J. (2009). Induc-
tion motor equivalent circuit for dynamic simulation.
In Electric Machines and Drives Conference, 2009.
IEMDC ’09. IEEE International, pages 858–863.
Ferreira, F. J. T. E., Fong, J., and De Almeida, A. (2011).
Ecoanalysis of variable-speed drives for flow regula-
tion in pumping systems. Industrial Electronics, IEEE
Transactions on, 58(6):2117–2125.
Jeong, H.-S. and Kim, H.-E. (2007). A novel performance
model given by the physical dimensions of hydraulic
axial piston motors: Experimental analysis. Journal of
Mechanical Science and Technology, 21(4):630–641.
Lovrec, D., Kastrevc, M., and Hribernik, D. (2005). Com-
parison of variable electrohydraulic supply systems by
example of pressure control. Ventil, 11(3):153–160.
Lovrec, D., Kastrevc, M., and Ulaga, S. (2009). Electro-
hydraulic load sensing with a speed-controlled hy-
draulic supply system on forming-machines. The In-
ternational Journal of Advanced Manufacturing Tech-
nology, 41(11-12):1066–1075.
Lovrec, D. and Ulaga, S. (2007). Pressure control in hy-
draulic systems with variable or constant pumps? Ex-
perimental Techniques, 31(2):33–41.
Majumdar, S. R. (2000). Oil Hydraulic Systems: Princi-
ples and Maintenance. McGraw-Hill Education (In-
dia) Pvt Limited.
Rydberg, K.-E. (2009). Efficiencies for variable hydraulic
pumps and motors mathematical models and opera-
tion conditions.
Shen, Z., Xiong, Y., Cheng, X., Fu, Y., and Kumar, P.
(2006). Power mosfet switching loss analysis: A new
insight. In Industry Applications Conference, 2006.
41st IAS Annual Meeting. Conference Record of the
2006 IEEE, volume 3, pages 1438–1442.
Song, X., Yao, X., Li, Z., and Wang, J. (2008). Equip-
ping variable-speed pumping source to reduce use-
less power of missile-loaded hydraulic actuator. In
Systems and Control in Aerospace and Astronautics,
2008. ISSCAA 2008. 2nd International Symposium on,
pages 1–5.
Stekl, P. (2007). 3-phase AC Induction Vector Control Drive
with Single Shunt Current Sensing.
Ta
ˇ
sner, T. and Lovrec, D. (2011). Comparison of modern
electrohydraulic systems. In 34th International Con-
ference on Production Engineering.
Wilson, E. W. (1949). Performance criteria for positive dis-
placement pumps and fluid motors. In ASME Semi-
annual Meeting, volume 71.
Xu, M., Chen, G., and Ni, J. (2010). Hierarchical control
of energy regulation based variable-speed electrohy-
draulic drive. In Information and Automation (ICIA),
2010 IEEE International Conference on, pages 2401–
2405.
AdvancedControlConceptsSuitableforEnergyEfficientHydraulicSystems
11