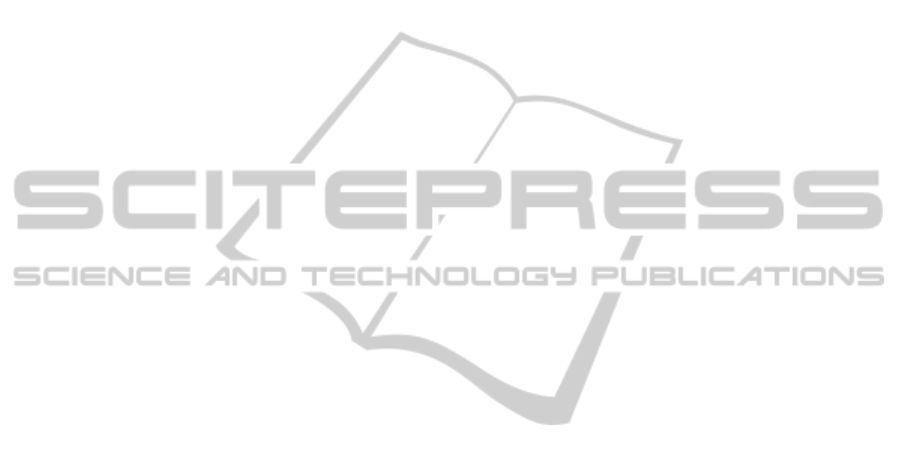
ACKNOWLEDGEMENTS
This research was supported by the National Center
of Competence in Research Robotics (NCCR
Robotics).
REFERENCES
Bouri, M., Stauffer, Y., Schmitt, C., Allemand, Y.,
Gnemmi, S., Clavel, R., Metrailler, P. & Brodard, R.
The Walktrainer: A Robotic System for Walking
Rehabilitation. International Conference on Robotics
and Biomimetics Robio, 2006. IEEE, 1616-1621.
Chapuis, D., Michel, X., Gassert, R., Chew, C.-M.,
Burdet, E. & Bleuler, H. A Haptic Knob with a Hybrid
Ultrasonic Motor and Powder Clutch Actuator.
Eurohaptics Conference, 2007 And Symposium on
Haptic Interfaces for Virtual Environment And
Teleoperator Systems. World Haptics 2007. Second
Joint, 2007. IEEE, 200-205.
Fauteux, P., Lauria, M., Heintz, B. & Michaud, F. 2010.
Dual-Differential Rheological Actuator For High-
Performance Physical Robotic Interaction. Robotics,
IEEE Transactions on, 26, 607-618.
Fauteux, P., Lauria, M., Legault, M.-A., Michaud, F. &
Lavoie, M.-A. 2009. Dual Differential Semi-Active
Actuator Fit For Interaction Tasks And Fast Motion.
Google Patents.
Herr, H. 2009. Exoskeletons And Orthoses: Classification,
Design Challenges and Future Directions. Journal Of
Neuroengineering and Rehabilitation, 6.
Jezernik, S., Colombo, G., Keller, T., Frueh, H. & Morari,
M. 2003. Robotic Orthosis Lokomat: A Rehabilitation
And Research Tool. Neuromodulation: Technology at
the Neural Interface, 6, 108-115.
Judgeroy, J. O., Davis, B. & Õunpuu, S. 1996. Step
Length Reductions in Advanced Age: The Role Of
Ankle and Hip Kinetics. The Journals of Gerontology
Series A: Biological Sciences and Medical Sciences,
51, M303.
Olivier, J., Bouri, M., Ortlieb, A., Bleuler, H. & Clavel, R.
2013. Development of an Assistive Motorized Hip
Orthosis. International Conference on Rehabilitation
Robotics ICORR. Seattle.
Ryder, M. C. & Sup, F. 2013. Leveraging Gait Dynamics
to Improve Efficiency and Performance of Powered
Hip Exoskeletons International Conference on
Rehabilitation Robotics ICORR. Seattle.
Stauffer, Y., Allemand, Y., Bouri, M., Fournier, J., Clavel,
R., Metrailler, P., Brodard, R. & Reynard, F. 2009. the
Walktrainer—A New Generation of Walking
Reeducation Device Combining Orthoses and Muscle
Stimulation. Neural Systems and Rehabilitation
Engineering, IEEE Transactions on, 17, 38-45.
Tucker, M. R. & Gassert, R. Differential-damper
Topologies for Actuators in Rehabilitation Robotics.
Engineering in Medicine and Biology Society
(EMBC), 2012 Annual International Conference of the
IEEE, 2012. IEEE, 3081-3085.
Vallery, H., Veneman, J., Van Asseldonk, E.,
Ekkelenkamp, R., Buss, M. & Van Der Kooij, H.
2008. Compliant Actuation of Rehabilitation Robots.
Robotics & Automation Magazine, IEEE, 15, 60-69.
Zanotto, D., Lenzi, T., Stegall, P. & Agrawal, S. K. 2013.
Improving Transparency of Powered Exoskeletons
Using Force/Torque Sensors on the Supporting Cuffs.
International Conference on Rehabilitation Robotics
ICORR. Seattle.
ADouble-differentialActuationforanAssistiveHipOrthosis-SpecificitiesandImplementation
189