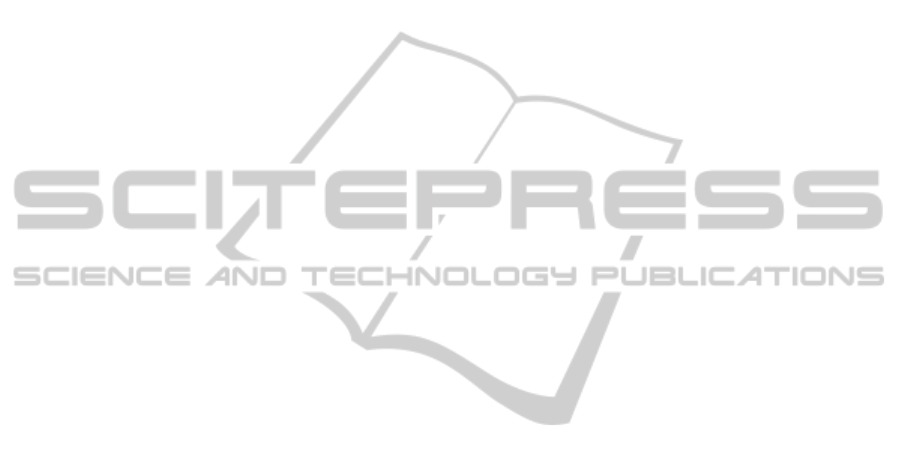
cycle on-line and control the knee and ankle modules,
as well as their mechanical coupling. Recorded data
and feedback from both healthy and amputated sub-
jects showed promising performance and encourage a
more extensive experimental characterization includ-
ing the effect of pretension on the energetics of the
gait cycle and the effects of the energy transfer mech-
anism. A powered knee based on the passive mecha-
nism of this design is currently in development. This
will allow sit to stand and stair climbing operations in
addition to efficient walking.
ACKNOWLEDGEMENTS
This work has been funded by the European Commis-
sions 7th Framework Program as part of the project
CYBERLEGs under grant no. 287894. The second
author is funded by a Ph.D. grant of the Agency for
Innovation by Science and Technology in Flanders
(IWT).
REFERENCES
Au, S., Berniker, M., and Herr, H. (2008). Powered ankle-
foot prosthesis to assist level-ground and stair-descent
gaits. Neural Networks, 21(4):654–66.
Au, S. and Herr, H. (2008). Powered ankle-foot prosthesis.
IEEE Robotics & Automation Magazine, 15(3):52–59.
Bellman, R., Holgate, M., and Sugar, T. (2008). SPARKy 3:
Design of an active robotic ankle prosthesis with two
actuated degrees of freedom using regenerative kinet-
ics. IEEE RAS & EMBS, pages 511–516.
Cherelle, P., Matthys, A., and et al. (2012). The AMP-Foot
2.0: Mimicking Intact Ankle Behavior with a Powered
Transtibial Prosthesis. In IEEE International Confer-
ence on Biomedical Robotics and Biomechatronics.
Donati, M. et al. (2013). A flexible sensor technology for
the distributed measurement of interaction pressure.
Sensors, 13(1):1021–1045.
Herr, H. M. and Grabowski, A. M. (2012). Bionic ankle-
foot prosthesis normalizes walking gait for persons
with leg amputation. Proc. Roy. Soc. Lon. B, 279:457–
464.
Hitt, J. K., Bellman, R., and et al. (2007). The SPARKy
Spring Ankle with Regenerative Kinetics project: De-
sign and analysis of a robotic transtibial prosthesis
with regenerative kinetics. In ASME IDETC/CIE, Las
Vegas, Nevada, USA, pages 1587–1596.
Hollander, K. W., Ilg, R., Sugar, T. G., and Herring, D.
(2006). An efficient robotic tendon for gait assistance.
Journal of biomechanical engineering, 128(5):788–
91.
IWalk (2013). Biom. http://www.iwalk.com/.
Kaufman, K. R., Levine, J. A., and et al. (2008). Energy Ex-
penditure and Activity of Transfemoral Amputees Us-
ing Mechanical and Microprocessor-Controlled Pros-
thetic Knees. Archives of Physical Medicine and Re-
habilitation, 89(July):1380–1385.
Matthys, A., Cherelle, P., Van Damme, M., Vanderborght,
B., and Lefeber, D. (2012). Concept and design of the
HEKTA (Harvest Energy from the Knee and Trans-
fer it to the Ankle) transfemoral prosthesis. In IEEE
International Conference on Biomedical Robotics and
Biomechatronics.
Ossur (2013). Power knee. www.ossur.com.
Sup, F., Bohara, A., and Goldfarb, M. (2008). Design and
Control of a Powered Transfemoral Prosthesis. In-
ternational Journal of Robotics Research, 27(2):263–
273.
Unal, R., Behrens, S. M., Carloni, R., Hekman, E. E. G.,
Stramigioli, S., and Koopman, H. F. J. M. (2010). Pro-
totype Design and Realization of an Innovative En-
ergy Efficient Transfemoral Prosthesis. In IEEE RAS
& EMBS.
Van Ham, R., Vanderborght, B., van Damme, M., Verrelst,
B., and Lefeber, D. (2007). MACCEPA, the mechan-
ically adjustable compliance and controllable equilib-
rium position actuator: Design and implementation in
a biped robot. Robotics and Autonomous Systems, 55
(10):761–768.
Vanderborght, B., Bicchi, A., and et al. (2013). Variable
Impedance Actuators : a Review. Robotics and Au-
tonomous Systems, (Accepted June 2013):1–39.
Villalpando, E. C. M., Weber, J., and etal. (2008). Design of
an Agonist-Antagonist Active Knee Prosthesis. IEEE
RAS & EMBS, pages 529–534.
Winter, D.A. (2005). Biomechanics and Motor Control
of Human Movement. John Wiley and Sons, United
States of America.
NEUROTECHNIX2013-InternationalCongressonNeurotechnology,ElectronicsandInformatics
228